UNITED STATES
SECURITIES AND EXCHANGE COMMISSION
Washington, D.C. 20549
Form 10-K
|
| |
ý | ANNUAL REPORT PURSUANT TO SECTION 13 OR 15(d) OF THE SECURITIES EXCHANGE ACT OF 1934 |
FOR THE ANNUAL PERIOD ENDED DECEMBER 31, 2016
|
| |
o | TRANSITION REPORT PURSUANT TO SECTION 13 OR 15(d) OF THE SECURITIES EXCHANGE ACT OF 1934 |
Commission File No. 001-37917
Mammoth Energy Services, Inc.
(Exact name of registrant as specified in its charter)
|
| | |
Delaware | | 32-0498321 |
(State or other jurisdiction of incorporation or organization) | | (I.R.S. Employer Identification No.) |
| | |
4727 Gaillardia Parkway, Suite 200 Oklahoma City, Oklahoma | (405) 608-6007 | 73142 |
(Address of principal executive offices) | (Registrant’s telephone number, including area code) | (Zip Code) |
| | |
| Securities registered pursuant to Section 12(b) of the Act: | |
Title of Each Class | | Name of Each Exchange on Which Registered |
Common Stock, par value $0.01 per share | | The NASDAQ Stock Market LLC |
| Securities registered pursuant to Section 12(g) | |
| of the Act: None | |
Indicate by check mark if the registrant is a well-known seasoned issuer, as defined in Rule 405 of the Securities Act. Yes ¨ No ý
Indicate by check mark if the registrant is not required to file reports pursuant to Section 13 or Section 15(d) of the Act. Yes ¨ No ý
Indicate by check mark whether the registrant (1) has filed all reports required to be filed by Section 13 or 15(d) of the Securities Exchange Act of 1934 during the preceding 12 months (or for such shorter period that the registrant was required to file such reports), and (2) has been subject to such filing requirements for the past 90 days. Yes ¨ No ý
Indicate by check mark whether the registrant has submitted electronically and posted on its corporate Web site, if any, every Interactive Data File required to be submitted and posted pursuant to Rule 405 of Regulation S-T (§ 232.405 of this chapter) during the preceding 12 months (or for such shorter period that the registrant was required to submit and post such files). Yes ý No ¨
Indicate by check mark if disclosure of delinquent filers pursuant to Item 405 of Regulation S-K (§ 229.405 of this chapter) is not contained herein, and will not be contained, to the best of registrant’s knowledge, in definitive proxy or information statements incorporated by reference in Part III of this Form 10-K or any amendment to this Form 10-K. Yes ý No ¨
Indicate by check mark whether the registrant is a large accelerated filer, accelerated filer, non-accelerated filer, or smaller reporting company. See the definitions of “large accelerated filer,” “accelerated filer” and “smaller reporting company” in Rule 12b-2 of the Exchange Act. |
| | | | | | |
Large accelerated filer | | o | | Accelerated filer | | o |
| | | | | | |
Non-accelerated filer | | ý | | Smaller reporting company | | o |
Indicate by check mark whether the registrant is a shell company (as defined in Rule 12b-2 of the Exchange Act). Yes ¨ No ý
As of June 30, 2016, the last business day of the registrant’s most recently completed second fiscal quarter, there was no public market for the registrant’s common stock. The registrant’s common stock began trading on the NASDAQ Global Select Market on October 19, 2016. The aggregate market value of the registrant's common stock held by non-affiliates of the registrant as of December 31, 2016, based on the closing price of the common stock on the NASDAQ Global Select Market on December 30, 2016, was $121,331,674.
As of February 21, 2017, there were 37,500,000 shares of our $0.01 par value common stock outstanding.
DOCUMENTS INCORPORATION BY REFERENCE
Portions of Mammoth Energy Services, Inc.'s Proxy Statement for the 2017 Annual Meeting of Stockholders are incorporated by reference in Items 10, 11, 12, 13 and 14 of Part III of this Form 10-K.
TABLE OF CONTENTS
|
| | |
|
| | |
| | Page |
| | |
| | |
| | |
| |
Item 1. | | |
Item 1A. | | |
Item 1B. | | |
Item 2. | | |
Item 3. | | |
Item 4. | | |
| |
| |
Item 5. | | |
Item 6. | | |
Item 7. | | |
Item 7A. | | |
Item 8. | | |
Item 9. | | |
Item 9A. | | |
Item 9B. | | |
| | |
| |
Item 10. | | |
Item 11. | | |
Item 12. | | |
Item 13. | | |
Item 14. | | |
| | |
| |
Item 15. | | |
| |
| |
GLOSSARY OF OIL AND NATURAL GAS TERMS
|
| |
The following is a glossary of certain oil and natural gas industry terms used in this report: |
Blowout | An uncontrolled flow of reservoir fluids into the wellbore, and sometimes catastrophically to the surface. A blowout may consist of salt water, oil, natural gas or a mixture of these. Blowouts can occur in all types of exploration and production operations, not just during drilling operations. If reservoir fluids flow into another formation and do not flow to the surface, the result is called an underground blowout. If the well experiencing a blowout has significant open-hole intervals, it is possible that the well will bridge over (or seal itself with rock fragments from collapsing formations) down-hole and intervention efforts will be averted. |
Bottomhole assembly | The lower portion of the drillstring, consisting of (from the bottom up in a vertical well) the bit, bit sub, a mud motor (in certain cases), stabilizers, drill collar, heavy-weight drillpipe, jarring devices (“jars”) and crossovers for various threadforms. The bottomhole assembly must provide force for the bit to break the rock (weight on bit), survive a hostile mechanical environment and provide the driller with directional control of the well. Oftentimes the assembly includes a mud motor, directional drilling and measuring equipment, measurements-while-drilling tools, logging-while-drilling tools and other specialized devices. |
Cementing | To prepare and pump cement into place in a wellbore. |
Coiled tubing | A long, continuous length of pipe wound on a spool. The pipe is straightened prior to pushing into a wellbore and rewound to coil the pipe back onto the transport and storage spool. Depending on the pipe diameter (1 in. to 4 1/2 in.) and the spool size, coiled tubing can range from 2,000 ft. to 20,000 ft. (610 m to 6,096 m) or greater length. |
Completion | A generic term used to describe the assembly of down-hole tubulars and equipment required to enable safe and efficient production from an oil or gas well. The point at which the completion process begins may depend on the type and design of the well. |
Directional drilling | The intentional deviation of a wellbore from the path it would naturally take. This is accomplished through the use of whipstocks, bottomhole assembly (BHA) configurations, instruments to measure the path of the wellbore in three-dimensional space, data links to communicate measurements taken down-hole to the surface, mud motors and special BHA components and drill bits, including rotary steerable systems, and drill bits. The directional driller also exploits drilling parameters such as weight on bit and rotary speed to deflect the bit away from the axis of the existing wellbore. In some cases, such as drilling steeply dipping formations or unpredictable deviation in conventional drilling operations, directional-drilling techniques may be employed to ensure that the hole is drilled vertically. While many techniques can accomplish this, the general concept is simple: point the bit in the direction that one wants to drill. The most common way is through the use of a bend near the bit in a down-hole steerable mud motor. The bend points the bit in a direction different from the axis of the wellbore when the entire drillstring is not rotating. By pumping mud through the mud motor, the bit turns while the drillstring does not rotate, allowing the bit to drill in the direction it points. When a particular wellbore direction is achieved, that direction may be maintained by rotating the entire drillstring (including the bent section) so that the bit does not drill in a single direction off the wellbore axis, but instead sweeps around and its net direction coincides with the existing wellbore. Rotary steerable tools allow steering while rotating, usually with higher rates of penetration and ultimately smoother boreholes. |
Down-hole | Pertaining to or in the wellbore (as opposed to being on the surface). |
Down-hole motor | A drilling motor located in the drill string above the drilling bit powered by the flow of drilling mud. Down-hole motors are used to increase the speed and efficiency of the drill bit or can be used to steer the bit in directional drilling operations. Drilling motors have become very popular because of horizontal and directional drilling applications and the increase of day rates for drilling rigs. |
Drilling rig | The machine used to drill a wellbore. |
Drillpipe or Drill pipe | Tubular steel conduit fitted with special threaded ends called tool joints. The drillpipe connects the rig surface equipment with the bottomhole assembly and the bit, both to pump drilling fluid to the bit and to be able to raise, lower and rotate the bottomhole assembly and bit. |
Drillstring or Drill string | The combination of the drillpipe, the bottomhole assembly and any other tools used to make the drill bit turn at the bottom of the wellbore. |
Horizontal drilling | A subset of the more general term “directional drilling,” used where the departure of the wellbore from vertical exceeds about 80 degrees. Note that some horizontal wells are designed such that after reaching true 90-degree horizontal, the wellbore may actually start drilling upward. In such cases, the angle past 90 degrees is continued, as in 95 degrees, rather than reporting it as deviation from vertical, which would then be 85 degrees. Because a horizontal well typically penetrates a greater length of the reservoir, it can offer significant production improvement over a vertical well. |
Hydraulic fracturing | A stimulation treatment routinely performed on oil and gas wells in low permeability reservoirs. Specially engineered fluids are pumped at high pressure and rate into the reservoir interval to be treated, causing a vertical fracture to open. The wings of the fracture extend away from the wellbore in opposing directions according to the natural stresses within the formation. Proppant, such as grains of sand of a particular size, is mixed with the treatment fluid to keep the fracture open when the treatment is complete. Hydraulic fracturing creates high-conductivity communication with a large area of formation and bypasses any damage that may exist in the near-wellbore area. |
Hydrocarbon | A naturally occurring organic compound comprising hydrogen and carbon. Hydrocarbons can be as simple as methane, but many are highly complex molecules, and can occur as gases, liquids or solids. Petroleum is a complex mixture of hydrocarbons. The most common hydrocarbons are natural gas, oil and coal. |
Mud motors | A positive displacement drilling motor that uses hydraulic horsepower of the drilling fluid to drive the drill bit. Mud motors are used extensively in directional drilling operations. |
|
| |
Natural gas liquids | Components of natural gas that are liquid at surface in field facilities or in gas processing plants. Natural gas liquids can be classified according to their vapor pressures as low (condensate), intermediate (natural gasoline) and high (liquefied petroleum gas) vapor pressure. |
Nitrogen pumping unit | A high-pressure pump or compressor unit capable of delivering high-purity nitrogen gas for use in oil or gas wells. Two basic types of units are commonly available: a nitrogen converter unit that pumps liquid nitrogen at high pressure through a heat exchanger or converter to deliver high-pressure gas at ambient temperature, and a nitrogen generator unit that compresses and separates air to provide a supply of high pressure nitrogen gas. |
Plugging | The process of permanently closing oil and gas wells no longer capable of producing in economic quantities. Plugging work can be performed with a well servicing rig along with wireline and cementing equipment; however, this service is typically provided by companies that specialize in plugging work. |
Plug | A down-hole packer assembly used in a well to seal off or isolate a particular formation for testing, acidizing, cementing, etc.; also a type of plug used to seal off a well temporarily while the wellhead is removed. |
Pressure pumping | Services that include the pumping of liquids under pressure. |
Producing formation | An underground rock formation from which oil, natural gas or water is produced. Any porous rock will contain fluids of some sort, and all rocks at considerable distance below the Earth’s surface will initially be under pressure, often related to the hydrostatic column of ground waters above the reservoir. To produce, rocks must also have permeability, or the capacity to permit fluids to flow through them. |
Proppant | Sized particles mixed with fracturing fluid to hold fractures open after a hydraulic fracturing treatment. In addition to naturally occurring sand grains, man-made or specially engineered proppants, such as resin-coated sand or high-strength ceramic materials like sintered bauxite, may also be used. Proppant materials are carefully sorted for size and sphericity to provide an efficient conduit for production of fluid from the reservoir to the wellbore. |
Resource play | Accumulation of hydrocarbons known to exist over a large area. |
Shale | A fine-grained, fissile, sedimentary rock formed by consolidation of clay- and silt-sized particles into thin, relatively impermeable layers. |
Tight oil | Conventional oil that is found within reservoirs with very low permeability. The oil contained within these reservoir rocks typically will not flow to the wellbore at economic rates without assistance from technologically advanced drilling and completion processes. Commonly, horizontal drilling coupled with multistage fracturing is used to access these difficult to produce reservoirs. |
Tight sands | A type of unconventional tight reservoir. Tight reservoirs are those which have low permeability, often quantified as less than 0.1 millidarcies. |
Tubulars | A generic term pertaining to any type of oilfield pipe, such as drillpipe, drill collars, pup joints, casing, production tubing and pipeline. |
Unconventional resource | An umbrella term for oil and natural gas that is produced by means that do not meet the criteria for conventional production. What has qualified as “unconventional” at any particular time is a complex function of resource characteristics, the available exploration and production technologies, the economic environment, and the scale, frequency and duration of production from the resource. Perceptions of these factors inevitably change over time and often differ among users of the term. At present, the term is used in reference to oil and gas resources whose porosity, permeability, fluid trapping mechanism, or other characteristics differ from conventional sandstone and carbonate reservoirs. Coalbed methane, gas hydrates, shale gas, fractured reservoirs and tight gas sands are considered unconventional resources. |
Wellbore | The physical conduit from surface into the hydrocarbon reservoir. |
Well stimulation | A treatment performed to restore or enhance the productivity of a well. Stimulation treatments fall into two main groups, hydraulic fracturing treatments and matrix treatments. Fracturing treatments are performed above the fracture pressure of the reservoir formation and create a highly conductive flow path between the reservoir and the wellbore. Matrix treatments are performed below the reservoir fracture pressure and generally are designed to restore the natural permeability of the reservoir following damage to the near wellbore area. Stimulation in shale gas reservoirs typically takes the form of hydraulic fracturing treatments. |
Wireline | A general term used to describe well-intervention operations conducted using single-strand or multi-strand wire or cable for intervention in oil or gas wells. Although applied inconsistently, the term commonly is used in association with electric logging and cables incorporating electrical conductors. |
Workover | The process of performing major maintenance or remedial treatments on an oil or gas well. In many cases, workover implies the removal and replacement of the production tubing string after the well has been killed and a workover rig has been placed on location. Through-tubing workover operations, using coiled tubing, snubbing or slickline equipment, are routinely conducted to complete treatments or well service activities that avoid a full workover where the tubing is removed. This operation saves considerable time and expense. |
CAUTIONARY NOTE REGARDING FORWARD-LOOKING STATEMENTS
Various statements contained in this Annual Report on Form 10-K (this "annual report" or "report") that express a belief, expectation, or intention, or that are not statements of historical fact, are forward-looking statements within the meaning of Section 27A of the Securities Act of 1933, as amended, or the Securities Act, and Section 21E of the Securities Exchange Act of 1934, or the Exchange Act.
Forward-looking statements may include statements about our:
| |
• | planned acquisitions and future capital expenditures; |
| |
• | ability to obtain permits and governmental approvals; |
| |
• | future operating results; and |
| |
• | plans, objectives, expectations and intentions. |
All of these types of statements, other than statements of historical fact included in this annual report, are forward-looking statements. These forward-looking statements may be found in the “Business,” “Risk Factors,” “Management’s Discussion and Analysis of Financial Condition and Results of Operations,” and other sections of this annual report. In some cases, you can identify forward-looking statements by terminology such as “may,” "will," “could,” “should,” “expect,” “plan,” “project,” “budget,” “intend,” “anticipate,” “believe,” “estimate,” “predict,” “potential,” “pursue,” “target,” “seek,” “objective” or “continue,” the negative of such terms or other comparable terminology.
The forward-looking statements contained in this annual report are largely based on our expectations, which reflect estimates and assumptions made by our management. These estimates and assumptions reflect our best judgment based on currently known market conditions and other factors. Although we believe such estimates and assumptions to be reasonable, they are inherently uncertain and involve a number of risks and uncertainties that are beyond our control. In addition, our management’s assumptions about future events may prove to be inaccurate. Our management cautions all readers that the forward-looking statements contained in this annual report are not guarantees of future performance, and we cannot assure any reader that such statements will be realized or the forward-looking events and circumstances will occur. Actual results may differ materially from those anticipated or implied in the forward-looking statements due to the many factors including those described in Item 1A. “Risk Factors” and Item 7. "Management's Discussion and Analysis of Financial Condition and Results of Operations" and elsewhere in this annual report. All forward-looking statements speak only as of the date of this annual report. We do not intend to publicly update or revise any forward-looking statements as a result of new information, future events or otherwise. These cautionary statements qualify all forward-looking statements attributable to us or persons acting on our behalf.
PART I.
The historical financial information for periods prior to October 12, 2016, contained in this annual report relates to Mammoth Energy Partners LP, a Delaware limited partnership, or the Partnership. On October 12, 2016, the Partnership was converted into a Delaware limited liability company named Mammoth Energy Partners LLC, or Mammoth LLC, and then each member of Mammoth LLC contributed all of its membership interests in Mammoth LLC to Mammoth Energy Services, Inc., a Delaware corporation, or Mammoth Inc. Prior to the conversion and the contribution, Mammoth Inc. was a wholly-owned subsidiary of the Partnership. Following the conversion and the contribution, Mammoth LLC (as the converted successor to the Partnership) became a wholly-owned subsidiary of Mammoth Inc.
On October 13, 2016, Mammoth Inc. priced 7,750,000 shares of its common stock in its initial public offering, or the "IPO" at a price to the public of $15.00 per share and, on October 14, 2016, Mammoth Inc.’s common stock began trading on The Nasdaq Global Select Market under the symbol “TUSK.” On October 19, 2016, Mammoth Inc. closed its IPO. Unless the context otherwise requires, references in this report to “we,” “our,” “us” or like terms, when used in a historical context for periods prior to October 12, 2016 refer to the Partnership and its subsidiaries. References in this report to “we,” “our,” “us” or like terms, when used for periods beginning on or after October 12, 2016 refer to Mammoth Inc. and its subsidiaries.
Item 1. Business
Overview
We are an integrated, growth-oriented oilfield service company serving companies engaged in the exploration and development of North American onshore unconventional oil and natural gas reserves. Our primary business objective is to grow our operations and create value for stockholders through organic opportunities and accretive acquisitions. Our suite of services includes pressure pumping services, well services, natural sand proppant services, contract land and directional drilling services and other energy services. Our pressure pumping division provides hydraulic fracturing services. Our well services division provides pressure control services, flowback services and equipment rentals. Our natural sand proppant services division sells, distributes and is capable of producing proppant for hydraulic fracturing. Our contract land and directional drilling services division provides drilling rigs and crews for operators as well as rental equipment, such as mud motors and operational tools, for both vertical and horizontal drilling. Our other energy services division provides housing, kitchen and dining, and recreational service facilities for oilfield workers located in remote areas away from readily available lodging. We believe that the services we offer play a critical role in increasing the ultimate recovery and present value of production streams from unconventional resources. Our complementary suite of completion and production and drilling related services provides us with the opportunity to cross-sell our services and expand our customer base and geographic positioning.
“Unconventional resources” references the different manner by which they are exploited as compared to the extraction of conventional resources. In unconventional drilling, the wellbore is generally drilled to specific objectives within narrow parameters, often across long, lateral intervals within narrow horizontal formations offering greater contact area with the producing formation. Typically, the well is then hydraulically fractured at multiple stages to optimize production.
Our facilities and service centers are strategically located in Ohio, Oklahoma, Wisconsin, Minnesota, West Virginia, Texas and Alberta, Canada primarily to serve the following resource plays:
| |
• | The Utica Shale in Eastern Ohio; |
| |
• | The Permian Basin in West Texas; |
| |
• | The Appalachian Basin in the Northeast; |
| |
• | The Arkoma Basin in Arkansas and Oklahoma; |
| |
• | The Anadarko Basin in Oklahoma; |
| |
• | The Marcellus Shale in West Virginia and Pennsylvania; |
| |
• | The Granite Wash and Mississippi Shale in Oklahoma and Texas; |
| |
• | The Cana Woodford and Woodford Shales and the Cleveland Sand in Oklahoma; |
| |
• | The SCOOP/STACK in Oklahoma; |
| |
• | The Eagle Ford Shale in Texas; and |
| |
• | The oil sands in Alberta, Canada. |
Our operational division heads have an average of over 34 years of oilfield service experience and bring valuable basin-level expertise and long-term customer relationships to our business. We provide our completion and production and contract and directional drilling services to a diversified range of both public and private independent producers. Our top five
customers for the year ended December 31, 2016, representing 80%, of our revenue, were Gulfport Energy Corporation, or Gulfport, Japan Canada Oil Sands Limited, or Oil Sands Limited, Rice Energy, Inc. or Rice Energy, Surge Operating, LLC or Surge Operating, and Hilcorp Energy Corporation, or Hilcorp. For the year ended December 31, 2015, representing 71%, of our revenue, were Gulfport, EQT Production Company, Oil Sands Limited, RSP Permian LLC, or RSP Permian, and Bantrel Co.
Our Services
Each year, we evaluate qualitative and quantitative aspects of our service lines. As a result of that review as of December 31, 2016, we have split our completion and production division into pressure pumping services and well services. In addition, we renamed our remote accommodation services as other energy services. As a result, we now manage our business through five operating divisions: pressure pumping services, well services, natural sand proppant services, contract and directional drilling services and other energy services. For additional information see Note 17 to our consolidated financial statements included elsewhere in this annual report.
Pressure Pumping Services
Pressure Pumping. Our primary service offering is providing pressure pumping services, also known as hydraulic fracturing, to exploration and production companies. These services are intended to optimize hydrocarbon flow paths during the completion phase of horizontal shale wellbores. Currently, we provide pressure pumping services in the Utica Shale of Eastern Ohio. Two of our fleets, which are currently providing services in the Utica Shale, operate under a long-term contract expiring in September 2018. Our third fleet is also currently operating under a third party pricing agreement in the Utica Shale. Our pressure pumping services include the following:
| |
• | Hydraulic Fracturing. We provide high-pressure hydraulic fracturing services. Fracturing services are performed to enhance the production of oil and natural gas from formations having low permeability such that the flow of hydrocarbons is restricted. We have significant expertise in multistage fracturing of horizontal oil- and natural gas-producing wells in shale and other unconventional geological formations. |
The fracturing process consists of pumping a fracturing fluid into a well at sufficient pressure to fracture the formation. Materials known as proppants, in our case primarily sand or ceramic beads, are suspended in the fracturing fluid and are pumped into the fracture to prop it open. The fracturing fluid is designed to “break,” or loosen viscosity, and be forced out of the formation by its pressure, leaving the proppants suspended in the fractures created, thereby increasing the mobility of the hydrocarbons. As a result of the fracturing process, production rates are usually enhanced substantially, thus increasing the rate of return for the operator.
We own and operate fleets of mobile hydraulic fracturing units and other auxiliary heavy equipment to perform fracturing services. Our hydraulic fracturing units consist primarily of a high pressure hydraulic pump, a diesel engine, a transmission and various hoses, valves, tanks and other supporting equipment that are typically mounted to a flat-bed trailer. As of December 31, 2016, we had grown our pressure pumping business to three high pressure fleets consisting of an aggregate 64 high pressure fracturing units with pump nameplate capacity of 159,250 horsepower. As of December 31, 2016, we had also entered into agreements to acquire 30 new high pressure fracturing units with nameplate capacity of 75,000 horsepower and related equipment. Subsequently, in February 2017, we ordered an additional 23 new high pressure hydraulic pumps with nameplate capacity of 57,500 horsepower. Upon delivery of this new equipment, which is expected by mid-year 2017, we will have aggregate nameplate capacity of 291,750 horsepower.
We refer to the group of fracturing units, other equipment and vehicles necessary to perform a typical fracturing job as a “fleet” and the personnel assigned to each fleet as a “crew.” We operate on a 24-hour-per-day basis and we typically staff three crews per fleet. All of our fracturing units and high pressure pumps are manufactured to our specifications to enhance the performance and durability of our equipment and meet our customers’ needs.
Each hydraulic fracturing fleet includes a mobile, on-site control center that monitors pressures, rates and volumes, as applicable. From there, our field-level managers supervise the job-site by radio. Each control center is equipped with high bandwidth satellite hardware that provides continuous upload and download of job telemetry data. The data is delivered on a real-time basis to on-site job personnel, the operator and an assigned coordinator at our headquarters for display in both digital and graphical form.
An important element of fracturing services is determining the proper fracturing fluid, proppants and injection program to maximize results. In virtually all of our hydraulic fracturing jobs, our customers specify the composition of
the fracturing fluid to be used. The fracturing fluid may contain hazardous substances, such as hydrochloric acid and certain petrochemicals. Our customers are responsible for the disposal of the fracturing fluid that flows back out of the well as waste water. The customers remove the water from the well using a controlled flow-back process, and we are not involved in that process or in the disposal of the fluid.
Master Services Agreements. We contract with most of our pressure pumping customers under MSAs. Generally, under our MSAs, including those relating to our hydraulic fracturing services, we assume responsibility for, including control and removal of, pollution or contamination which originates above surface and originates from our equipment or services. However, our customer assumes responsibility for, including control and removal of, all other pollution or contamination which may occur during operations, including that which may result from seepage or any other uncontrolled flow of fluids. We may have liability in such cases if we are negligent or commit willful acts which cause such events. Generally, our customers also agree to indemnify us against claims arising from their employees’ personal injury or death to the extent that, in the case of our hydraulic fracturing operations, their employees are injured or their properties are damaged by such operations, unless resulting from our gross negligence or willful misconduct. Similarly, we generally agree to indemnify our customers for liabilities arising from personal injury to or death of any of our employees, unless resulting from gross negligence or willful misconduct of the customer. In addition, our customers generally agree to indemnify us for loss or destruction of customer-owned property or equipment and in turn, we agree to indemnify our customers for loss or destruction of property or equipment we own. Losses due to catastrophic events, such as blowouts, are generally the responsibility of the customer. However, despite this general allocation of risk, we might not succeed in enforcing such contractual allocation of risk, might incur an unforeseen liability falling outside the scope of such allocation or may be required to enter into an MSA with terms that vary from the above allocations of risk. As a result, we may incur substantial losses which could materially and adversely affect our financial condition and results of operation.
Well Services
Flowback. Our flowback services consist of production testing, solids control, hydrostatic testing and torque services. Flowback involves the process of allowing fluids to flow from the well following a treatment, either in preparation for an impending phase of treatment or to return the well to production. Our flowback equipment consists of manifolds, accumulators, valves, flare stacks and other associated equipment that combine to form up to a total of five well-testing spreads. We provide flowback services in the Appalachian Basin, the Eagle Ford Shale, the Haynesville Shale and mid-continent markets.
| |
• | Production Testing. Production testing focuses on testing production potential. Key measurements are recorded to determine activity both above and below ground. Production testing and the knowledge it provides help our customers determine where they can more efficiently deploy capital. As of December 31, 2016, we had five production testing packages. |
| |
• | Solids Control. Solids control services provide prepared drilling fluids for drilling rigs with equipment such as sand separators and plug catchers. These services reduce costs throughout the entire drilling process. As of December 31, 2016, we had ten solids control packages. |
| |
• | Hydrostatic Testing. Hydrostatic testing is a procedure in which pressure vessels, such as pipelines, are tested for damage or leaks. This method of testing helps maintain safety standards and increases the durability of the pipeline. We employ hydrostatic testing at industry standards and to a customer’s desired specifications and configuration. As of December 31, 2016, we had two hydrostatic testing packages. |
| |
• | Torque Services. Torque refers to the force applied to a rotary device to make it rotate. We offer a comprehensive range of torque services, offering a customer the dual benefit of reducing costs on the rig as well as reducing hazards for both personnel and equipment. We had five torque service packages as of December 31, 2016. |
Coil Tubing. Coiled tubing services involve injecting coiled tubing into wells to perform various well-servicing and workover operations. Coiled tubing is a flexible steel pipe with a diameter of typically less than three inches and manufactured in continuous lengths of thousands of feet. It is wound or coiled on a truck-mounted reel for onshore applications. Due to its small diameter, coiled tubing can be inserted into existing production tubing and used to perform a variety of services to enhance the flow of oil or natural gas without using a larger, more costly workover rig. The principal advantages of using coiled tubing in a workover include the ability to (i) continue production from the well without interruption, thus reducing the risk of formation damage, (ii) move continuous coiled tubing in and out of a well significantly faster than conventional pipe in the case of a workover rig, which must be jointed and unjointed, (iii) direct fluids into a wellbore with more precision, allowing for improved stimulation fluid placement, (iv) provide a source of energy to power a downhole mud motor or manipulate down-hole tools and (v) enhance access to remote fields due to the smaller size and mobility of a coiled tubing unit.
| |
• | As of December 31, 2016, we had three coiled tubing units capable of running over 22,000 feet of two inch coil rated at 15,000 pounds per square inch, or psi, and three coiled tubing units capable of running over |
20,000 feet of two and three eighths inch coil rated at 15 pounds per square inch, or psi, in service. We believe these units are well suited for the performance requirements of the unconventional resource markets we serve. The average age of these units was less than four years at December 31, 2016.
Pressure Control. Our pressure control services consist of nitrogen and fluid pumping services. Our pressure control services equipment is designed to support activities in unconventional resource plays with the ability to operate under high pressures without having to delay or cease production during completion operations. Ceasing or suppressing production during the completion phase of an unconventional well could result in formation damage impacting the overall recovery of reserves. Our pressure control services help operators minimize the risk of such damage during completion activities. Currently, we provide pressure control services in the Eagle Ford Shale in South Texas and the Permian Basin in West Texas. Our pressure control services include the following:
| |
• | Nitrogen Services. Nitrogen services involve the use of nitrogen, an inert gas, in various pressure pumping operations. When provided as a stand-alone service, nitrogen is used in displacing fluids in various oilfield applications. As of December 31, 2016, we had a total of four nitrogen pumping units capable of pumping at a rate of up to 3,000 standard cubic feet per minute with pressures up to 10,000 psi. Pumping at these rates and pressures is typically required for the unconventional oil and natural gas resource plays we serve. The average age of these units was less than four years at December 31, 2016. |
| |
• | Fluid Pumping Services. Fluid pumping services consist of maintaining well pressure, pumping down wireline tools, assisting coiled tubing units and the removal of fluids and solids from the wellbore for clean-out operations. As of December 31, 2016, we had five fluid pumping units with an average age of less than four years. Of these, all five were coiled tubing double pump units capable of output of up to eight barrels per minute, and are rated to a maximum of 15,000 psi service. |
Equipment Rentals. Our equipment rental services provide a wide range of oilfield related equipment used in flowback and hydraulic fracturing services. Our equipment rentals consist of light plants and other oilfield related equipment. We provide equipment rental services in the Eagle Ford Shale and mid-continent markets.
Master Services Agreements. We contract with most of our well service customers under MSAs. For more information regarding our MSAs, see "- Pressure Pumping Services - Master Service Agreements" above.
Natural Sand Proppant Services
In our natural sand proppant business, we currently buy processed sand from suppliers on the spot market and resell that sand. Natural sand proppant, also known as frac sand, is the most widely used type of proppant due to its broad applicability in unconventional oil and natural gas wells and its cost advantage relative to other proppants. Natural frac sand may be used as proppant in all but the highest pressure and temperature drilling environments and is being employed in nearly all major U.S. unconventional oil and natural gas producing basins, including those in which we operate.
We also have the ability to purchase raw sand under a fixed-price contract with one supplier, process it into premium monocrystalline sand (also known as frac sand), a specialized mineral that is used as a proppant at our indoor sand processing plant located in Pierce County, Wisconsin and sell it to our customers for use in their hydraulic fracturing operations to enhance recovery rates from unconventional wells. Our sand processing plant is capable of producing a range of frac sand sizes for use in all major North American shale basins, including a majority of the standard proppant sizes as defined by the ISO/API 13503-2 specifications. These grain sizes can be customized to meet the demands of our customers with respect to a specific well. Our supply of Jordan substrate exhibits the physical properties necessary to withstand the completion and production environments of the wells in these shale basins. Our indoor processing plant is designed for year-round continuous wet and dry plant operation capable of producing a wide variety of frac sand products based on the needs of our customers. At December 31, 2016 we were not using this plant to produce sand as a result of the decline in commodity pricing and the resulting decrease in completion activity. However, based on recent increases in demand for sand and rising prices, we recently returned this plant to operation and the first shipments from this plant began in February 2017. We expect this plant to reach full utilization of approximately 58,300 tons per month by April 2017.
We also provide logistics solutions to facilitate delivery of our frac sand products to our customers. Almost all of our frac sand products are shipped by rail to our customers in the Utica Shale and the Montney Shale in British Columbia and Alberta, Canada. Our logistics capabilities in this regard are important to our customers, who focus on both the reliability and flexibility of product delivery. Because our customers generally find it impractical to store frac sand in large quantities near their job sites, they typically prefer product to be delivered where and as needed, which requires predictable and efficient loading and shipping capabilities. We contract with third party providers to transport our frac sand products to railroad facilities
for delivery to our customers. We currently lease or have access to origin transloading facilities on the Canadian National Railway Company (CN), Union Pacific (UP), Burlington Northern Santa Fe (BNSF) and the Canadian Pacific (CP) rail systems and use an in-house railcar fleet that we lease from various third parties to deliver our frac sand products to our customers. Origin transloading facilities on multiple railways allow us to provide predictable and efficient loading and shipping of our frac sand products. We also utilize a destination transloading facility in Yorkville, Ohio, to serve the Utica Shale, and utilize destination transloading facilities located in other North American resource plays, including the Montney Shale, to meet our customers’ delivery needs.
Contract Land and Directional Drilling Services
Our contract and directional drilling business provides contract drilling and directional drilling services.
Contract Drilling. As part of our contract drilling services, we provide both vertical and horizontal drilling services to our customers. Currently, we perform our contract drilling services in the Permian Basin of West Texas.
A majority of the wells we drill for our customers are drilled in unconventional basins or resource plays. These plays are generally characterized by complex geologic formations that often require higher horsepower, premium rigs and experienced crews to reach targeted depths. As of December 31, 2016, we owned 13 land drilling rigs, ranging from 800 to 1,500 horsepower, nine of which are specifically designed for drilling horizontal and directional wells, which continue to increase as a percentage of total wells drilled in North America and are frequently utilized in unconventional resource plays. As of December 31, 2016, five of our 13 drilling rigs were operating under term contracts with a term of more than one well or a stated period of time. To facilitate the provision of our contract drilling services, as of December 31, 2016, we also owned 32 trucks specifically tailored to move rigs and two cranes to assist us in moving rigs in the Permian Basin.
A land drilling rig generally consists of engines, a hoisting system, a rotating system, a drawworks, a mast, pumps and related equipment to circulate the drilling fluid under various pressures, blowout preventers, drill string and related equipment. The engines power the different pieces of equipment, including a rotary table or top drive that turns the drill pipe, or drill string, causing the drill bit to bore through the subsurface rock layers. Drilling rigs use long strings of drill pipe and drill collars to drill wells. Drilling rigs are also used to set heavy strings of large-diameter pipe, or casing, inside the borehole. Because the total weight of the drill string and the casing can exceed 500,000 pounds, drilling rigs require significant hoisting and braking capacities. Generally, a drilling rig’s hoisting system is made up of a mast, or derrick, a drilling line, a traveling block and hook assembly and ancillary equipment that attaches to the rotating system, a mechanism known as the drawworks. The drawworks mechanism consists of a revolving drum, around which the drilling line is wound, and a series of shafts, clutches and chain and gear drives for generating speed changes and reverse motion. The drawworks also houses the main brake, which has the capacity to stop and sustain the weights used in the drilling process. When heavy loads are being lowered, a hydromatic or electric auxiliary brake assists the main brake to absorb the great amount of energy developed by the mass of the traveling block, hook assembly, drill pipe, drill collars and drill bit or casing being lowered into the well.
The rotating equipment from top to bottom consists of a swivel, the kelly bushing, the kelly, the rotary table, drill pipe, drill collars and the drill bit. We refer to the equipment between the swivel and the drill bit as the drill stem. The swivel assembly sustains the weight of the drill stem, permits its rotation and affords a rotating pressure seal and passageway for circulating drilling fluid into the top of the drill string. The swivel also has a large handle that fits inside the hook assembly at the bottom of the traveling block. Drilling fluid enters the drill stem through a hose, called the rotary hose, attached to the side of the swivel. The kelly is a triangular, square or hexagonal piece of pipe, usually 40 feet long, that transmits torque from the rotary table to the drill stem and permits its vertical movement as it is lowered into the hole. The bottom end of the kelly fits inside a corresponding triangular, square or hexagonal opening in a device called the kelly bushing. The kelly bushing, in turn, fits into a part of the rotary table called the master bushing. As the master bushing rotates, the kelly bushing also rotates, turning the kelly, which rotates the drill pipe and thus the drill bit. Drilling fluid is pumped through the kelly on its way to the bottom. The rotary table, equipped with its master bushing and kelly bushing, supplies the necessary torque to turn the drill stem. The drill pipe and drill collars are both steel tubes through which drilling fluid can be pumped. Drill pipe comes in 30-foot sections, or joints, with threaded sections on each end. Drill collars are heavier than drill pipe and are also threaded on the ends. Collars are used on the bottom of the drill stem to apply weight to the drill bit. At the end of the drill stem is the bit, which chews up the formation rock and dislodges it so that drilling fluid can circulate the fragmented material back up to the surface where the circulating system filters it out of the fluid.
Drilling fluid, often called drilling mud, is a mixture of clays, chemicals and water or oil, which is carefully formulated for the particular well being drilled. Bulk storage of drilling fluid materials, the pumps and the mud-mixing equipment are placed at the start of the circulating system. Working mud pits and reserve storage are at the other end of the system. Between these two points the circulating system includes auxiliary equipment for drilling fluid maintenance and
equipment for well pressure control. Within the system, the drilling mud is typically routed from the mud pits to the mud pump and from the mud pump through a standpipe and the rotary hose to the drill stem. The drilling mud travels down the drill stem to the bit, up the annular space between the drill stem and the borehole and through the blowout preventer stack to the return flow line. It then travels to a shale shaker for removal of rock cuttings, and then back to the mud pits, which are usually steel tanks. The reserve pits, usually one or two fairly shallow excavations, are used for waste material and excess water around the location.
There are numerous factors that differentiate drilling rigs, including their power generation systems, horsepower, maximum drilling depth and horizontal drilling capabilities. The actual drilling depth capability of a rig may be less than or more than its rated depth capability due to numerous factors, including the size, weight and amount of the drill pipe on the rig. The intended well depth and the drill site conditions determine the amount of drill pipe and other equipment needed to drill a well.
Our drilling rigs have rated maximum depth capabilities ranging from 12,500 feet to 20,000 feet. Of these drilling rigs, seven are electric rigs and six are mechanical rigs. An electric rig differs from a mechanical rig in that the electric rig converts the power from its generators (which in the case of mechanical rigs, power the rig directly) into electricity to power the rig. Depth and complexity of the well and drill site conditions are the principal factors in determining the specifications of the rig selected for a particular job. Power requirements for drilling jobs may vary considerably, but most of our mechanical drilling rigs employ six engines to generate between 800 and 1,500 horsepower, depending on well depth and rig design. Most drilling rigs capable of drilling in deep formations drill to measured depths greater than 10,000 to 18,000 feet. Generally, land rigs operate with four crews of five people and two tool pushers, or rig managers, rotating on a weekly or bi-weekly schedule.
We believe that our drilling rigs and other related equipment are in good operating condition. Our employees perform periodic maintenance and minor repair work on our drilling rigs.
We obtain our contracts for drilling oil and natural gas wells either through competitive bidding or through direct negotiations with customers. We typically enter into drilling contracts that provide for compensation on a daywork basis. Occasionally, we enter into drilling contracts that provide for compensation on a footage basis, however, a majority of such footage drilling contracts also provide for daywork rates for work outside core drilling activities contemplated by such footage contracts and under certain other circumstances. We have not historically entered into turnkey contracts; however, we may decide to enter into such contracts in the future. It is also possible that we may acquire such contracts in connection with future acquisitions of drilling assets. Contract terms we offer generally depend on the complexity and risk of operations, the on-site drilling conditions, the type of equipment used, the anticipated duration of the work to be performed and market conditions. As of December 31, 2016, three of our 13 drilling rigs were operating under term contracts that provide for a take-or-pay model where customers cannot terminate contracts without paying the full amount remaining and two were operating under contracts that allow the customer to terminate on 30 days’ notice, upon payment of an agreed upon fee.
Daywork Contracts. Under daywork drilling contracts, we provide equipment and labor and perform services under the direction, supervision and control of our customers. We are paid a specified operating daywork rate from the time the drilling unit is rigged up at the drilling location and is ready to commence operations. Additionally, the daywork drilling contracts typically provide for fees and/or a daywork rates for mobilization, demobilization, moving, standby time and for any continuous period that normal operations are suspended or cannot be carried on because of force majeure conditions. The daywork drilling contracts also generally provide that the customer has the right to designate the points at which casing will be set and the manner of setting, cementing and testing. Such specifications include hole size, casing size, weight, grade and approximate setting depth. Furthermore, the daywork drilling contracts specify the equipment, materials and services to be separately furnished by us and our customer. Under these contracts, liability is typically allocated so that our customer is solely responsible for the following: (i) damage to our surface equipment as a result of certain corrosive elements; (ii) damage to customer’s equipment; (iii) damage to our in-hole equipment; (iv) damage or loss to the hole; (v) damage to the underground; and (vi) costs and damages associated with a wild well. We remain responsible for any damage to our surface equipment (except for damage resulting from the presence of certain corrosive elements) and for pollution or contamination from spills of materials that originate above the surface, are wholly in our control and are directly associated with our equipment. Daywork drilling contracts generally allow the customer to terminate the contract prior to drilling to a specified depth. This right, however, is generally subject to early termination compensation, the amount of which depends on when the termination occurs.
Footage Contracts. Under footage contracts, the contractor is typically paid a fixed amount for each foot drilled, regardless of the time required or the problems encountered in drilling the well. A majority of these types of drilling contracts, however, contain both footage and daywork basis provisions, the applicability of which typically depends on the depth of drilling and/or the type of services being performed. For instance, when drilling occurs below a specified drilling depth or when work is considered outside the scope of the footage basis, which we refer to as core drilling, then daywork contract terms apply
similar to those described above. Otherwise, the footage contract terms apply. These include a footage rate price that is a specific dollar amount per linear foot of hole drilled within the contract footage depth. Also, under the footage contract terms, we assume more responsibility for base drilling activities compared to daywork drilling. For instance, in addition to assuming responsibility for damage to our surface equipment and damage caused by certain pollution and contamination, we are responsible for the following: (i) damage to our in-hole equipment; (ii) damage to the hole that is attributable to our performance; and (iii) any costs or expenditures associated with drilling a new hole after such damage. Our customers remain responsible for any loss to their equipment, for any damage to a hole caused by them and for any underground damage. As with contracts for daywork drilling, footage drilling contracts generally allow the customer to terminate the contract before drilling to a specified depth. This right, however, is generally subject to early termination compensation, the amount of which depends on when the termination occurs.
Because we assume higher risk in a footage drilling contract, we typically pay more of the out-of-pocket costs associated with such contracts as compared to daywork contracts. We endeavor to manage these additional risks through the use of our engineering expertise and bid the footage contracts accordingly. We typically maintain insurance coverage against some, but not all, drilling hazards. However, the occurrence of uninsured or under-insured losses or operating cost overruns on our footage jobs could have a negative impact on our profitability. While we have historically entered into few footage contracts, we may enter into more such arrangements in the future to the extent warranted by market conditions.
Turnkey Contracts. Turnkey contracts typically provide for a drilling company to drill a well for a customer to a specified depth and under specified conditions for a fixed price, regardless of the time required or the problems encountered in drilling the well. The drilling company would provide technical expertise and engineering services, as well as most of the equipment and drilling supplies required to drill the well. The drilling company may subcontract for related services, such as the provision of casing crews, cementing and well logging. Under typical turnkey drilling arrangements, a drilling company would not receive progress payments and would be paid by its customer only after it had performed the terms of the drilling contract in full. The risks to the drilling company under a turnkey contract are substantially greater than those under a daywork basis. This is primarily because under a turnkey contract, the drilling company assumes most of the risks associated with drilling operations generally assumed by the operator in a daywork contract, including the risk of blowout, loss of hole, stuck drill pipe, machinery breakdowns, abnormal drilling conditions and risks associated with subcontractors’ services, supplies, cost escalations and personnel.
Directional Drilling. Our directional drilling services provide for the efficient drilling and production of oil and natural gas from unconventional resource plays. Our directional drilling equipment includes mud motors used to propel drill bits and kits for MWD and EM technology. MWD kits are down-hole tools that provide real-time measurements of the location and orientation of the bottom-hole assembly, which is necessary to adjust the drilling process and guide the wellbore to a specific target. This technology, coupled with our complementary services, allows our customers to drill wellbores to specific objectives within narrow location parameters within target horizons. The evolution of unconventional resource reserve recovery has increased the need for the precise placement of a wellbore. Wellbores often travel across long-lateral intervals within narrow formations as thin as ten feet. Our personnel are involved in all aspects of a well from the initial planning of a customer’s drilling program to the management and execution of the horizontal or directional drilling operation.
As of December 31, 2016, we owned seven MWD kits and two EM kits used in vertical, horizontal and directional drilling applications, 57 mud motors, ten air motors and an inventory of related parts and equipment. Currently, we perform our directional drilling services in the Utica Shale, Anadarko Basin, Arkoma Basin and Permian Basin.
Other Energy Services
Our other energy services division currently consists of our remote accommodations business which provides housing, kitchen and dining, and recreational service facilities for oilfield workers located in remote areas away from readily available lodging. We provide a turnkey solution for our customers’ accommodation needs. These modular camps, when assembled together, form large dormitories, with kitchen/dining facilities and recreation areas. These camps are operated as “all inclusive,” where meals are prepared and provided for the guests. The primary revenue source for these camps is lodging fees. In 2013, we expanded our remote accommodation services business after being awarded a long-term contract by an unrelated third party. We also have an agreement with an affiliate pursuant to which we provide remote accommodation services on an on-going basis. See Note 15 to our consolidated financial statements included elsewhere in this annual report. As of December 31, 2016, we had a capacity of 1,008 rooms, 880 of which are at Sand Tiger Lodge, our camp in northern Alberta, Canada, and 128 of which are available to be leased as rental equipment to a third party.
Our Industry
The oil and natural gas industry has traditionally been volatile and is influenced by a combination of long-term, short-term and cyclical trends, including the domestic and international supply and demand for oil and natural gas, current and expected future prices for oil and natural gas and the perceived stability and sustainability of those prices, production depletion rates and the resultant levels of cash flows generated and allocated by exploration and production companies to their drilling, completion and related services and products budget. The oil and natural gas industry is also impacted by general domestic and international economic conditions, political instability in oil producing countries, government regulations (both in the United States and elsewhere), levels of customer demand, the availability of pipeline capacity and other conditions and factors that are beyond our control.
Demand for most of our products and services depends substantially on the level of expenditures by companies in the oil and natural gas industry. The significant decline in oil and natural gas prices that began in the third quarter of 2014 continued into February 2016, when the closing price of oil reached a 12-year low of $26.19 per barrel on February 11, 2016. The low commodity price environment caused a reduction in the drilling, completion and other production activities of most of our customers and their spending on our products and services.
The reduction in demand, and the resulting oversupply of many of the services and products we provide, has substantially reduced the prices we can charge our customers for our products and services, and has had a negative impact on the utilization of our services. While oil prices have rebounded from the lows experienced during the first part of 2016, and the demand for our suite of services has increased, prices for oil and natural gas historically have been extremely volatile and are expected to continue to be volatile in the years to come. Throughout 2016, the posted price for West Texas Intermediate light sweet crude oil, which we refer to as WTI, ranged from a low of $26.19 per barrel, or Bbl, on February 11, 2016 to a high of $54.06 per Bbl on December 28, 2016. As commodity prices have begun to recover, we have experienced an increase in activity. If near term commodity prices stabilize at current levels and recover further, we expect to experience further increase in demand for our services and products, particularly in our completion and production, natural sand proppant and contract land and directional drilling businesses. Spears and Associates, Inc. estimates a recovery to 1,089 active drilling rigs in the United States by 2020, with a projected 27,000 new wells being drilled by 2020. We expect that the projected increased drilling activity will result in increased demand for our completion and production services.
Although the ongoing volatility and depressed levels of activity are expected to persist until supply and demand for oil and natural gas come into balance, we believe that the following trends in our industry should benefit our operations and our ability to achieve our primary business objective as commodity prices recover:
| |
• | Increased U.S. Petroleum field Production. According to the EIA, U.S. average petroleum field production was approximately 8.9 million barrels per day during November 2016, only 7.5% below the record high average daily petroleum field production set in 2015. U.S. average petroleum field production has grown at a compound annual growth rate of 9.8% over the period from 2009 through 2015 due to production gains from unconventional reservoirs. We expect that this continued growth will result in increased demand for our services as commodity prices continue to stabilize and increase. |
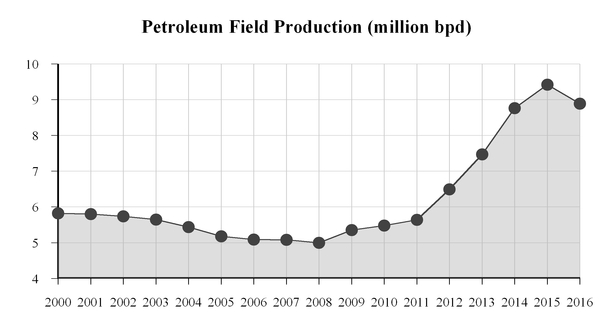
| |
• | Increased use of horizontal drilling to develop unconventional resource plays. According to Baker Hughes, the horizontal rig count on December 30, 2016 was 532, or approximately 81% of the total U.S. onshore rig count. Although the overall onshore rig count declined significantly from September 2014 to May 2016, the horizontal rig count as a percentage of the overall onshore rig count has increased every year since 2007 when horizontal rigs represented only approximately 25% of the total U.S. onshore rig count at year-end. As a result of improvements in drilling and production enhancement technologies, oil and natural gas companies are increasingly developing unconventional resources such as tight sands and shales. Successful and economic production of these unconventional resource plays frequently requires horizontal drilling, fracturing and stimulation services. Drilling related activity for unconventional resources is typically done on tighter acre spacing and thus requires that more wells be drilled relative to conventional resources. We believe that all of these characteristics will drive the demand for our services in an improved commodity price environment. |
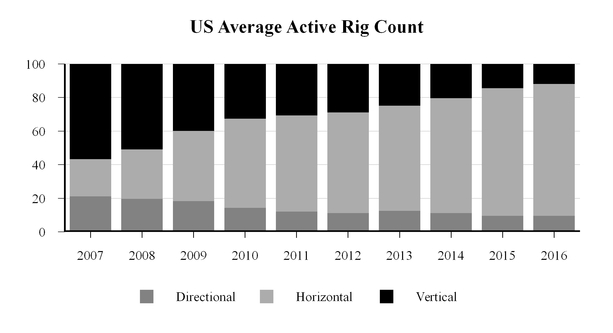
| |
• | Tight oil production growth is expected to continue to be the primary driver of U.S. oil production growth. According to the EIA, U.S. tight oil production grew from 430,000 barrels per day in 2007 to almost 4.3 million barrels per day in 2016, representing 48% of total U.S. crude oil production in 2016. A majority of this increase came from the Eagle |
Ford play in South Texas, the Bakken Shale in the Williston Basin of North Dakota and Montana, and the Permian Basin in West Texas. We believe the Utica Shale and the Permian Basin, our primary business locations, will be key drivers of U.S. tight oil and natural gas production as those plays are developed further in the coming years due to the favorable well economics in those basins.
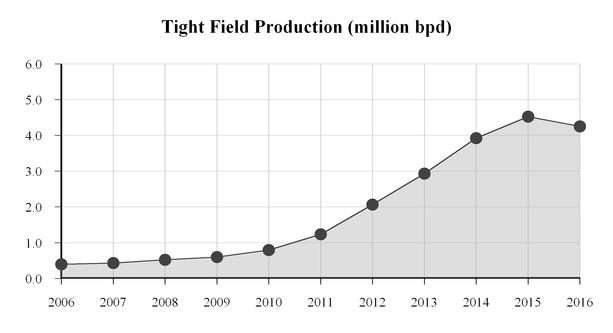
| |
• | Horizontal wells are heavily dependent on oil field services. According to Baker Hughes, as of December 30, 2016, horizontal rigs accounted for approximately 81% of all rigs drilling in the United States, up from 25% at year-end 2007. The scope of services for a horizontal well are greater than for a conventional well. Industry analysts report that the average horsepower, length of the lateral and number of fracture stages has continued to increase since 2008. We believe our commitment to provide services in unconventional plays, such as the Utica Shale and the Permian Basin, provide us the opportunity to compete in those regional markets where the majority of total footage is drilled each year in the United States. |
| |
• | New and emerging unconventional resource plays. In addition to the development of existing unconventional resource plays such as the Permian, Utica, Bakken, Eagle Ford, Barnett, Fayetteville, Cotton Valley, Haynesville, Marcellus and Woodford Shales, exploration and production companies continue to find new unconventional resources. These include oil and liquids-based shales in the Cana Woodford, Granite Wash, Niobrara, Woodford and SCOOP/STACK resource plays. In certain cases, exploration and production companies have acquired vast acreage positions in these plays that require them to drill and produce hydrocarbons to hold the leased acreage. We believe these unconventional resource plays will increasingly drive demand for our services as commodity prices continue to recover as they typically require the use of extended reach horizontal drilling, multiple stage fracture stimulation and high pressure completion capabilities. We also believe we are well positioned to expand our services in two major unconventional plays, the Utica Shale in Ohio and the Permian Basin in West Texas. |
| |
• | Need for additional drilling activity to maintain production levels. With the increased maturity of the onshore conventional and, in many cases, unconventional resource plays, oil and natural gas production may be characterized as having steeper initial decline curves. Given average decline rates and the substantial reduction in activity over the past year, we believe that the number of wells drilled is likely to increase in coming years as commodity prices continue to recover. Once a well has been drilled, it requires recurring production and completion services, which we believe will also drive demand for our services. |
Our Strengths
Our primary business objective is to grow our operations and create value for our stockholders through organic growth opportunities and accretive acquisitions. We believe that the following strengths position us well to capitalize on activity in unconventional resource plays and achieve our primary business objective:
| |
• | Modern fleet of equipment designed for horizontal wells. Our service fleet is predominantly comprised of equipment designed to optimize recovery from unconventional wells. As of December 31, 2016, approximately 44% of our high pressure fracturing units had been purpose built within the last three years. Giving effect to the delivery of the new equipment ordered in November 2016 and February 2017 as described above in "- Pressure Pumping Services - Hydraulic Fracturing," approximately 69% of our high pressure fracturing units will have been built within the last three years. Our pressure control equipment has been designed by us and has an average age of approximately three years. Our accommodation units have an average age of approximately five years and are built on a customer-by-customer basis to meet their specific needs. We believe that our modern fleet of quality equipment will allow us to provide a high level of service to our customers and capitalize on future growth in the unconventional resource plays that we serve. |
| |
• | Strategic geographic positioning, including primary presence in the Utica Shale and the Permian Basin. We currently operate facilities and service centers to support our operations in major unconventional resource plays in the United States, including the Utica Shale in Eastern Ohio, the Permian Basin in West Texas, the Marcellus Shale in West Virginia, the Granite Wash in Oklahoma and Texas, the Cana Woodford Shale and the Cleveland Sand in Oklahoma, the Eagle Ford Shale in South Texas and the oil sands in Alberta, Canada. We believe our geographic positioning within active oil and natural gas liquids resource plays will benefit us strategically as activity increases in these unconventional resource plays. |
| |
• | Long-term contractual and other basin-level relationships with a stable customer base. We are party to two long-term contracts with Gulfport to provide pressure pumping services and natural sand proppant services through September 2018. In addition, our operational division heads and field managers have formed long-term relationships with our customer base. We believe these contractual and other relationships help provide us a more stable and growth-oriented client base in the unconventional shale markets that we currently serve. Our customers include large independent oil and natural gas exploration and production companies. Our top five customers for the year ended December 31, 2016, representing 80%, of our revenue, were Gulfport, Oil Sands Limited, Rice Energy, Surge Operating and Hilcorp. For the year ended December 31, 2015, representing 71%, of our revenue, were Gulfport, EQT Production Company, Oil Sands Limited, RSP Permian and Bantrel Co. |
| |
• | Experienced management and operating team. Our operational division heads have an extensive track record in the oilfield services business with an average of over 34 years of oilfield services experience. In addition, our field managers have expertise in the geological basins in which they operate and understand the regional challenges that our customers face. We believe their knowledge of our industry and business lines enhances our ability to provide innovative, client-focused and basin-specific customer service, which we also believe strengthens our relationships with our customers. |
Our Business Strategy
We intend to achieve our primary business objective by the successful execution of our business plan to strategically deploy our equipment and personnel to provide pressure pumping services, well services, natural sand proppant, drilling and other energy services in unconventional resource plays, including the Utica Shale in Ohio and the Permian Basin in West Texas. We believe these services optimize our customers’ ultimate resources recovery and present value of hydrocarbon reserves. We seek to create cost efficiencies for our customers by providing a suite of complementary oilfield services designed to address a wide range of our customers’ needs. Specifically, we intend to create value for our stockholders through the following strategies:
| |
• | Capitalize on the recovery in activity in the unconventional resource plays. Our equipment is designed to provide a broad range of services for unconventional wells, and our operations are strategically located in major unconventional resource plays. During 2016, the posted price for WTI, rose from a low of $26.19 per barrel on February 11, 2016 to a high of $54.06 per barrel on December 28, 2016 before closing the year at $53.72 per barrel. If commodity prices stabilize at current levels or recover further, we expect to experience further increase in demand for our services and products. We intend to capitalize on the anticipated increase in activity in these markets and diversify our operations across additional unconventional resource basins. Our core operations are currently focused in the Utica Shale in Ohio and the Permian Basin in West Texas. We intend to continue to strategically deploy assets to these and other unconventional resource basins and will look to capitalize on further growth in emerging unconventional resource plays as they develop. |
| |
• | Leverage our broad range of services for unconventional wells for cross-selling opportunities. We offer a complementary suite of oilfield services and products. Our pressure pumping and well services divisions provide pressure pumping services, pressure control services and flowback services for unconventional wells. Our natural sand |
proppant services division sells and is capable of producing proppant for hydraulic fracturing. Our drilling services division adds drilling capabilities to our well-related services. We intend to leverage our existing customer relationships and operational track record to cross sell our services and increase our exposure and product offerings to our existing customers, broaden our customer base and expand opportunistically to other geographic regions in which our customers have operations, as well as to create operational efficiencies for our customers.
| |
• | Expand through selected, accretive acquisitions. To complement our organic growth, we intend to actively pursue selected, accretive acquisitions of businesses and assets, primarily related to our completion and production services and natural sand proppant services, that can meet our targeted returns on invested capital and enhance our portfolio of products and services, market positioning and/or geographic presence. We believe this strategy will facilitate the continued expansion of our customer base, geographic presence and service offerings. We also believe that our industry contacts and those of Wexford, our equity sponsor and largest stockholder, will facilitate the identification of acquisition opportunities. We expect to use our common stock as consideration for accretive acquisitions. |
| |
• | Maintain a conservative balance sheet. We seek to maintain a conservative balance sheet, which allows us to better react to changes in commodity prices and related demand for our services, as well as overall market conditions. We used a portion of the net proceeds from the IPO to repay all outstanding borrowings under our revolving credit facility and as of December 31, 2016 had no outstanding debt and a cash balance of $28.7 million. |
| |
• | Expand our services to meet expanding customer demand. The scope of services for horizontal wells is greater than that for conventional wells. Industry analysts have reported that the average horsepower required for current completion designs, amount of sand per lateral foot, length of lateral and number of fracture stages has continued to increase since 2008. We consistently monitor market conditions and intend to expand the capacity and scope of our business lines as demand warrants in resource plays in which we currently operate, as well as in new resource plays. If we perceive unmet demand in our principal geographic locations for different service lines, we will seek to expand our current service offerings to meet that demand. |
| |
• | Leverage our experienced operational management team and basin-level expertise. We seek to manage the services we provide as closely as possible to the needs of our customer base. Our operational division heads have long-term relationships with our largest customers. We intend to leverage these relationships and our operational management team’s basin-level expertise to deliver innovative, client focused and basin-specific services to our customers. |
Marketing and Customers
Our customers consist primarily of independent oil and natural gas producers and land-based drilling contractors in North America. For the years ended December 31, 2016 and 2015, we had approximately 239 and 116 customers, respectively, including Gulfport, Oil Sands Limited, RSP Permian and Rice Energy. Our top five customers accounted for approximately 80% and 71% of our revenue for the years ended December 31, 2016 and 2015, respectively. During the year ended December 31, 2016, Gulfport accounted for 57% and Oil Sands Limited accounted for 11% of our revenue. For the year ended December 31, 2015, Gulfport accounted for 47% and EQT Production Company accounted for 12% of our revenue. Although we believe we have a broad customer base and wide geographic coverage of operations, it is likely that we will continue to derive a significant portion of our revenue from a relatively small number of customers in the future. If a major customer decided not to continue to use our services, revenue could decline and our operating results and financial condition could be harmed.
Operating Risks and Insurance
Our operations are subject to hazards inherent in the oilfield services industry, such as accidents, blowouts, explosions, fires and spills and releases that can cause:
| |
• | personal injury or loss of life; |
| |
• | damage or destruction of property, equipment, natural resources and the environment; and |
| |
• | suspension of operations. |
In addition, claims for loss of oil and natural gas production and damage to formations can occur in the oilfield services industry. If a serious accident were to occur at a location where our equipment and services are being used, it could result in us being named as a defendant in lawsuits asserting large claims.
Because our business involves the transportation of heavy equipment and materials, we may also experience traffic accidents which may result in spills, property damage and personal injury.
Despite our efforts to maintain safety standards, we from time to time have suffered accidents in the past and anticipate that we could experience accidents in the future. In addition to the property damage, personal injury and other losses from these accidents, the frequency and severity of these incidents affect our operating costs and insurability and our relationships with customers, employees, regulatory agencies and other parties. Any significant increase in the frequency or severity of these incidents, or the general level of compensation awards, could adversely affect the cost of, or our ability to obtain, workers’ compensation and other forms of insurance, and could have other material adverse effects on our financial condition and results of operations.
We maintain commercial general liability, workers’ compensation, business auto, commercial property, motor truck cargo, umbrella liability, in certain instances, excess liability, and directors and officers insurance policies providing coverages of risks and amounts that we believe to be customary in our industry. Further, we have pollution legal liability coverage for our business entities, which would cover, among other things, third party liability and costs of clean-up relating to environmental contamination on our premises while our equipment and chemicals are in transit and while on our customers’ job site. With respect to our hydraulic fracturing operations, coverage would be available under our pollution legal liability policy for any surface or subsurface environmental clean-up and liability to third parties arising from any surface or subsurface
contamination. We also have certain specific coverages for some of our businesses, including our remote accommodation services, pressure pumping services and contract and directional drilling services.
Although we maintain insurance coverage of types and amounts that we believe to be customary in the industry, we are not fully insured against all risks, either because insurance is not available or because of the high premium costs relative to perceived risk. Further, insurance rates have in the past been subject to wide fluctuation and changes in coverage could result in less coverage, increases in cost or higher deductibles and retentions. Liabilities for which we are not insured, or which exceed the policy limits of our applicable insurance, could have a material adverse effect on us. See Item 1A. “Risk Factors” on page 20 of this annual report for a description of certain risks associated with our insurance policies.
Safety and Remediation Program
In the oilfield services industry, an important competitive factor in establishing and maintaining long-term customer relationships is having an experienced and skilled workforce. Recently, many of our large customers have placed an emphasis not only on pricing, but also on safety records and quality management systems of contractors. We believe these factors will gain further importance in the future. We have committed resources toward employee safety and quality management training programs. Our field employees are required to complete both technical and safety training programs. Further, as part of our safety program and remediation procedures, we check fluid lines for any defects on a periodic basis to avoid line failure during hydraulic fracturing operations, marking such fluid lines to reflect the most recent testing date. We also regularly monitor pressure levels in the fluid lines used for fracturing and the surface casing to verify that the pressure and flow rates are consistent with the job specific model in an effort to avoid failure. As part of our safety procedures, we also have the capability to shut down our pressure pumping and fracturing operations both at the lines and in our data van. In addition, we maintain spill kits on location for containment of pollutants that may be spilled in the process of providing our hydraulic fracturing services. The spill kits are generally comprised of pads and booms for absorption and containment of spills, as well as soda ash for neutralizing acid. Fire extinguishers are also in place on job sites at each pump.
Historically, we have used a third-party contractor to provide remediation and spill response services when necessary to address spills that were beyond our containment capabilities. None of these prior spills were significant, and we have not experienced any incidents, citations or legal proceeding relating to our hydraulic fracturing services for environmental concerns. To the extent our hydraulic fracturing or other oilfield services operations result in a future spill, leak or other environmental impact that is beyond our ability to contain, we intend to engage the services of such remediation company or an alternative company to assist us with clean-up and remediation.
Competition
The markets in which we operate are highly competitive. To be successful, a company must provide services and products that meet the specific needs of oil and natural gas exploration and production companies and drilling services contractors at competitive prices.
We provide our services and products across the United States and in Alberta, Canada and we compete against different companies in each service and product line we offer. Our competition includes many large and small oilfield service
companies, including the largest integrated oilfield services companies. Our major competitors in pressure pumping services include Halliburton Company, U.S. Well Services, LLC, Schlumberger Limited, Keane Group, Inc., C&J Energy Services Ltd., RPC Incorporated, Complete Energy Services, Inc. and FracTech Services, Inc. Our major competitors for our pressure control services include Schlumberger Limited, Halliburton Company, Baker Hughes Incorporated, Weatherford International Ltd., Key Energy Services Inc., Nabors Industries Ltd., Complete Energy Services, Inc. and RPC Incorporated and a significant number of locally oriented businesses. In our contract and directional drilling services segment, our primary competitors include Helmerich & Payne, Inc., Precision Drilling Corporation, Patterson-UTI Energy, Inc., Cactus Drilling, Sidewinder Drilling, Inc., Baker Hughes Incorporated, Weatherford International Ltd. and various regional and local service providers. Our major competitors in our proppant production and sales business are Badger Mining Corporation, Fairmount Minerals, Ltd., Hi-Crush Partners LP, Preferred Proppants LLC, Unimin Corporation, Smart Sand, Inc. and U.S. Silica Holdings Inc. Our major competitors for our remote accommodation business include Oil States International, Inc., Black Diamond Limited and a significant number of local businesses.
We believe that the principal competitive factors in the market areas that we serve are quality of service and products, reputation for safety and technical proficiency, availability and price. While we must be competitive in our pricing, we believe our customers select our services and products based on the local leadership and basin-expertise that our field management and operating personnel use to deliver quality services and products.
Regulation
We operate under the jurisdiction of a number of regulatory bodies that regulate worker safety standards, the handling of hazardous materials, the transportation of explosives, the protection of human health and the environment and driving standards of operation. Regulations concerning equipment certification create an ongoing need for regular maintenance which is incorporated into our daily operating procedures. The oil and natural gas industry is subject to environmental regulation pursuant to local, state and federal legislation.
Transportation Matters
In connection with our transportation and relocation of our oilfield service equipment and shipment of frac sand, we operate trucks and other heavy equipment. As such, we operate as a motor carrier in providing certain of our services and therefore are subject to regulation by the United States Department of Transportation and by various state agencies. These regulatory authorities exercise broad powers, governing activities such as the authorization to engage in motor carrier operations, driver licensing and insurance requirements, financial reporting and review of certain mergers, consolidations and acquisitions, and transportation of hazardous materials (HAZMAT). Our trucking operations are subject to possible regulatory and legislative changes that may increase our costs. Some of these possible changes include increasingly stringent environmental regulations, changes in the hours of service regulations which govern the amount of time a driver may drive or work in any specific period, onboard black box recorder device requirements or limits on vehicle weight and size.
Interstate motor carrier operations are subject to safety requirements prescribed by the Federal Motor Carrier Safety Administration, or FMCSA, a unit within the United States Department of Transportation. To a large degree, intrastate motor carrier operations are subject to state safety regulations that mirror federal regulations. Matters such as the weight and dimensions of equipment are also subject to federal and state regulations. From time to time, various legislative proposals are introduced, including proposals to increase federal, state or local taxes, including taxes on motor fuels, which may increase our costs or adversely impact the recruitment of drivers. We cannot predict whether, or in what form, any increase in such taxes applicable to us will be enacted.
Certain motor vehicle operators require registration with the Department of Transportation. This registration requires an acceptable operating record. The Department of Transportation periodically conducts compliance reviews and may revoke registration privileges based on certain safety performance criteria which could result in a suspension of operations. The rating scale consists of “satisfactory,” “conditional” and “unsatisfactory” ratings. As of December 31, 2016, all of our trucking operations have “satisfactory” ratings with the Department of Transportation. We have undertaken comprehensive efforts that we believe are adequate to comply with the regulations. Further information regarding our safety performance is available at the FMCSA website at www.fmcsa.dot.gov.
In December 2010, the FMCSA launched a program called Compliance, Safety, Accountability, or CSA, in an effort to improve commercial truck and bus safety. A component of CSA is the Safety Measurement System, or SMS, which analyzes all safety violations recorded by federal and state law enforcement personnel to determine a carrier’s safety performance. The SMS is intended to allow FMCSA to identify carriers with safety issues and intervene to address those problems. However, the
agency has announced a future intention to revise its safety rating system by making greater use of SMS data in lieu of on-site compliance audits of carriers. At this time, we cannot predict the effect such a revision may have on our safety rating.
Environmental Matters and Regulation
Our operations are subject to stringent laws and regulations governing the discharge of materials into the environment or otherwise relating to environmental protection. Numerous federal, state and local governmental agencies, such as the U.S. Environmental Protection Agency, or the EPA, issue regulations that often require difficult and costly compliance measures that carry substantial administrative, civil and criminal penalties and may result in injunctive obligations for non-compliance. These laws and regulations may require the acquisition of a permit before drilling commences, restrict the types, quantities and concentrations of various substances that can be released into the environment in connection with drilling activities, limit or prohibit construction or drilling activities on certain lands lying within wilderness, wetlands, ecologically or seismically sensitive areas and other protected areas, require action to prevent or remediate pollution from current or former operations, such as plugging abandoned wells or closing pits, result in the suspension or revocation of necessary permits, licenses and authorizations, require that additional pollution controls be installed and impose substantial liabilities for pollution resulting from our operations or related to our owned or operated facilities. Liability under such laws and regulations is strict (i.e., no showing of “fault” is required) and can be joint and several. Moreover, it is not uncommon for neighboring landowners and other third parties to file claims for personal injury and property damage allegedly caused by the release of hazardous substances, hydrocarbons or other waste products into the environment. Changes in environmental laws and regulations occur frequently, and any changes that result in more stringent and costly pollution control or waste handling, storage, transport, disposal or cleanup requirements could materially adversely affect our operations and financial position, as well as the oil and natural gas industry in general. We have not experienced any material adverse effect from compliance with these environmental requirements. This trend, however, may not continue in the future.
Waste Handling. We handle, transport, store and dispose of wastes that are subject to the federal Resource Conservation and Recovery Act, as amended, or RCRA, and comparable state statutes and regulations promulgated thereunder, which affect our activities by imposing requirements regarding the generation, transportation, treatment, storage, disposal and cleanup of hazardous and non-hazardous wastes. With federal approval, the individual states administer some or all of the provisions of RCRA, sometimes in conjunction with their own, more stringent requirements. Although certain petroleum production wastes are exempt from regulation as hazardous wastes under RCRA, such wastes may constitute “solid wastes” that are subject to the less stringent requirements of non-hazardous waste provisions.
Administrative, civil and criminal penalties can be imposed for failure to comply with waste handling requirements. Moreover, the EPA or state or local governments may adopt more stringent requirements for the handling of non-hazardous wastes or categorize some non-hazardous wastes as hazardous for future regulation. Indeed, legislation has been proposed from time to time in Congress to re-categorize certain oil and natural gas exploration, development and production wastes as “hazardous wastes.” Several environmental organizations have also petitioned the EPA to modify existing regulations to recategorize certain oil and natural gas exploration, development and production wastes as “hazardous.” Also, in December 2015, the EPA agreed in a consent decree to review its regulation of oil and gas waste. It has until March 2019 to determine whether any revisions are necessary. Any such changes in the laws and regulations could have a material adverse effect on our capital expenditures and operating expenses. Although we do not believe the current costs of managing our wastes, as presently classified, to be significant, any legislative or regulatory reclassification of oil and natural gas exploration and production wastes could increase our costs to manage and dispose of such wastes.
Remediation of Hazardous Substances. The Comprehensive Environmental Response, Compensation and Liability Act, as amended, which we refer to as CERCLA, or the “Superfund” law, and analogous state laws, generally imposes liability, without regard to fault or legality of the original conduct, on classes of persons who are considered to be responsible for the release of a “hazardous substance” into the environment. These persons include the current owner or operator of a contaminated facility, a former owner or operator of the facility at the time of contamination and those persons that disposed or arranged for the disposal of the hazardous substance at the facility. Under CERCLA and comparable state statutes, persons deemed “responsible parties” are subject to strict liability, that, in some circumstances, may be joint and several for the costs of removing or remediating previously disposed wastes (including wastes disposed of or released by prior owners or operators) or property contamination (including groundwater contamination), for damages to natural resources and for the costs of certain health studies. In addition, it is not uncommon for neighboring landowners and other third parties to file claims for personal injury and property damage allegedly caused by the hazardous substances released into the environment. In the course of our operations, we use materials that, if released, would be subject to CERCLA and comparable state statutes. Therefore, governmental agencies or third parties may seek to hold us responsible under CERCLA and comparable state statutes for all or part of the costs to clean up sites at which such “hazardous substances” have been released.
NORM. In the course of our operations, some of our equipment may be exposed to naturally occurring radioactive materials associated with oil and gas deposits and, accordingly may result in the generation of wastes and other materials containing naturally occurring radioactive materials, or NORM. NORM exhibiting levels of naturally occurring radiation in excess of established state standards are subject to special handling and disposal requirements, and any storage vessels, piping and work area affected by NORM may be subject to remediation or restoration requirements. Because certain of the properties presently or previously owned, operated or occupied by us may have been used for oil and gas production operations, it is possible that we may incur costs or liabilities associated with NORM.
Water Discharges. The Federal Water Pollution Control Act of 1972, as amended, also known as the “Clean Water Act,” the Safe Drinking Water Act, the Oil Pollution Act and analogous state laws and regulations promulgated thereunder impose restrictions and strict controls regarding the unauthorized discharge of pollutants, including produced waters and other gas and oil wastes, into navigable waters of the United States, as well as state waters. The discharge of pollutants into regulated waters is prohibited, except in accordance with the terms of a permit issued by the EPA or the state. The Clean Water Act and regulations implemented thereunder also prohibit the discharge of dredge and fill material into regulated waters, including jurisdictional wetlands, unless authorized by a permit issued by the U.S. Army Corps of Engineers, which we refer to as the Corps. In September 2015, a new EPA and the Corps rule defining the scope of the jurisdiction of the EPA and the Corps over wetlands and other waters became effective. To the extent the rule expands the range of properties subject to the Clean Water Act’s jurisdiction, certain energy companies could face increased costs and delays with respect to obtaining permits for dredge and fill activities in wetland areas. The rule has been challenged in court on the grounds that it unlawfully expands the reach of Clean Water Act programs, and implementation of the rule has been stayed pending resolution of the court challenge. The process for obtaining permits has the potential to delay the development of natural gas and oil projects. Also, spill prevention, control and countermeasure plan requirements under federal law require appropriate containment berms and similar structures to help prevent the contamination of navigable waters. Noncompliance with these requirements may result in substantial administrative, civil and criminal penalties, as well as injunctive obligations.
Air Emissions. The federal Clean Air Act, as amended, and comparable state laws and regulations, regulate emissions of various air pollutants through the issuance of permits and the imposition of other requirements. The EPA has developed, and continues to develop, stringent regulations governing emissions of air pollutants at specified sources. New facilities may be required to obtain permits before work can begin, and existing facilities may be required to obtain additional permits and incur capital costs in order to remain in compliance. For example, our sand proppant production operations are subject to air permits issued by the Wisconsin Department of Natural Resources regulating our emission of fugitive dust and other constituents. These and other laws and regulations may increase the costs of compliance for some facilities where we operate, and federal and state regulatory agencies can impose administrative, civil and criminal penalties for non-compliance with air permits or other requirements of the federal Clean Air Act and associated state laws and regulations. Obtaining or renewing permits has the potential to delay the development of oil and natural gas projects.
Climate Change. In December 2009, the EPA issued an Endangerment Finding that determined that emissions of carbon dioxide, methane and other greenhouse gases, or collectively referred to as GHGs, present an endangerment to public health and the environment because, according to the EPA, emissions of such gases contribute to the warming of the earth’s atmosphere and other climatic changes. These findings by the EPA allowed the agency to proceed with the adoption and implementation of regulations that would restrict emissions of GHGs under existing provisions of the federal Clean Air Act. Subsequently, the EPA adopted two sets of related rules, one of which purports to regulate emissions of GHGs from motor vehicles and the other of which regulates emissions of GHGs from certain large stationary sources of emissions such as power plants or industrial facilities. The EPA adopted the stationary source rule, which we refer to as the tailoring rule, in May 2010, and it became effective January 2011. The tailoring rule established new GHG emissions thresholds that determine when stationary sources must obtain permits under the PSD and Title V programs of the Clean Air Act. On June 23, 2014, in Utility Air Regulatory Group v. EPA, the Supreme Court held that stationary sources could not become subject to PSD or Title V permitting solely by reason of their GHG emissions. The Court ruled, however, that the EPA may require installation of best available control technology for GHG emissions at sources otherwise subject to the PSD and Title V programs. On August 26, 2016, the EPA proposed changes needed to bring EPA’s air permitting regulations in line with the Supreme Court’s decision on GHG permitting. The proposed rule was published in the Federal Register on October 3, 2016 and the public comment period closed on December 2, 2016.
Additionally, in September 2009, the EPA issued a final rule requiring the reporting of GHG emissions from specified large GHG emission sources in the U.S., including natural gas liquids fractionators and local natural gas distribution companies, beginning in 2011 for emissions occurring in 2010. In November 2010, the EPA expanded the GHG reporting rule to include onshore and offshore oil and natural gas production and onshore processing, transmission, storage and distribution facilities, which may include certain of our customers’ facilities, beginning in 2012 for emissions occurring in 2011. In October
2015, the EPA amended the GHG reporting rule to add the reporting of GHG emissions from gathering and boosting systems, completions and workovers of oil wells using hydraulic fracturing, and blowdowns of natural gas transmission pipelines.
The EPA has continued to adopt GHG regulations applicable to other industries, such as its August 2015 adoption of three separate, but related, actions to address carbon dioxide pollution from power plants, including final Carbon Pollution Standards for new, modified and reconstructed power plants, a final Clean Power Plan to cut carbon dioxide pollution from existing power plants, and a proposed federal plan to implement the Clean Power Plan emission guidelines. Upon publication of the Clean Power Plan on October 23, 2015, more than two dozen states as well as industry and labor groups challenged the Clean Power Plan in the D.C. Circuit Court of Appeals. On February 9, 2016, the Supreme Court stayed implementation of the Clean Power Plan while legal challenges to the rule proceed. As a result of this continued regulatory focus, future GHG regulations of the oil and gas industry remain a possibility, which could increase the cost of our operation and reduce the demand for our products and services.
In addition, the U.S. Congress has from time to time considered adopting legislation to reduce emissions of GHGs and almost one-half of the states have already taken legal measures to reduce emissions of GHGs primarily through the planned development of GHG emission inventories and/or regional GHG cap and trade programs. Although the U.S. Congress has not adopted such legislation at this time, it may do so in the future and many states continue to pursue regulations to reduce GHG emissions. Most of these cap and trade programs work by requiring major sources of emissions, such as electric power plants or major producers of fuels, such as refineries and gas processing plants, to acquire and surrender emission allowances corresponding with their annual emissions of GHGs. The number of allowances available for purchase is reduced each year until the overall GHG emission reduction goal is achieved. As the number of GHG emission allowances declines each year, the cost or value of such allowances is expected to escalate significantly.
In December 2015, the United States participated in the 21st Conference of the Parties of the United Nations Framework Convention on Climate Change in Paris, France. The resulting Paris Agreement calls for the parties to undertake “ambitious efforts” to limit the average global temperature, and to conserve and enhance sinks and reservoirs of greenhouse gases. The Agreement went into effect on November 4, 2016. The Paris Agreement establishes a framework for the parties to cooperate and report actions to reduce greenhouse gas emissions. Also, on June 29, 2016, the leaders of the United States, Canada and Mexico announced an Action Plan to, among other things, boost clean energy, improve energy efficiency, and reduce GHG emissions. The Action Plan specifically calls for a reduction in methane emissions from the oil and gas sector by 40 to 45 percent by 2025.
Restrictions on emissions of methane or carbon dioxide that may be imposed could adversely affect the oil and natural gas industry by reducing demand for hydrocarbons and by making it more expensive to develop and produce hydrocarbons, either of which could have a material adverse effect on future demand for our services. At this time, it is not possible to accurately estimate how potential future laws or regulations addressing GHG emissions would impact our business. It also remains unclear whether and how the results of the 2016 U.S. election could impact the regulation of GHG emissions at the federal and state level.
In addition, claims have been made against certain energy companies alleging that greenhouse gas emissions from oil and natural gas operations constitute a public nuisance under federal and/or state common law. As a result, private individuals may seek to enforce environmental laws and regulations against certain energy companies and could allege personal injury or property damages. While our business is not a party to any such litigation, we could be named in actions making similar allegations. An unfavorable ruling in any such case could significantly impact our operations and could have an adverse impact on our financial condition. Moreover, climate change may cause more extreme weather conditions such as more intense hurricanes, thunderstorms, tornadoes and snow or ice storms, as well as rising sea levels and increased volatility in seasonal temperatures. Extreme weather conditions can interfere with our productivity and increase our costs and damage resulting from extreme weather may not be fully insured. However, at this time, we are unable to determine the extent to which climate change may lead to increased storm or weather hazards affecting our operations.
Endangered Species Act
Environmental laws such as the Endangered Species Act, as amended, or the ESA, may impact exploration, development and production activities on public or private lands. The ESA provides broad protection for species of fish, wildlife and plants that are listed as threatened or endangered in the U.S.. Similar protections are offered to migratory birds under the Migratory Bird Treaty Act. Federal agencies are required to insure that any action authorized, funded or carried out by them is not likely to jeopardize the continued existence of listed species or modify their critical habitat. While some of our facilities may be located in areas that are designated as habitat for endangered or threatened species, we believe that we are in substantial compliance with the ESA. The U.S. Fish and Wildlife Service may identify, however, previously unidentified
endangered or threatened species or may designate critical habitat and suitable habitat areas that it believes are necessary for survival of a threatened or endangered species, which could cause us to incur additional costs or become subject to operating restrictions or bans in the affected areas.
Regulation of Hydraulic Fracturing
Our business is dependent on our ability to conduct hydraulic fracturing and horizontal drilling activities. Hydraulic fracturing is an important and common practice that is used to stimulate production of hydrocarbons, particularly natural gas, from tight formations, including shales. The process, which involves the injection of water, sand and chemicals (also called “proppants”) under pressure into formations to fracture the surrounding rock and stimulate production, is typically regulated by state oil and natural gas commissions. However, federal agencies have asserted regulatory authority over certain aspects of the process. For example, the EPA has taken the position that hydraulic fracturing with fluids containing diesel fuel is subject to regulation under the Underground Injection Control program, specifically as “Class II” Underground Injection Control wells under the Safe Drinking Water Act. In addition, the EPA plans to develop a Notice of Proposed Rulemaking by June 2018, which would describe a proposed mechanism - regulatory, voluntary, or a combination of both - to collect data on hydraulic fracturing chemical substances and mixtures. Also, on June 28, 2016, the EPA published a final rule prohibiting the discharge of wastewater from onshore unconventional oil and natural gas extraction facilities to publicly owned wastewater treatment plans. The EPA is also conducting a study of private wastewater treatment facilities (also known as centralized waste treatment, or CWT, facilities) accepting oil and natural gas extraction wastewater. The EPA is collecting data and information related to the extent to which CWT facilities accept such wastewater, available treatment technologies (and their associated costs), discharge characteristics, financial characteristics of CWT facilities and the environmental impacts of discharges from CWT facilities. Furthermore, legislation to amend the Safe Drinking Water Act, or SDWA, to repeal the exemption for hydraulic fracturing (except when diesel fuels are used) from the definition of “underground injection” and require federal permitting and regulatory control of hydraulic fracturing, as well as legislative proposals to require disclosure of the chemical constituents of the fluids used in the fracturing process, were proposed in recent sessions of Congress.
On August 16, 2012, the EPA published final regulations under the federal Clean Air Act that establish new air emission controls for oil and natural gas production and natural gas processing operations. Specifically, the EPA’s rule package includes New Source Performance standards, which we refer to as NSP standards, to address emissions of sulfur dioxide and volatile organic compounds and a separate set of emission standards to address hazardous air pollutants frequently associated with oil and natural gas production and processing activities. The final rule seeks to achieve a 95% reduction in volatile organic compounds emitted by requiring the use of reduced emission completions or “green completions” on all hydraulically-fractured wells constructed or refractured after January 1, 2015. The rules also establish specific new requirements regarding emissions from compressors, controllers, dehydrators, storage tanks and other production equipment. The EPA received numerous requests for reconsideration of these rules from both industry and the environmental community, and court challenges to the rules were also filed. In response, the EPA has issued, and will likely continue to issue, revised rules responsive to some of the requests for reconsideration. In particular, on May 12, 2016, the EPA amended the NSP standards to impose new standards for methane and VOC emissions for certain new, modified and reconstructed equipment, processes and activities across the oil and natural gas sector. On the same day, the EPA finalized a plan to implement its minor new source review program on Indian lands for oil and natural gas production, and it issued for public comment an information request that will require companies to provide extensive information instrumental for the development of regulations to reduce methane emissions from existing oil and gas sources. These standards, as well as any future laws and their implementing regulations, may require us to obtain pre-approval for the expansion or modification of existing facilities or the construction of new facilities expected to produce air emissions, impose stringent air permit requirements, or mandate the use of specific equipment or technologies to control emissions.
In addition, on March 26, 2015, the Bureau of Land Management, or BLM, published a final rule governing hydraulic fracturing on federal and Indian lands. The rule requires public disclosure of chemicals used in hydraulic fracturing, implementation of a casing and cementing program, management of recovered fluids, and submission to the BLM of detailed information about the proposed operation, including wellbore geology, the location of faults and fractures, and the depths of all usable water. On June 21, 2016, the United States District Court for Wyoming set aside the rule, holding that the BLM lacked Congressional authority to promulgate the rule. The BLM has appealed the decision to the Tenth Circuit Court of Appeals. Also, on November 15, 2016, the BLM finalized a rule to reduce the flaring, venting and leaking of methane from oil and gas operations on federal and Indian lands. The rule requires operators to use currently available technologies and equipment to reduce flaring, periodically inspect their operations for leaks, and replace outdated equipment that vents large quantities of gas into the air. The rule also clarifies when operators owe the government royalties for flared gas. State and industry groups have challenged this rule in federal court, asserting that the BLM lacks authority to prescribe air quality regulations. Congressional measure to repeal this rule is currently pending.
There are certain governmental reviews either underway or being proposed that focus on the environmental aspects of hydraulic fracturing practices. The EPA is currently evaluating the potential impacts of hydraulic fracturing on drinking water resources. On December 13, 2016, the EPA released a study examining the potential for hydraulic fracturing activities to impact drinking water resources, finding that, under some circumstances, the use of water in hydraulic fracturing activities can impact drinking water resources. Also, on February 6, 2015, the EPA released a report with findings and recommendations related to public concern about induced seismic activity from disposal wells. The report recommends strategies for managing and minimizing the potential for significant injection-induced seismic events. Other governmental agencies, including the U.S. Department of Energy, the U.S. Geological Survey, and the U.S. Government Accountability Office, have evaluated or are evaluating various other aspects of hydraulic fracturing. These ongoing or proposed studies, depending on their degree of pursuit and whether any meaningful results are obtained, could spur initiatives to further regulate hydraulic fracturing, and could ultimately make it more difficult or costly for us to perform fracturing and increase our costs of compliance and doing business.
Several states and local jurisdictions in which we or our customers operate have adopted or are considering adopting regulations that could restrict or prohibit hydraulic fracturing in certain circumstances, impose more stringent operating standards and/or require the disclosure of the composition of hydraulic fracturing fluids. Any increased regulation of hydraulic fracturing could reduce the demand for our services and materially and adversely effect our reserves and results of operations.
There has been increasing public controversy regarding hydraulic fracturing with regard to the use of fracturing fluids, induced seismic activity, impacts on drinking water supplies, use of water and the potential for impacts to surface water, groundwater and the environment generally. A number of lawsuits and enforcement actions have been initiated across the country implicating hydraulic fracturing practices. If new laws or regulations that significantly restrict hydraulic fracturing are adopted, such laws could make it more difficult or costly for us to perform fracturing to stimulate production from tight formations as well as make it easier for third parties opposing the hydraulic fracturing process to initiate legal proceedings based on allegations that specific chemicals used in the fracturing process could adversely affect groundwater. In addition, if hydraulic fracturing is further regulated at the federal, state or local level, our customers’ fracturing activities could become subject to additional permitting and financial assurance requirements, more stringent construction specifications, increased monitoring, reporting and recordkeeping obligations, plugging and abandonment requirements and also to attendant permitting delays and potential increases in costs. Such legislative or regulatory changes could cause us or our customers to incur substantial compliance costs, and compliance or the consequences of any failure to comply by us could have a material adverse effect on our financial condition and results of operations. At this time, it is not possible to estimate the impact on our business of newly enacted or potential federal, state or local laws governing hydraulic fracturing.
Regulation of Sand Proppant Production
The MSHA has primary regulatory jurisdiction over commercial silica operations, including quarries, surface mines, underground mines and industrial mineral processing facilities. While we do not directly conduct any mining operations, we are dependent on several regulated mines for the supply of natural sand used in our proppant production. In addition, MSHA representatives perform at least two annual inspections of our production facilities to ensure employee and general site safety. To date, these inspections have not resulted in any citations for material violations of MSHA standards, and we believe we are in material compliance with MSHA requirements.
Other Regulation of the Oil and Natural Gas Industry
The oil and natural gas industry is extensively regulated by numerous federal, state and local authorities. Legislation affecting the oil and natural gas industry is under constant review for amendment or expansion, frequently increasing the regulatory burden. Also, numerous departments and agencies, both federal and state, are authorized by statute to issue rules and regulations that are binding on the oil and natural gas industry and its individual members, some of which carry substantial penalties for failure to comply. Although changes to the regulatory burden on the oil and natural gas industry could affect the demand for our services, we would not expect to be affected any differently or to any greater or lesser extent than other companies in the industry with similar operations.
Drilling. Our operations are subject to various types of regulation at the federal, state and local level. These types of regulation include requiring permits for the drilling of wells, drilling bonds and reports concerning operations. The states, and some counties and municipalities, in which we operate also regulate one or more of the following:
| |
• | the method of drilling and casing wells; |
| |
• | the timing of construction or drilling activities, including seasonal wildlife closures; |
| |
• | the surface use and restoration of properties upon which wells are drilled; |
| |
• | the plugging and abandoning of wells; and |
| |
• | notice to, and consultation with, surface owners and other third parties. |
Federal, state and local regulations provide detailed requirements for the abandonment of wells, closure or decommissioning of production facilities and pipelines and for site restoration in areas where we operate. The Corps and many other state and local authorities also have regulations for plugging and abandonment, decommissioning and site restoration. Although the Corps does not require bonds or other financial assurances, some state agencies and municipalities do have such requirements.
State Regulation. The states in which we or our customers operate regulate the drilling for, and the production and gathering of, oil and natural gas, including through requirements relating to the method of developing new fields, the spacing and operation of wells and the prevention of waste of oil and natural gas resources. States may also regulate rates of production and may establish maximum daily production allowables from oil and natural gas wells based on market demand or resource conservation, or both. States do not regulate wellhead prices or engage in other similar direct economic regulation, but they may do so in the future. The effect of these regulations may be to limit the amount of oil and natural gas that may be produced from wells and to limit the number of wells or locations our customers can drill.
In July 2015, the Ohio Department of Natural Resources, or the ODNR, enacted a comprehensive set of rules to regulate the construction of well pads. Under these new rules, operators must submit detailed horizontal well pad site plans certified by a professional engineer for review by the ODNR Division of Oil and Gas Resources Management prior to the construction of a well pad. These rules will result in increased construction costs for operators. It is expected that the ODNR will pursue further initiatives in 2017, including additional well spacing rules.
The petroleum industry is also subject to compliance with various other federal, state and local regulations and laws. Some of those laws relate to resource conservation and equal employment opportunity. We do not believe that compliance with these laws will have a material adverse effect on us.
OSHA Matters
We are also subject to the requirements of the federal Occupational Safety and Health Act, or OSHA, and comparable state statutes that regulate the protection of the health and safety of workers. In addition, the OSHA hazard communication standard requires that information be maintained about hazardous materials used or produced in operations and that this information be provided to employees, state and local government authorities and the public. Compliance with these laws and regulations has not had a material adverse effect on our operations or financial position.
Employees
As of December 31, 2016, we had approximately 520 full time employees, including 160 salaried administrative or supervisory employees. None of our employees are represented by labor unions or covered by any collective bargaining agreements. We also hire independent contractors and consultants involved in land, technical, regulatory and other disciplines to assist our full time employees.
Availability of Company Reports
Our annual report on Form 10-K, quarterly reports on Form 10-Q, current reports on Form 8-K and all amendments to those reports filed or furnished pursuant to Section 13(a) or 15(d) of the Exchange Act are made available free of charge on the Investor Relations page of our website at www.mammothenergy.com as soon as reasonably practicable after such material is electronically filed with, or furnished to, the SEC. Information contained on our website, or on other websites that may be linked to our website, is not incorporated by reference into this annual report on Form 10-K and should not be considered part of this report or any other filing that we make with the SEC.
Item 1A. Risk Factors
Risks Related to Our Business and the Oil and Natural Gas Industry
Our business depends on the oil and natural gas industry and particularly on the level of exploration and production activity within the United States and Canada, and the ongoing volatility in prices for oil and natural gas has had, and continues to have, an adverse effect on our revenue, cash flows, profitability and growth.
Demand for most of our products and services depends substantially on the level of expenditures by companies in the oil and natural gas industry. The significant decline in oil and natural gas prices during 2015 continued during the first part of 2016 before seeing a rebound during the second half of 2016. The low commodity price environment caused many of our customers to reduce spending on drilling, completion and other production activities. Although the prices for oil and natural gas have recently improved, the industry conditions are dynamic and the continuation or a weakening of commodity prices from current levels may result in a material adverse impact on certain of our customers’ liquidity and financial position resulting in spending reductions, delays in the collection of amounts owing to us and similar impacts. These conditions have had and may continue to have an adverse impact on our financial condition, results of operations and cash flows, and it is difficult to predict how long the current commodity price environment will continue.
Many factors over which we have no control affect the supply of and demand for, and our customers’ willingness to explore, develop and produce oil and natural gas, and therefore, influence prices for our products and services, including:
| |
• | the domestic and foreign supply of and demand for oil and natural gas; |
| |
• | the level of prices, and expectations about future prices, of oil and natural gas; |
| |
• | the level of global oil and natural gas exploration and production; |
| |
• | the cost of exploring for, developing, producing and delivering oil and natural gas; |
| |
• | the expected decline rates of current production; |
| |
• | the price and quantity of foreign imports; |
| |
• | political and economic conditions in oil producing countries, including the Middle East, Africa, South America and Russia; |
| |
• | the ability of members of the Organization of Petroleum Exporting Countries to agree to and maintain oil price and production controls; |
| |
• | speculative trading in crude oil and natural gas derivative contracts; |
| |
• | the level of consumer product demand; |
| |
• | the discovery rates of new oil and natural gas reserves; |
| |
• | contractions in the credit market; |
| |
• | the strength or weakness of the U.S. dollar; |
| |
• | available pipeline and other transportation capacity; |
| |
• | the levels of oil and natural gas storage; |
| |
• | weather conditions and other natural disasters; |
| |
• | political instability in oil and natural gas producing countries; |
| |
• | domestic and foreign tax policy; |
| |
• | domestic and foreign governmental approvals and regulatory requirements and conditions; |
| |
• | the continued threat of terrorism and the impact of military and other action, including military action in the Middle East; |
| |
• | technical advances affecting energy consumption; |
| |
• | the proximity and capacity of oil and natural gas pipelines and other transportation facilities; |
| |
• | the price and availability of alternative fuels; |
| |
• | the ability of oil and natural gas producers to raise equity capital and debt financing; |
| |
• | merger and divestiture activity among oil and natural gas producers; and |
| |
• | overall domestic and global economic conditions. |
These factors and the volatility of the energy markets make it extremely difficult to predict future oil and natural gas price movements with any certainty. Any of the above factors could impact the level of oil and natural gas exploration and production activity and could ultimately have a material adverse effect on our business, financial condition, results of operations and cash flows. Further, future weakness in commodity prices could impact our business going forward, and we could encounter difficulties such as an inability to access needed capital on attractive terms or at all, recognizing asset impairment charges, an inability to meet financial ratios contained in our debt agreements, a need to reduce our capital spending and other similar impacts.
The cyclicality of the oil and natural gas industry may cause our operating results to fluctuate.
We derive our revenues from companies in the oil and natural gas exploration and production industry, a historically cyclical industry with levels of activity that are significantly affected by the levels and volatility of oil and natural gas prices. We have, and may in the future, experience significant fluctuations in operating results as a result of the reactions of our customers to changes in oil and natural gas prices. For example, prolonged low commodity prices experienced by the oil and natural gas industry during 2015 and the first part of 2016, combined with adverse changes in the capital and credit markets, caused many exploration and production companies to reduce their capital budgets and drilling activity. This resulted in a
significant decline in demand for oilfield services and adversely impacted the prices oilfield services companies could charge for their services. In addition, a majority of the service revenue we earn is based upon a charge for a relatively short period of time (e.g., an hour, a day, a week) for the actual period of time the service is provided to our customers. By contracting services on a short-term basis, we are exposed to the risks of a rapid reduction in market prices and utilization, with resulting volatility in our revenues.
If oil prices or natural gas prices remain at current levels or decline further, the demand for our services could be adversely affected.
The demand for our services is primarily determined by current and anticipated oil and natural gas prices and the related general production spending and level of drilling activity in the areas in which we have operations. Volatility or weakness in oil prices or natural gas prices (or the perception that oil prices or natural gas prices will decrease) affects the spending patterns of our customers and may result in the drilling of fewer new wells or lower production spending on existing wells. This, in turn, could result in lower demand for our services and may cause lower rates and lower utilization of our well service equipment. Any future decline in oil and gas prices could materially affect the demand for our services and our results of operations could be materially and adversely affected. Prices for oil and natural gas historically have been extremely volatile and are expected to continue to be volatile in the years to come. During 2016, the posted WTI price for oil has ranged from a low of $26.19 per Bbl, on February 11, 2016 to a high of $54.06 per Bbl on December 28, 2016. The Henry Hub spot market price of natural gas has ranged from a low of $1.64 per MMBtu on March 3, 2016 to a high of $3.93 per MMBtu on December 28, 2016. During 2015, WTI prices ranged from $34.95 to $61.43 per Bbl and the Henry Hub spot market price of natural gas ranged from $1.76 to $3.21 per MMBtu. If the prices of oil and natural gas decline from current levels, our operations, financial condition and level of expenditures may be materially and adversely affected.
Our business is difficult to evaluate because we have a limited operating history.
Mammoth Energy Services, Inc. was formed in June 2016, and did not conduct any material business operations prior to the IPO, which closed on October 19, 2016. Prior to the IPO, Mammoth Energy Services, Inc. was a wholly-owned subsidiary of Mammoth Partners, which was originally formed in February 2014. Except as expressly noted otherwise, the historical financial information of Mammoth Energy Services, Inc. and operational data described in this annual report for the periods prior to October 12, 2016 is that of Mammoth Partners and its consolidated subsidiaries. These subsidiaries were formed or acquired between 2007 and 2016. As a result, there is only limited historical financial and operating information available upon which to base your evaluation of our performance.
Our customer base is concentrated and the loss of one or more of our significant customers, or their failure to pay the amounts they owe us, could cause our revenue to decline substantially.
Our top five customers accounted for approximately 80% and 71% of our revenue for the years ended December 31, 2016 and 2015, respectively. Gulfport was our largest customer accounting for approximately 57% and 47% of our revenue for such years. It is likely that we will continue to derive a significant portion of our revenue from a relatively small number of customers in the future. If a major customer decided not to continue to use our services, our revenue would decline and our operating results and financial condition could be harmed. For example, effective January 1, 2016, we entered into an amendment to our master services agreement with Gulfport in which Gulfport suspended its use of our hydraulic fracturing services during the first quarter of 2016. As a result, there were no revenues attributable to these services from Gulfport during the first quarter of 2016 as compared to $25.8 million for the fourth quarter of 2015 and approximately $124.3 million during the year ended December 31, 2015. Under the amendment, the services that were suspended during the first quarter, and the related fees, were performed and paid for during the second and third quarters of 2016. We recognized revenues of $38.2 million and $35.4 million from Gulfport for these services during the second and third quarters of 2016, respectively. In addition, we are subject to credit risk due to the concentration of our customer base. Any nonperformance by our counterparties, including their failure to pay the amounts they owe us, either as a result of changes in financial and economic conditions or otherwise, could have an adverse impact on our operating results and could adversely affect our liquidity.
We provide the majority of our hydraulic fracturing completion services to Gulfport, and the termination of this relationship could adversely affect our operations.
We provide completion services, which services include hydraulic fracturing. The majority of our revenue from this business is derived from Gulfport pursuant to a contract that expires in September 2018. We cannot assure you that we will be able to extend or renew our contract with Gulfport on favorable terms and conditions or at all. Likewise, we cannot assure you that we would be able to obtain a replacement long-term contract with other customers sufficient to continue providing the
level of services as we currently do with Gulfport. The termination of our relationship or nonrenewal of our contract with Gulfport could have a material adverse effect on our business, financial condition, results of operations and cash flows.
We provide natural sand proppant to a limited number of customers, and the termination of one or more of these relationships could adversely affect our operations.
We provide natural sand proppant used for hydraulic fracturing. The majority of our revenue from this business is derived from Gulfport pursuant to a contract that expires in September 2018. The termination of our relationship or nonrenewal of our contract with Gulfport, or one or more of our other customers, could have a material adverse effect on our business, financial condition, results of operations and cash flows.
We provide our remote accommodation services to a limited number of customers, and the termination of one or more of these or other relationships could adversely affect our operations.
In our other energy services division, we provide turnkey remote accommodations services for oilfield related labor located in remote areas, which services include site identification, permitting and development, facility design, construction, installation and full site maintenance. Approximately 85% of these services during the year ended December 31, 2016 were attributable to Oil Sands Limited. We anticipate that Oil Sands Limited’s occupancy of our accommodations will decrease by at least 70% in 2017 following the completion of the construction phase of its project in the service area, which is currently estimated to occur in early 2017. During the fourth quarter of 2016, our revenue from this customer was $6.9 million, or 90% of our other energy service revenues during that period. Our failure to replace the revenue received from this customer will have a material adverse effect on the financial results of our other energy services division and could have a material adverse effect on our consolidated results of operations and financial condition. The termination of our relationship with any other of our remote accommodation customers could also have a material adverse effect on this part of our business. Further, our remote accommodation services are provided in Canada on tribal lands. Our failure to maintain favorable relationships with these tribes could adversely affect our operations and financial results.
Deterioration of the commodity price environment can negatively impact oil and natural gas exploration and production companies and, in some cases, impair their ability to timely pay for products or services provided or result in their insolvency or bankruptcy, any of which exposes us to credit risk of our oil and natural gas exploration and production customers.
In weak economic and commodity price environments, we may experience increased difficulties, delays or failures in collecting outstanding receivables from our customers, due to, among other reasons, a reduction in their cash flow from operations, their inability to access the credit markets and, in certain cases, their insolvencies. Such increases in collection issues could have a material adverse effect on our business, results of operations, cash flows and financial condition. We cannot assure you that the reserves we have established for potential credit losses will be sufficient to meet write-offs of uncollectible receivables or that our losses from such receivables will be consistent with our expectations. To the extent one or more of our key customers commences bankruptcy proceedings, our contracts with these customers may be subject to rejection under applicable provisions of the United States Bankruptcy Code, or may be renegotiated. Further, during any such bankruptcy proceeding, prior to assumption, rejection or renegotiation of such contracts, the bankruptcy court may temporarily authorize the payment of value for our services less than contractually required, which could also have a material adverse effect on our business, results of operations, cash flows and financial condition.
Competition within the oilfield services industry may adversely affect our ability to market our services.
The oilfield services industry is highly competitive and fragmented and includes numerous small companies capable of competing effectively in our markets on a local basis, as well as several large companies that possess substantially greater financial and other resources than we do. Our larger competitors’ greater resources could allow those competitors to compete more effectively than we can. The amount of equipment available may exceed demand, which could result in active price competition. Many contracts are awarded on a bid basis, which may further increase competition based primarily on price. In addition, adverse market conditions lower demand for well servicing equipment, which results in excess equipment and lower utilization rates. If market conditions in our oil-oriented operating areas were to deteriorate or if adverse market conditions in our natural gas-oriented operating areas persist, utilization rates may decline.
Shortages, delays in delivery and interruptions in supply of drill pipe, replacement parts, other equipment, supplies and materials may adversely affect our contract land and directional drilling business or our pressure pumping business.
During periods of increased demand for drilling services, the industry has experienced shortages of drill pipe, replacement parts, other equipment, supplies and materials, including, in the case of our pressure pumping operations, proppants, acid, gel and water. These shortages can cause the price of these items to increase significantly and require that orders for the items be placed well in advance of expected use. In addition, any interruption in supply could result in significant delays in delivery of equipment and materials or prevent operations. Interruptions may be caused by, among other reasons:
| |
• | weather issues, whether short-term such as a hurricane, or long-term such as a drought, and |
| |
• | shortage in the number of vendors able or willing to provide the necessary equipment, supplies and materials, including as a result of commitments of vendors to other customers or third parties. |
These price increases, delays in delivery and interruptions in supply may require us to increase capital and repair expenditures and incur higher operating costs. Severe shortages, delays in delivery and interruptions in supply could limit our ability to construct and operate our drilling rigs and could have a material adverse effect on our business, financial condition, cash flows and results of operations.
Oilfield services equipment, refurbishment and new asset construction projects, as well as the reactivation of oilfield service assets that have been idle for six months or longer, are subject to risks which could cause delays or cost overruns and adversely affect our cash flows, results of operations and financial position.
Oilfield services equipment or assets being upgraded, converted or re-activated following a period of inactivity may experience start-up complications and may encounter other operational problems that could result in significant delays, uncompensated downtime, reduced dayrates or the cancellation, termination or non-renewal of contracts. Construction and upgrade projects are subject to risks of delay or significant cost overruns inherent in any large construction project from numerous factors, including the following:
| |
• | shortages of equipment, materials or skilled labor; |
| |
• | unscheduled delays in the delivery of ordered materials and equipment or shipyard construction; |
| |
• | failure of equipment to meet quality and/or performance standards; |
| |
• | financial or operating difficulties of equipment vendors; |
| |
• | unanticipated actual or purported change orders; |
| |
• | inability by us or our customer to obtain required permits or approvals, or to meet applicable regulatory standards in our areas of operations; |
| |
• | unanticipated cost increases between order and delivery; |
| |
• | adverse weather conditions and other events of force majeure; |
| |
• | design or engineering changes; and |
| |
• | work stoppages and other labor disputes. |
The occurrence of any of these events could have a material adverse effect on our cash flows, results of operations and financial position.
Advancements in oilfield service technologies could have a material adverse effect on our business, financial condition, results of operations and cash flows.
The oilfield services industry is characterized by rapid and significant technological advancements and introductions of new products and services using new technologies. As new horizontal and directional drilling, pressure pumping, pressure control and well service technologies develop, we may be placed at a competitive disadvantage, and competitive pressure may force us to implement new technologies at a substantial cost. We may not be able to successfully acquire or use new technologies. Further, our customers are increasingly demanding the services of newer, higher specification drilling rigs. There can be no assurance that we will:
| |
• | have sufficient capital resources to build new, technologically advanced equipment and other assets; |
| |
• | successfully integrate additional oilfield service equipment and other assets; |
| |
• | effectively manage the growth and increased size of our organization, equipment and other assets; |
| |
• | successfully deploy idle, stacked or additional oilfield service assets; |
| |
• | maintain crews necessary to operate additional drilling rigs or pressure pumping service equipment; or |
| |
• | successfully improve our financial condition, results of operations, business or prospects. |
If we are not successful in building or acquiring new oilfield service equipment and other assets or upgrading our existing rigs and equipment in a timely and cost-effective manner, we could lose market share. New technologies, services or
standards could render some of our services, equipment and other assets obsolete, which could have a material adverse impact on our business, financial condition and results of operation.
Our business depends upon our ability to obtain specialized equipment and parts from third-party suppliers, and we may be vulnerable to delayed deliveries and future price increases.
We purchase specialized equipment and parts from third party suppliers. At times during the business cycle, there is a high demand for hydraulic fracturing, coiled tubing and other oilfield services and extended lead times to obtain equipment needed to provide these services. Further, there are a limited number of suppliers that manufacture the equipment we use. Should our current suppliers be unable or unwilling to provide the necessary equipment and parts or otherwise fail to deliver the products timely and in the quantities required, any resulting delays in the provision of our services could have a material adverse effect on our business, financial condition, results of operations and cash flows. In addition, future price increases for this type of equipment and parts could negatively impact our ability to purchase new equipment to update or expand our existing fleet or to timely repair equipment in our existing fleet.
As part of our proppant sales and distribution business, we rely on third parties for raw materials and transportation, and the termination of our relationship with one or more of these third parties could adversely affect our operations.
As part of our proppant sales and distribution business, we buy processed sand from suppliers on the spot market and resell that sand. Although we did not do so during the year ended December 31, 2016, we also have the ability to buy raw sand, process it into premium monocrystalline sand, a specialized mineral that is used as a proppant (also known as frac sand), at our indoor sand processing plant located in Pierce County, Wisconsin and sell it to our customers for use in their hydraulic fracturing operations to enhance the recovery rates of hydrocarbons from oil and natural gas wells. We also provide logistics solutions to deliver our frac sand products to our customers. Because our customers generally find it impractical to store frac sand in large quantities near their job sites, they seek to arrange for product to be delivered where and as needed, which requires predictable and efficient loading and shipping of product. To facilitate our logistics and transload facility capabilities, we contract with third party providers to transport our frac sand products to railroad facilities for delivery to our customers. We also lease a railcar fleet from various third parties to deliver our frac sand products to our customers and lease or otherwise utilize origin and destination transloading facilities. The termination or nonrenewal of our relationship with any one or more of these third parties involved in the sourcing, transportation and delivery of our frac sand products could result in material operational delays, increase our operating costs, limit our ability to service our customers’ wells or otherwise materially and adversely affect our business and operating results.
Future performance of our proppant sales and distribution business will depend on our ability to succeed in competitive markets, and on our ability to appropriately react to potential fluctuations in the demand for and supply of frac sand.
In our proppant sales and distribution business, we operate in a highly competitive market that is characterized by a small number of large, national producers and a larger number of small, regional or local producers. Competition in the industry is based on price, consistency and quality of product, site location, distribution and logistics capabilities, customer service, reliability of supply and breadth of product offering. The large, national producers with whom we compete include Badger Mining Corporation, Fairmount Santrol Holdings, Inc., Hi-Crush Partners LP, Preferred Proppants LLC, Unimin Corporation, Smart Sand, Inc. and U.S. Silica Holdings Inc. Our larger competitors may have greater financial and other resources than we do, may develop technology superior to ours, may have production facilities that are located closer to sand mines from which raw sand is mined or to their key customers than our processing facility or have a more cost effective access to raw sand and transportation facilities that we do. Should the demand for hydraulic fracturing services decrease, prices in the frac sand market could materially decrease as producers may seek to preserve market share or exit the market and sell frac sand at below market prices. In addition, oil and natural gas exploration and production companies and other providers of hydraulic fracturing services could acquire their own frac sand reserves, develop or expand frac sand production capacity or otherwise fulfill their own proppant requirements and existing or new frac sand producers could add to or expand their frac sand production capacity, which may negatively impact pricing and demand for our frac sand. We may not be able to compete successfully against either our larger or smaller competitors in the future, and competition could have a material adverse effect on our business, financial condition, results of operations and cash flows.
An increase in the supply of raw frac sand having similar characteristics as the raw frac sand we sell or have the ability to produce could make it more difficult for us to market our sand on favorable terms or at all.
We have entered into a take-or-pay contract with our principal raw frac sand supplier. If significant new reserves of raw frac sand continue to be discovered and developed, and those frac sands have similar characteristics to the frac sand we produce, the market price for our frac sand may decline. If the market price for our frac sand falls below an amount equal to the
contracted purchase price in our take-or-pay contract plus our processing and related transportation costs, this could have an adverse effect on our results of operations and cash flows over the remaining term of this contract.
Diminished access to water and inability to secure or maintain necessary permits may adversely affect operations of our frac sand processing plant when such operations are restarted.
The processing of raw sand and production of natural sand proppant require significant amounts of water. As a result, securing water rights and water access is necessary to operate our processing facilities. If the area where our facilities are located experiences water shortages, restrictions or any other constraints due to drought, contamination or otherwise, there may be additional costs associated with securing water access. Although we have obtained water rights to service our activities when we are operating our processing plant, the amount of water that we are entitled to use pursuant to our water rights must be determined by the appropriate regulatory authorities. Such regulatory authorities may amend the regulations regarding such water rights, increase the cost of maintaining such water rights or eliminate our current water rights, and we may be unable to retain all or a portion of such water rights. If implemented, these new regulations could also affect local municipalities and other industrial operations and could have a material adverse effect on costs involved in operating our processing plant. Such changes in laws, regulations or government policy and related interpretations pertaining to water rights may alter the environment in which we do business, which may have an adverse effect on our financial condition and results of operations. Additionally, a water discharge permit may be required to properly dispose of water at our processing site when in operation. Certain of our facilities are also required to obtain storm water permits. The water discharge, storm water or any other permits we may be required to have in order to conduct our frac sand processing operations (when they are restarted) is subject to regulatory discretion, and any inability to obtain or maintain the necessary permits could have an adverse effect on our ability to run such operations.
Demand for our frac sand products could be reduced by changes in well stimulation processes and technologies, as well as changes in governmental regulations and other applicable law.
As part of our proppant sales and production business, we sell custom frac sand products to our customers for use in their hydraulic fracturing operations to enhance the recovery rates of hydrocarbons from oil and natural gas wells. A significant shift in demand from frac sand to other proppants, or the development of new processes to replace hydraulic fracturing altogether, could cause a decline in the demand for the frac sand we produce and result in a material adverse effect on our financial condition and results of operations. Further, federal and state governments and agencies have adopted various laws and regulations or are evaluating proposed legislation and regulations that are focused on the extraction of shale gas or oil using hydraulic fracturing, a process which utilizes proppants such as those that we produce. Future hydraulic fracturing-related legislation or regulations could restrict the ability of our customers to utilize, or increase the cost associated with, hydraulic fracturing, which could reduce demand for our proppants and adversely affect our financial condition, results of operations and cash flows. For additional information regarding the regulation of hydraulic fracturing, see “—Risks Related to Our Business and the Oil and Natural Gas Industry—Federal and state legislative and regulatory initiatives relating to hydraulic fracturing could result in increased costs and additional operating restrictions or delays.”
The customized nature, and remote location, of the modular camps that we provide and service present unique challenges that could adversely affect our ability to successfully operate our remote accommodations business.
We rely on a third-party subcontractor to manufacture and install the customized modular units used in our remote accommodations business. These customized units often take a considerable amount of time to manufacture and, once manufactured, often need to be delivered to remote areas that are frequently difficult to access by traditional means of transportation. In the event we are unable to provide these modular units in a timely fashion, we may not be entitled to full, or any, payment therefor under the terms of our contracts with customers. In addition, the remote location of the modular camps often makes it difficult to install and maintain the units, and our failure, on a timely basis, to have such units installed and provide maintenance services could result in our breach of, and non-payment by our customers under, the terms of our customer contracts. Any of these factors could have a material adverse effect on our remote accommodation business and our overall financial condition and results of operations.
Health and food safety issues and food-borne illness concerns could adversely affect our remote accommodations business.
We provide food services to our customers as part of our remote accommodations business and, as a result, face health and food safety issues that are common in the food and hospitality industries. Food-borne illnesses, such as E. coli, hepatitis A, trichinosis or salmonella, and food safety issues have occurred in the food industry in the past and could occur in the future. Our reliance on third-party food suppliers and distributors increases the risk that food-borne illness incidents could be caused
by factors outside of our control. New illnesses resistant to any precautions may develop in the future, or diseases with long incubation periods could arise. Further, the remote nature of our accommodation facilities and related food services may increase the risk of contamination of our food supply and create additional health and hygiene concerns due to the limited access to modern amenities and conveniences that may not be faced by other food service providers or hospitality businesses operating in urban environment. If our customers become ill from food-borne illness, we could be forced to close some or all of our remote accommodation facilities on a temporary basis or otherwise. Any such incidents and/or any report of publicity linking us to incidents of food-borne illness or other food safety issues, including food tampering or contamination, could adversely affect our remote accommodations business as well as our overall financial condition and results of operations.
Development of permanent infrastructure in the Canadian oil sands region or other locations where we locate our remote accommodations could negatively impact our remote accommodations business.
Our remote accommodations business specializes in providing modular housing and related services for work forces in remote areas which lack the infrastructure typically available in towns and cities. If permanent towns, cities and municipal infrastructure develop in the oil sands region of northern Alberta, Canada or other regions where we locate our modular camps, then demand for our accommodations could decrease as customer employees move to the region and choose to utilize permanent housing and food services.
Revenue generated and expenses incurred by our remote accommodation business are denominated in the Canadian dollar and could be negatively impacted by currency fluctuations.
Our remote accommodation business generates revenue and incurs expenses that are denominated in the Canadian dollar. These transactions could be materially affected by currency fluctuations. Changes in currency exchange rates could adversely affect our combined results of operations or financial position. We also maintain cash balances denominated in the Canadian dollar. At December 31, 2016, we had $5.6 million of cash, in Canadian dollars, in Canadian accounts. A 10% increase in the strength of the Canadian dollar versus the U.S. dollar would have resulted in an increase in pre-tax income of approximately $0.9 million as of December 31, 2016. Conversely, a corresponding decrease in the strength of the Canadian dollar would have resulted in a comparable decrease in pre-tax income. We have not hedged our exposure to changes in foreign currency exchange rates and, as a result, could incur unanticipated translation gains and losses.
Certain of our completion and production services, particularly our hydraulic fracturing services, are substantially dependent on the availability of water. Restrictions on our ability to obtain water may have an adverse effect on our financial condition, results of operations and cash flows.
Water is an essential component of deep shale oil and natural gas production during both the drilling and hydraulic fracturing processes. Over the past several years, certain of the areas have experienced extreme drought conditions and competition for water in such shales is growing. As a result of this severe drought, some local water districts have begun restricting the use of water subject to their jurisdiction for hydraulic fracturing to protect local water supply. Our inability to obtain water to use in our operations from local sources or to effectively utilize flowback water could have an adverse effect on our financial condition, results of operations and cash flows.
We rely on a few key employees whose absence or loss could adversely affect our business.
Many key responsibilities within our business have been assigned to a small number of employees. The loss of their services could adversely affect our business. In particular, the loss of the services of our Chief Executive Officer or Chief Financial Officer, could disrupt our operations. We do not have any written employment agreement with our executives at this time. Further, we do not maintain “key person” life insurance policies on any of our employees. As a result, we are not insured against any losses resulting from the death of our key employees.
If we are unable to employ a sufficient number of skilled and qualified workers, our capacity and profitability could be diminished and our growth potential could be impaired.
The delivery of our products and services requires skilled and qualified workers with specialized skills and experience who can perform physically demanding work. As a result of the volatility of the oilfield services industry and the demanding nature of the work, workers may choose to pursue employment in fields that offer a more desirable work environment at wage rates that are competitive. Our ability to be productive and profitable will depend upon our ability to employ and retain skilled workers. In addition, our ability to expand our operations depends in part on our ability to increase the size of our skilled labor force. The demand for skilled workers is high, and the supply is limited. As a result, competition for experienced oilfield service personnel is intense, and we face significant challenges in competing for crews and management with large and well
established competitors. A significant increase in the wages paid by competing employers could result in a reduction of our skilled labor force, increases in the wage rates that we must pay, or both. If either of these events were to occur, our capacity and profitability could be diminished and our growth potential could be impaired.
Unionization efforts could increase our costs or limit our flexibility.
Presently, none of our employees work under collective bargaining agreements. Unionization efforts have been made from time to time within our industry, to varying degrees of success. Any such unionization could increase our costs or limit our flexibility.
Our operations may be limited or disrupted in certain parts of the continental U.S. and Canada during severe weather conditions, which could have a material adverse effect on our financial condition and results of operations.
We provide completion and production services and contract land and directional drilling services in the Utica, Permian Basin, Marcellus, Granite Wash, Cana Woodford and Eagle Ford resource plays located in the continental U.S. We also provide remote accommodation services in the oil sands in Alberta, Canada. We serve these markets through our facilities and service centers located in Ohio, Oklahoma, Texas, Wisconsin, Minnesota and Alberta, Canada. For the years ended December 31, 2016 and 2015, we generated approximately 84% and 72%, respectively, of our revenue from our operations in Ohio, Wisconsin, Minnesota, Pennsylvania, West Virginia and Canada where weather conditions may be severe, particularly during winter and spring months. Repercussions of severe weather conditions may include:
| |
• | curtailment of services; |
| |
• | weather-related damage to equipment resulting in suspension of operations; |
| |
• | weather-related damage to our facilities; |
| |
• | inability to deliver equipment and materials to jobsites in accordance with contract schedules; and |
Many municipalities, including those in Ohio and Wisconsin, impose bans or other restrictions on the use of roads and highways, which include weight restrictions on the paved roads that lead to our jobsites due to the muddy conditions caused by spring thaws. This can limit our access to these jobsites and our ability to service wells in these areas. These constraints and the resulting shortages or high costs could delay our operations and materially increase our operating and capital costs in those regions. Weather conditions may also affect the price of crude oil and natural gas, and related demand for our services. Any of these factors could have a material adverse effect on our financial condition and results of operations.
Concerns over general economic, business or industry conditions may have a material adverse effect on our results of operations, liquidity and financial condition.
Concerns over global economic conditions, energy costs, geopolitical issues, inflation, the availability and cost of credit and the European, Asian and the United States financial markets have contributed to increased economic uncertainty and diminished expectations for the global economy. These factors, combined with volatility in commodity prices, business and consumer confidence and unemployment rates, have precipitated an economic slowdown. Concerns about global economic growth have had a significant adverse impact on global financial markets and commodity prices. If the economic climate in the United States or abroad deteriorates, worldwide demand for petroleum products could diminish further, which could impact the price at which oil, natural gas and natural gas liquids can be sold, which could affect the ability of our customers to continue operations and ultimately adversely impact our results of operations, liquidity and financial condition.
A terrorist attack or armed conflict could harm our business
The occurrence or threat of terrorist attacks in the United States or other countries, anti-terrorist efforts and other armed conflicts involving the United States or other countries, including continued hostilities in the Middle East, may adversely affect the United States and global economies and could prevent us from meeting our financial and other obligations. If any of these events occur, the resulting political instability and societal disruption could reduce overall demand for oil and natural gas, potentially putting downward pressure on demand for our services and causing a reduction in our revenues. Oil and natural gas related facilities could be direct targets of terrorist attacks, and our operations could be adversely impacted if infrastructure integral to our customers’ operations is destroyed or damaged. Costs for insurance and other security may increase as a result of these threats, and some insurance coverage may become more difficult to obtain, if available at all.
Our operations require substantial capital and we may be unable to obtain needed capital or financing on
satisfactory terms or at all, which could limit our ability to grow.
The oilfield services industry is capital intensive. In conducting our business and operations, we have made, and expect to continue to make, substantial capital expenditures. Our total capital expenditures were approximately $11.3 million and $26.3 million for the years ended December 31, 2016 and 2015, respectively. Our capital expenditures budget for 2017 is approximately $120.0 million. Since November 2014, we have financed capital expenditures primarily with funding from cash on hand, cash generated by operations and borrowings under our revolving credit facility. We may be unable to generate sufficient cash from operations and other capital resources to maintain planned or future levels of capital expenditures which, among other things, may prevent us from acquiring new equipment or properly maintaining our existing equipment. Further, any disruptions or continuing volatility in the global financial markets may lead to an increase in interest rates or a contraction in credit availability impacting our ability to finance our operations. This could put us at a competitive disadvantage or interfere with our growth plans. Further, our actual capital expenditures for 2017 or future years could exceed our capital expenditure budget. In the event our capital expenditure requirements at any time are greater than the amount we have available, we could be required to seek additional sources of capital, which may include debt financing, joint venture partnerships, sales of assets, offerings of debt or equity securities or other means. We may not be able to obtain any such alternative source of capital. We may be required to curtail or eliminate contemplated activities. If we can obtain alternative sources of capital, the terms of such alternative may not be favorable to us. In particular, the terms of any debt financing may include covenants that significantly restrict our operations. Our inability to grow as planned may reduce our chances of maintaining and improving profitability.
The growth of our business through acquisitions may expose us to various risks, including those relating to difficulties in identifying suitable, accretive acquisition opportunities and integrating businesses, assets and personnel, as well as difficulties in obtaining financing for targeted acquisitions and the potential for increased leverage or debt service requirements.
As a component of our business strategy, we have pursued and intend to continue to pursue selected, accretive acquisitions of complementary assets, businesses and technologies. Acquisitions involve numerous risks, including:
| |
• | unanticipated costs and assumption of liabilities and exposure to unforeseen liabilities of acquired businesses, including but not limited to environmental liabilities; |
| |
• | difficulties in integrating the operations and assets of the acquired business and the acquired personnel; |
| |
• | limitations on our ability to properly assess and maintain an effective internal control environment over an acquired business, in order to comply with public reporting requirements; |
| |
• | potential losses of key employees and customers of the acquired businesses; |
| |
• | inability to commercially develop acquired technologies; |
| |
• | risks of entering markets in which we have limited prior experience; and |
| |
• | increases in our expenses and working capital requirements. |
The process of integrating an acquired business may involve unforeseen costs and delays or other operational, technical and financial difficulties and may require a disproportionate amount of management attention and financial and other resources. Our failure to achieve consolidation savings, to incorporate the acquired businesses and assets into our existing operations successfully or to minimize any unforeseen operational difficulties could have a material adverse effect on our financial condition and results of operations. Furthermore, there is intense competition for acquisition opportunities in our industry. Competition for acquisitions may increase the cost of, or cause us to refrain from, completing acquisitions. In addition, we may not have sufficient capital resources to complete additional acquisitions. Historically, we have financed capital expenditures primarily with funding from our equity investors, cash generated by operations and borrowings under our revolving credit facility. We may incur substantial indebtedness to finance future acquisitions and also may issue equity, debt or convertible securities in connection with such acquisitions. Debt service requirements could represent a significant burden on our results of operations and financial condition and the issuance of additional equity or convertible securities could be dilutive to our existing stockholders. Furthermore, we may not be able to obtain additional financing on satisfactory terms. Even if we have access to the necessary capital, we may be unable to continue to identify additional suitable acquisition opportunities, negotiate acceptable terms or successfully acquire identified targets. Our ability to grow through acquisitions and manage growth will require us to continue to invest in operational, financial and management information systems and to attract, retain, motivate and effectively manage our employees. The inability to effectively manage the integration of acquisitions could reduce our focus on subsequent acquisitions and current operations, which, in turn, could negatively impact our earnings and growth. Our financial position and results of operations may fluctuate significantly from period to period, based on whether or not significant acquisitions are completed in particular periods.
We may have difficulty managing growth in our business, which could adversely affect our financial condition and results of operations.
As a recently formed company, growth in accordance with our business plan, if achieved, could place a significant strain on our financial, technical, operational and management resources. As we expand the scope of our activities and our geographic coverage through both organic growth and acquisitions, there will be additional demands on our financial, technical, operational and management resources. The failure to continue to upgrade our technical, administrative, operating and financial control systems or the occurrences of unexpected expansion difficulties, including the failure to recruit and retain experienced managers, engineers and other professionals in the oilfield services industry, could have a material adverse effect on our business, financial condition, results of operations and our ability to successfully or timely execute our business plan.
If our intended expansion of our business is not successful, our financial condition, profitability and results of
operations could be adversely affected, and we may not achieve increases in revenue and profitability that we
hope to realize.
A key element of our business strategy involves the expansion of our services, geographic presence and customer base. These aspects of our strategy are subject to numerous risks and uncertainties, including:
| |
• | an inability to retain or hire experienced crews and other personnel; |
| |
• | a lack of customer demand for the services we intend to provide; |
| |
• | an inability to secure necessary equipment, raw materials (particularly sand and other proppants) or technology to successfully execute our expansion plans; |
| |
• | shortages of water used in our sand processing operations and our hydraulic fracturing operations; |
| |
• | unanticipated delays that could limit or defer the provision of services by us and jeopardize our relationships with existing customers and adversely affect our ability to obtain new customers for such services; and |
| |
• | competition from new and existing services providers. |
Encountering any of these or any unforeseen problems in implementing our planned expansion could have a material adverse impact on our business, financial condition, results of operations and cash flows, and could prevent us from achieving the increases in revenues and profitability that we hope to realize.
Our liquidity needs could restrict our operations and make us more vulnerable to adverse economic conditions.
Our future indebtedness, whether incurred in connection with acquisitions, operations or otherwise, may adversely affect our operations and limit our growth, and we may have difficulty making debt service payments on such indebtedness as payments become due. Our level of indebtedness may affect our operations in several ways, including the following:
| |
• | increasing our vulnerability to general adverse economic and industry conditions; |
| |
• | the covenants that are contained in the agreements governing our indebtedness could limit our ability to borrow funds, dispose of assets, pay dividends and make certain investments; |
| |
• | our debt covenants could also affect our flexibility in planning for, and reacting to, changes in the economy and in our industry; |
| |
• | any failure to comply with the financial or other covenants of our debt, including covenants that impose requirements to maintain certain financial ratios, could result in an event of default, which could result in some or all of our indebtedness becoming immediately due and payable; |
| |
• | our level of debt could impair our ability to obtain additional financing in the future for working capital, capital expenditures, acquisitions or other general corporate purposes; and |
| |
• | our business may not generate sufficient cash flow from operations to enable us to meet our obligations under our indebtedness. |
Our revolving credit facility imposes, and any of our future credit facilities may impose, restrictions on us that
may affect our ability to successfully operate our business.
Our revolving credit facility limits, and any of our future credit facilities may limit, our ability to take various actions, such as:
| |
• | incurring additional indebtedness; |
| |
• | creating certain additional liens on our assets; |
| |
• | entering into sale and leaseback transactions; |
| |
• | entering into transactions with affiliates; |
| |
• | making material changes to the type of business we conduct or our business structure; |
| |
• | disposing of assets in excess of certain permitted amounts; |
| |
• | merging or consolidating with other entities; and |
| |
• | selling all or substantially all of our assets. |
In addition, our revolving credit facility requires, and any future debt may require, us to maintain certain financial ratios and to satisfy certain financial conditions, which may require us to reduce our debt or take some other action in order to comply with each of them. These restrictions could also limit our ability to obtain future financings, make needed capital expenditures, withstand a downturn in our business or the economy in general, or otherwise conduct necessary corporate activities. We also may be prevented from taking advantage of business opportunities that arise because of the limitations imposed on us by the restrictive covenants under our revolving credit facility and any future debt agreements. If we fail to comply with the covenants in our existing revolving credit facility or any future debt agreements and such failure is not waived by the lender, a default may be declared by the lenders, which could have a material adverse effect on us.
Our revolving credit facility provides, and any future credit facilities may provide, for variable interest rates,
which may increase or decrease our interest expense.
We repaid all borrowings outstanding under our revolving credit facility with a portion of the net proceeds from the IPO. At December 31, 2016, our revolving credit facility remained undrawn. We do not currently hedge our interest rate exposure. We intend to reborrow under our revolving credit facility in the future. On October 19, 2016, immediately prior to the closing of the IPO, we had $78.1 million outstanding under this facility with weighted average interest rate of 3.51%. A 1% increase or decrease in the interest rate at that time would have increased or decreased our interest expense by approximately $0.8 million per year.
We may not be able to provide services that meet the specific needs of oil and natural gas exploration and
production companies at competitive prices.
The markets in which we operate are generally highly competitive and have relatively few barriers to entry. The principal competitive factors in our markets are price, product and service quality and availability, responsiveness, experience, technology, equipment quality and reputation for safety. We compete with large national and multi-national companies that have longer operating histories, greater financial, technical and other resources and greater name recognition than we do. Several of our competitors provide a broader array of services and have a stronger presence in more geographic markets. In addition, we compete with several smaller companies capable of competing effectively on a regional or local basis. Our competitors may be able to respond more quickly to new or emerging technologies and services and changes in customer requirements. Some contracts are awarded on a bid basis, which further increases competition based on price. Pricing is often the primary factor in determining which qualified contractor is awarded a job. The competitive environment may be further intensified by mergers and acquisitions among oil and natural gas companies or other events that have the effect of reducing the number of available customers. As a result of competition, we may lose market share or be unable to maintain or increase prices for our present services or to acquire additional business opportunities, which could have a material adverse effect on our business, financial condition, results of operations and cash flows.
In addition, some exploration and production companies have begun performing hydraulic fracturing and directional drilling on their wells using their own equipment and personnel. Any increase in the development and utilization of in-house fracturing and directional drilling capabilities by our customers could decrease the demand for our services and have a material adverse impact on our business.
Our operations are subject to hazards inherent in the oil and natural gas industry, which could expose us to
substantial liability and cause us to lose customers and substantial revenue.
Risks inherent to our industry, such as equipment defects, vehicle accidents, fires, explosions, blowouts, surface cratering, uncontrollable flows of gas or well fluids, pipe or pipeline failures, abnormally pressured formations and various environmental hazards such as oil spills and releases of, and exposure to, hazardous substances. For example, our operations are subject to risks associated with hydraulic fracturing, including any mishandling, surface spillage or potential underground migration of fracturing fluids, including chemical additives. The occurrence of any of these events could result in substantial
losses to us due to injury or loss of life, severe damage to or destruction of property, natural resources and equipment, pollution or other environmental damage, clean-up responsibilities, regulatory investigations and penalties, suspension of operations and repairs required to resume operations. The cost of managing such risks may be significant. The frequency and severity of such incidents will affect operating costs, insurability and relationships with customers, employees and regulators. In particular, our customers may elect not to purchase our services if they view our environmental or safety record as unacceptable, which could cause us to lose customers and substantial revenues. In addition, these risks may be greater for us than some of our competitors because we sometimes acquire companies that may not have allocated significant resources and management focus to safety and environmental matters and may have a poor environmental and safety record and associated possible exposure. Our insurance may not be adequate to cover all losses or liabilities we may suffer. Also, insurance may no longer be available to us or, if it is, its availability may be at premium levels that do not justify its purchase. The occurrence of a significant uninsured claim, a claim in excess of the insurance coverage limits maintained by us or a claim at a time when we are not able to obtain liability insurance could have a material adverse effect on our ability to conduct normal business operations and on our financial condition, results of operations and cash flows. In addition, we may not be able to secure additional insurance or bonding that might be required by new governmental regulations. This may cause us to restrict our operations, which might severely impact our financial position.
Since hydraulic fracturing activities are part of our operations, they are covered by our insurance against claims made for bodily injury, property damage and clean-up costs stemming from a sudden and accidental pollution event. However, we may not have coverage if we are unaware of the pollution event and unable to report the “occurrence” to our insurance company within the time frame required under our insurance policy. We have no coverage for gradual, long-term pollution events. In addition, these policies do not provide coverage for all liabilities, and the insurance coverage may not be adequate to cover claims that may arise, or we may not be able to maintain adequate insurance at rates we consider reasonable. A loss not fully covered by insurance could have a material adverse effect on our financial position, results of operations and cash flows.
We are subject to extensive environmental, health and safety laws and regulations that may subject us to substantial liability or require us to take actions that will adversely affect our results of operations.
Our business is significantly affected by stringent and complex federal, state and local laws and regulations governing the discharge of substances into the environment or otherwise relating to environmental protection and health and safety matters. As part of our business, we handle, transport and dispose of a variety of fluids and substances, including hydraulic fracturing fluids which can contain hydrochloric acid and certain petrochemicals. This activity poses some risks of environmental liability, including leakage of hazardous substances from the wells to surface and subsurface soils, surface water or groundwater. We also handle, transport and store these substances. The handling, transportation, storage and disposal of these fluids are regulated by a number of laws, including: the Resource Conservation and Recovery Act; the Comprehensive Environmental Response, Compensation, and Liability Act; the Clean Water Act; the Safe Drinking Water Act; and other federal and state laws and regulations promulgated thereunder. The cost of compliance with these laws can be significant. Failure to properly handle, transport or dispose of these materials or otherwise conduct our operations in accordance with these and other environmental laws could expose us to substantial liability for administrative, civil and criminal penalties, cleanup and site restoration costs and liability associated with releases of such materials, damages to natural resources and other damages, as well as potentially impair our ability to conduct our operations. We could be exposed to liability for cleanup costs, natural resource damages and other damages under these and other environmental laws. Such liability is commonly on a strict, joint and several liability basis, without regard to fault. Liability may be imposed as a result of our conduct that was lawful at the time it occurred or the conduct of, or conditions caused by, prior operators or other third parties. Environmental laws and regulations have changed in the past, and they are likely to change in the future. If existing environmental requirements or enforcement policies change and become more stringent, we may be required to make significant unanticipated capital and operating expenditures.
The adoption of climate change legislation or regulations restricting emissions of greenhouse gases could
result in increased operating costs and reduced demand for oil and natural gas.
In recent years, federal, state and local governments have taken steps to reduce emissions of greenhouse gases. The EPA has finalized a series of greenhouse gas monitoring, reporting and emissions control rules for the oil and natural gas industry, and the U.S. Congress has, from time to time, considered adopting legislation to reduce emissions. Almost one-half of the states have already taken measures to reduce emissions of greenhouse gases primarily through the development of greenhouse gas emission inventories and/or regional greenhouse gas cap-and-trade programs. In December 2015, the United States participated in the 21st Conference of the Parties of the United Nations Framework Convention on Climate Change in Paris, France. The resulting Paris Agreement calls for the parties to undertake “ambitious efforts” to limit the average global temperature, and to conserve and enhance sinks and reservoirs of greenhouse gases. The Agreement, which went into effect on November 6, 2016, establishes a framework for the parties to cooperate and report actions to reduce greenhouse gas emissions.
Also, on June 29, 2016, the leaders of the United States, Canada and Mexico announced an Action Plan to, among other things, boost clean energy, improve energy efficiency, and reduce GHG emissions. The Action Plan specifically calls for a reduction in methane emissions from the oil and gas sector by 40 to 45 percent by 2025. Restrictions on emissions of methane or carbon dioxide that may be imposed could adversely affect the oil and natural gas industry by reducing demand for hydrocarbons and by making it more expensive to develop and produce hydrocarbons, either of which could have a material adverse effect on future demand for our services. At this time, it is not possible to accurately estimate how potential future laws or regulations addressing greenhouse gas emissions would impact our business. It also remains unclear whether and how the results of the 2016 U.S. election could impact the regulation of GHG emissions at the federal and state level.
In addition, claims have been made against certain energy companies alleging that greenhouse gas emissions from oil and natural gas operations constitute a public nuisance under federal and/or state common law. As a result, private individuals may seek to enforce environmental laws and regulations against certain energy companies and could allege personal injury or property damages. While our business is not a party to any such litigation, we could be named in actions making similar allegations. An unfavorable ruling in any such case could significantly impact our operations and could have an adverse impact on our financial condition. Moreover, climate change may cause more extreme weather conditions such as more intense hurricanes, thunderstorms, tornadoes and snow or ice storms, as well as rising sea levels and increased volatility in seasonal temperatures. Extreme weather conditions can interfere with our services and increase our costs, and damage resulting from extreme weather may not be fully insured. However, at this time, we are unable to determine the extent to which climate change may lead to increased storm or weather hazards affecting our operations.
Federal and state legislative and regulatory initiatives relating to hydraulic fracturing could result in increased costs and additional operating restrictions or delays.
Our business is dependent on our ability to conduct hydraulic fracturing and horizontal drilling activities. Hydraulic fracturing is an important and common practice that is used to stimulate production of hydrocarbons, particularly natural gas, from tight formations, including shales. The process, which involves the injection of water, sand and chemicals (also called “proppants”) under pressure into formations to fracture the surrounding rock and stimulate production, is typically regulated by state oil and natural gas commissions. However, federal agencies have asserted regulatory authority over certain aspects of the process. For example, on December 13, 2016, the EPA released a study examining the potential for hydraulic fracturing activities to impact drinking water resources, finding that, under some circumstances, the use of water in hydraulic fracturing activities can impact drinking water resources. Also, on June 28, 2016, the EPA published a final rule prohibiting the discharge of wastewater from onshore unconventional oil and natural gas extraction facilities to publicly owned wastewater treatment plans. The EPA is also conducting a study of private wastewater treatment facilities (also known as centralized waste treatment, or CWT, facilities) accepting oil and natural gas extraction wastewater. The EPA is collecting data and information related to the extent to which CWT facilities accept such wastewater, available treatment technologies (and their associated costs), discharge characteristics, financial characteristics of CWT facilities and the environmental impacts of discharges from CWT facilities. Furthermore, legislation to amend the Safe Drinking Water Act, or SDWA, to repeal the exemption for hydraulic fracturing (except when diesel fuels are used) from the definition of “underground injection” and require federal permitting and regulatory control of hydraulic fracturing, as well as legislative proposals to require disclosure of the chemical constituents of the fluids used in the fracturing process, were proposed in recent sessions of Congress.
On August 16, 2012, the EPA published final regulations under the federal Clean Air Act that establish new air emission controls for oil and natural gas production and natural gas processing operations. Specifically, the EPA’s rule package includes New Source Performance Standards to address emissions of sulfur dioxide and volatile organic compounds, or VOCs, and a separate set of emission standards to address hazardous air pollutants frequently associated with oil and natural gas production and processing activities. The final rule seeks to achieve a 95% reduction in VOCs emitted by requiring the use of reduced emission completions or “green completions” on all hydraulically-fractured wells constructed or refractured after January 1, 2015. The rules also establish specific new requirements regarding emissions from compressors, controllers, dehydrators, storage tanks and other production equipment. These rules required a number of modifications to our operations, including the installation of new equipment to control emissions. The EPA received numerous requests for reconsideration of these rules from both industry and the environmental community, and court challenges to the rules were also filed. In response, the EPA has issued, and will likely continue to issue, revised rules responsive to some of the requests for reconsideration. In particular, on May 12, 2016, the EPA amended the New Source Performance Standards to impose new standards for methane and VOC emissions for certain new, modified, and reconstructed equipment, processes, and activities across the oil and natural gas sector. On the same day, the EPA finalized a plan to implement its minor new source review program on Indian lands for oil and natural gas production, and it issued for public comment an information request that will require companies to provide extensive information instrumental for the development of regulations to reduce methane emissions from existing oil and gas sources. These standards, as well as any future laws and their implementing regulations, may require us to obtain pre-approval
for the expansion or modification of existing facilities or the construction of new facilities expected to produce air emissions, impose stringent air permit requirements, or mandate the use of specific equipment or technologies to control emissions.
There are certain governmental reviews either underway or being proposed that focus on the environmental aspects of hydraulic fracturing practices. The EPA continues to evaluate the potential impacts of hydraulic fracturing on drinking water resources and the induced seismic activity from disposal wells and has recommended strategies for managing and minimizing the potential for significant injection-induced seismic events. Other governmental agencies, including the U.S. Department of Energy, the U.S. Geological Survey and the U.S. Government Accountability Office, have evaluated or are evaluating various other aspects of hydraulic fracturing. These ongoing or proposed studies, depending on their degree of pursuit and whether any meaningful results are obtained, could spur initiatives to further regulate hydraulic fracturing, and could ultimately make it more difficult or costly to perform fracturing and increase the costs of compliance and doing business for our customers.
Several states, including Texas and Ohio, have adopted or are considering adopting regulations that could restrict or prohibit hydraulic fracturing in certain circumstances, impose more stringent operating standards and/or require the disclosure of the composition of hydraulic fracturing fluids. Any increased regulation of hydraulic fracturing could reduce the demand for our services and materially and adversely affect our revenues and results of operations.
There has been increasing public controversy regarding hydraulic fracturing with regard to the use of fracturing fluids, induced seismic activity, impacts on drinking water supplies, use of water and the potential for impacts to surface water, groundwater and the environment generally. A number of lawsuits and enforcement actions have been initiated across the country implicating hydraulic fracturing practices. If new laws or regulations are adopted that significantly restrict hydraulic fracturing, such laws could make it more difficult or costly for us to perform fracturing to stimulate production from tight formations as well as make it easier for third parties opposing the hydraulic fracturing process to initiate legal proceedings based on allegations that specific chemicals used in the fracturing process could adversely affect groundwater. In addition, if hydraulic fracturing is further regulated at the federal, state or local level, our customers’ fracturing activities could become subject to additional permitting and financial assurance requirements, more stringent construction specifications, increased monitoring, reporting and recordkeeping obligations, plugging and abandonment requirements and also to attendant permitting delays and potential increases in costs. Such legislative or regulatory changes could cause us or our customers to incur substantial compliance costs, and compliance or the consequences of any failure to comply by us could have a material adverse effect on our financial condition and results of operations. At this time, it is not possible to estimate the impact on our business of newly enacted or potential federal, state or local laws governing hydraulic fracturing.
Penalties, fines or sanctions that may be imposed by the U.S. Mine Safety and Health Administration could have a material adverse effect on our proppant production and sales business and our overall financial condition, results of operations and cash flows.
The U.S. Mine Safety and Health Administration, or MSHA, has primary regulatory jurisdiction over commercial silica operations, including quarries, surface mines, underground mines, and industrial mineral process facilities. While we do not directly conduct any mining operations, we are dependent on several regulated mines for the supply of natural sand used in our proppant production business. In addition, MSHA representatives perform at least two annual inspections of our production facilities to ensure employee and general site safety. As a result of these and future inspections and alleged violations and potential violations, we and our suppliers could be subject to material fines, penalties or sanctions. Any of our production facilities or our suppliers’ mines could be subject to a temporary or extended shut down as a result of an alleged MSHA violation. Any such penalties, fines or sanctions could have a material adverse effect on our proppant production and sales business and our overall financial condition, results of operations and cash flows.
Increasing trucking regulations may increase our costs and negatively impact our results of operations.
In connection with our business operations, including the transportation and relocation of our oilfield service equipment and shipment of frac sand, we operate trucks and other heavy equipment. As such, we operate as a motor carrier in providing certain of our services and therefore are subject to regulation by the United States Department of Transportation and by various state agencies. These regulatory authorities exercise broad powers, governing activities such as the authorization to engage in motor carrier operations, driver licensing, insurance requirements, financial reporting and review of certain mergers, consolidations and acquisitions, and transportation of hazardous materials (HAZMAT). Our trucking operations are subject to possible regulatory and legislative changes that may increase our costs. Some of these possible changes include increasingly stringent environmental regulations, changes in the hours of service regulations which govern the amount of time a driver may drive or work in any specific period, onboard black box recorder device requirements or limits on vehicle weight and size. Interstate motor carrier operations are subject to safety requirements prescribed by the United States Department of Transportation. To a large degree, intrastate motor carrier operations are subject to state safety regulations that mirror federal
regulations. Matters such as the weight and dimensions of equipment are also subject to federal and state regulations. From time to time, various legislative proposals are introduced, including proposals to increase federal, state, or local taxes, including taxes on motor fuels, which may increase our costs or adversely impact the recruitment of drivers. We cannot predict whether, or in what form, any increase in such taxes applicable to us will be enacted.
Certain motor vehicle operators require registration with the Department of Transportation. This registration requires an acceptable operating record. The Department of Transportation periodically conducts compliance reviews and may revoke registration privileges based on certain safety performance criteria that could result in a suspension of operations.
Restrictions on drilling activities intended to protect certain species of wildlife may adversely affect our ability
to conduct drilling activities in some of the areas where we operate.
Oil and natural gas operations in our operating areas can be adversely affected by seasonal or permanent restrictions on drilling activities designed to protect various wildlife, which may limit our ability to operate in protected areas. Permanent restrictions imposed to protect endangered species could prohibit drilling in certain areas or require the implementation of expensive mitigation measures. Additionally, the designation of previously unprotected species as threatened or endangered in areas where we operate could result in increased costs arising from species protection measures. Restrictions on oil and natural gas operations to protect wildlife could reduce demand for our services.
Conservation measures and technological advances could reduce demand for oil and natural gas and our
services.
Fuel conservation measures, alternative fuel requirements, increasing consumer demand for alternatives to oil and natural gas, technological advances in fuel economy and energy generation devices could reduce demand for oil and natural gas, resulting in reduced demand for oilfield services. The impact of the changing demand for oil and natural gas services and products may have a material adverse effect on our business, financial condition, results of operations and cash flows.
Losses and liabilities from uninsured or underinsured drilling and operating activities could have a material
adverse effect on our financial condition and operations.
The operational insurance coverage we maintain for our business may not fully insure us against all risks, either because insurance is not available or because of the high premium costs relative to perceived risk. Further, any insurance obtained by us may not be adequate to cover any losses or liabilities and this insurance may not continue to be available at all or on terms which are acceptable to us. Insurance rates have in the past been subject to wide fluctuation and changes in coverage could result in less coverage, increases in cost or higher deductibles and retentions. See “Business—Operating Risks and Insurance” for additional information on our insurance policies. Liabilities for which we are not insured, or which exceed the policy limits of our applicable insurance, could have a material adverse effect on our business activities, financial condition and results of operations.
We may be subject to claims for personal injury and property damage, which could materially adversely affect our financial condition and results of operations.
We operate with most of our customers under master service agreements, or MSAs. We endeavor to allocate potential liabilities and risks between the parties in the MSAs. Generally, under our MSAs, including those relating to our hydraulic fracturing services, we assume responsibility for, including control and removal of, pollution or contamination which originates above surface and originates from our equipment or services. Our customer assumes responsibility for, including control and removal of, all other pollution or contamination which may occur during operations, including that which may result from seepage or any other uncontrolled flow of drilling fluids. We may have liability in such cases if we are negligent or commit willful acts. Generally, our customers also agree to indemnify us against claims arising from their employees’ personal injury or death to the extent that, in the case of our hydraulic fracturing operations, their employees are injured or their properties are damaged by such operations, unless resulting from our gross negligence or willful misconduct. Similarly, we generally agree to indemnify our customers for liabilities arising from personal injury to or death of any of our employees, unless resulting from gross negligence or willful misconduct of the customer. In addition, our customers generally agree to indemnify us for loss or destruction of customer-owned property or equipment and in turn, we agree to indemnify our customers for loss or destruction of property or equipment we own. Losses due to catastrophic events, such as blowouts, are generally the responsibility of the customer. However, despite this general allocation of risk, we might not succeed in enforcing such contractual allocation, might incur an unforeseen liability falling outside the scope of such allocation or may be required to enter into an MSA with terms that vary from the above allocations of risk. As a result, we may incur substantial losses which could materially and adversely affect our financial condition and results of operation.
Loss of our information and computer systems could adversely affect our business.
We are heavily dependent on our information systems and computer based programs, including our well operations information and accounting data. If any of such programs or systems were to fail or create erroneous information in our hardware or software network infrastructure, whether due to cyber attack or otherwise, possible consequences include our loss of communication links and inability to automatically process commercial transactions or engage in similar automated or computerized business activities. Any such consequence could have a material adverse effect on our business.
We are subject to cyber security risks. A cyber incident could occur and result in information theft, data corruption, operational disruption and/or financial loss.
The oil and natural gas industry has become increasingly dependent on digital technologies to conduct certain processing activities. For example, we depend on digital technologies to perform many of our services and process and record financial and operating data. At the same time, cyber incidents, including deliberate attacks or unintentional events, have increased. The U.S. government has issued public warnings that indicate that energy assets might be specific targets of cyber security threats. Our technologies, systems and networks, and those of our vendors, suppliers and other business partners, may become the target of cyberattacks or information security breaches that could result in the unauthorized release, gathering, monitoring, misuse, loss or destruction of proprietary and other information, or other disruption of our business operations. In addition, certain cyber incidents, such as surveillance, may remain undetected for an extended period. Our systems and insurance coverage for protecting against cyber security risks may not be sufficient. As cyber incidents continue to evolve, we may be required to expend additional resources to continue to modify or enhance our protective measures or to investigate and remediate any vulnerability to cyber incidents. Our insurance coverage for cyberattacks may not be sufficient to cover all the losses we may experience as a result of such cyberattacks.
Risks Inherent to Our Common Stock
Our two largest stockholders control a significant percentage of our common stock, and their interests may conflict with those of our other stockholders.
Wexford, through its affiliate Mammoth Energy Holdings LLC, and Gulfport beneficially own approximately 54.5% and 24.2%, respectively, of our outstanding common stock. As a result, Wexford alone controls, and Gulfport can exercise significant influence, over matters requiring stockholder approval, including the election of directors, changes to our organizational documents and significant corporate transactions. Further, two individuals who serve as our directors are affiliates of Wexford or Gulfport. This concentration of ownership and relationships with Wexford and Gulfport make it unlikely that any other holder or group of holders of our common stock will be able to affect the way we are managed or the direction of our business. In addition, we have engaged, and expect to continue to engage, in related party transactions involving Wexford and Gulfport, and certain companies they control. See Note 15 to our consolidated financial statements included elsewhere in this annual report. The interests of Wexford and Gulfport with respect to matters potentially or actually involving or affecting us, such as services provided, future acquisitions, financings and other corporate opportunities, and attempts to acquire us, may conflict with the interests of our other stockholders. This concentrated ownership will make it impossible for another company to acquire us and for you to receive any related takeover premium for your shares unless these stockholders approve the acquisition.
A significant reduction by Wexford or Gulfport of their ownership interests in us could adversely affect us.
We believe that Wexford’s and Gulfport’s substantial ownership interests in us provides them with an economic incentive to assist us to be successful. Upon the expiration or earlier waiver of the lock-up restrictions on transfers or sales of our securities agreed to by Wexford and Gulfport in connection with the IPO, neither Wexford nor Gulfport will be subject to any obligation to maintain its ownership interest in us and may elect at any time thereafter to sell all or a substantial portion of or otherwise reduce its ownership interest in us. If Wexford or Gulfport sells all or a substantial portion of its ownership interest in us, it may have less incentive to assist in our success and its affiliates that serve as members of our board of directors may resign. Such actions could adversely affect our ability to successfully implement our business strategies which could adversely affect our cash flows or results of operations.
We will incur increased costs as a result of being a public company, which may significantly affect our
financial condition.
As a public company, we will incur significant legal, accounting and other expenses that we did not incur as a private company. We will incur costs associated with our public company reporting requirements. We also anticipate that we will incur
costs associated with corporate governance requirements, including requirements under the Sarbanes-Oxley Act of 2002 and the Dodd-Frank Act of 2010, as well as rules implemented by the SEC, The NASDAQ Global Select Market and the Financial Industry Regulatory Authority. We expect these rules and regulations to increase our legal and financial compliance costs and to make some activities more time-consuming and costly, particularly after we are no longer an “emerging growth company.” For example, as a result of becoming a publicly traded company, we are required to have at least three independent directors and adopt policies regarding internal controls and disclosure controls and procedures, including the preparation of reports on internal control over financial reporting. We also expect these rules and regulations may make it more difficult and more expensive for us to obtain director and officer liability insurance and we may be required to accept reduced policy limits and coverage or incur substantially higher costs to obtain the same or similar coverage. As a result, it may be more difficult for us to attract and retain qualified individuals to serve on our board of directors or as executive officers. We are currently evaluating these rules, and we cannot predict or estimate the amount of additional costs we may incur or the timing of such costs. However, for as long as we remain an “emerging growth company” as defined in the Jumpstart Our Business Startups Act enacted by the U.S. Congress in April 2012, or the JOBS Act, we intend to take advantage of certain exemptions from various reporting requirements that are applicable to other public companies that are not “emerging growth companies” including, but not limited to, not being required to comply with the auditor attestation requirements of Section 404 of the Sarbanes-Oxley Act, reduced disclosure obligations regarding executive compensation in our periodic reports and proxy statements, and exemptions from the requirements of holding a nonbinding advisory vote on executive compensation and stockholder approval of any golden parachute payments not previously approved. We intend to take advantage of these reporting exemptions until we are no longer an “emerging growth company.” We could be an “emerging growth company” for up to five years following the completion of our initial public offering, although, if we have more than $1.0 billion in annual revenue, if the market value of our common stock that is held by non-affiliates exceeds $700 million as of June 30 of any year, or we issue more than $1.0 billion of non-convertible debt over a three-year period before the end of that five-year period, we would cease to be an “emerging growth company” as of the following December 31st. We estimate that we will incur approximately $2.5 million of incremental costs per year associated with being a publicly traded company; however, it is possible that our actual incremental costs of being a publicly traded company will be higher than we currently estimate. After we are no longer an “emerging growth company,” we expect to incur significant additional expenses and devote substantial management effort toward ensuring compliance with those requirements applicable to companies that are not “emerging growth companies,” including Section 404 of the Sarbanes-Oxley Act. See “—Risks Related to Our Business and the Oil and Natural Gas Industry—We will be subject to certain requirements of Section 404 of the Sarbanes-Oxley Act. If we are unable to timely comply with Section 404 or if the costs related to compliance are significant, our profitability, stock price, results of operations and financial condition could be materially adversely affected.”
For so long as we are an “emerging growth company” we will not be required to comply with certain disclosure requirements that are applicable to other public companies and we cannot be certain if the reduced disclosure requirements applicable to emerging growth companies will make our common stock less attractive to investors.
We are an “emerging growth company,” as defined in the JOBS Act, and we may take advantage of certain exemptions from various reporting requirements that are applicable to other public companies, including, but not limited to, not being required to comply with the auditor attestation requirements of Section 404 of the Sarbanes-Oxley Act, reduced disclosure obligations regarding executive compensation in our periodic reports and proxy statements, and exemptions from the requirements of holding a nonbinding advisory vote on executive compensation and stockholder approval of any golden parachute payments not previously approved. We cannot predict if investors will find our common stock less attractive because we will rely on these exemptions. If some investors find our common stock less attractive as a result, there may be a less active trading market for our common stock and our common stock price may be more volatile. Under the JOBS Act, “emerging growth companies” can delay adopting new or revised accounting standards until such time as those standards apply to private companies. Prior to the completion of our IPO, we irrevocably elected not to avail ourselves to this exemption from new or revised accounting standards and, therefore, we will be subject to the same new or revised accounting standards as other public companies that are not “emerging growth companies.”
We will be subject to certain requirements of Section 404 of the Sarbanes-Oxley Act. If we are unable to timely comply with Section 404 or if the costs related to compliance are significant, our profitability, stock price, results of operations and financial condition could be materially adversely affected.
We will be required to comply with certain provisions of Section 404 of the Sarbanes-Oxley Act of 2002. Section 404 requires that we document and test our internal control over financial reporting and issue management’s assessment of our internal control over financial reporting. This section also requires that our independent registered public accounting firm opine on those internal controls upon becoming an accelerated filer, as defined in the SEC rules, or otherwise ceasing to qualify for an exemption from the requirement to provide auditors’ attestation on internal controls afforded to emerging growth companies under the JOBS Act. We are currently evaluating our existing controls against the standards adopted by the Committee of
Sponsoring Organizations of the Treadway Commission. During the course of our ongoing evaluation and integration of the internal control over financial reporting, we may identify areas requiring improvement, and we may have to design enhanced processes and controls to address issues identified through this review. For example, we anticipate the need to hire additional administrative and accounting personnel to conduct our financial reporting. We believe that the out-of-pocket costs, the diversion of management’s attention from running the day-to-day operations and operational changes caused by the need to comply with the requirements of Section 404 of the Sarbanes-Oxley Act could be significant. If the time and costs associated with such compliance exceed our current expectations and our results of operations could be adversely affected.
We cannot be certain at this time that we will be able to successfully complete the procedures, certification and attestation requirements of Section 404 or that we or our auditors will not identify material weaknesses in internal control over financial reporting. If we fail to comply with the requirements of Section 404 or if we or our auditors identify and report such material weaknesses, the accuracy and timeliness of the filing of our annual and quarterly reports may be materially adversely affected and could cause investors to lose confidence in our reported financial information, which could have a negative effect on the trading price of our common stock. In addition, a material weakness in the effectiveness of our internal control over financial reporting could result in an increased chance of fraud and the loss of customers, reduce our ability to obtain financing and require additional expenditures to comply with these requirements, each of which could have a material adverse effect on our business, results of operations and financial condition.
Since we are a “controlled company” for purposes of The NASDAQ Global Select Market’s corporate governance requirements, our stockholders will not have, and may never have, the protections that these corporate governance requirements are intended to provide.
Since we are a “controlled company” for purposes of The NASDAQ Global Select Market’s corporate governance requirements, we are not required to comply with the provisions requiring that a majority of our directors be independent, the compensation of our executives be determined by independent directors or nominees for election to our board of directors be selected by independent directors. If we choose to take advantage of any or all of these exemptions, our stockholders may not have the protections that these rules are intended to provide.
The corporate opportunity provisions in our certificate of incorporation could enable Wexford, Gulfport or other affiliates of ours to benefit from corporate opportunities that might otherwise be available to us.
Subject to the limitations of applicable law, our certificate of incorporation, among other things:
| |
• | permits us to enter into transactions with entities in which one or more of our officers or directors are financially or otherwise interested; |
| |
• | permits any of our stockholders, officers or directors to conduct business that competes with us and to make investments in any kind of property in which we may make investments; and |
| |
• | provides that if any director or officer of one of our affiliates who is also one of our officers or directors becomes aware of a potential business opportunity, transaction or other matter (other than one expressly offered to that director or officer in writing solely in his or her capacity as our director or officer), that director or officer will have no duty to communicate or offer that opportunity to us, and will be permitted to communicate or offer that opportunity to such affiliates and that director or officer will not be deemed to have (i) acted in a manner inconsistent with his or her fiduciary or other duties to us regarding the opportunity or (ii) acted in bad faith or in a manner inconsistent with our best interests. |
These provisions create the possibility that a corporate opportunity that would otherwise be available to us may
be used for the benefit of one of our affiliates.
We have engaged in transactions with our affiliates and expect to do so in the future. The terms of such transactions and the resolution of any conflicts that may arise may not always be in our or our common stockholders’ best interests.
We have engaged in transactions and expect to continue to engage in transactions with affiliated companies. As described in Note 15 to our consolidated financial statements included elsewhere in this annual report these include, among others, agreements to provide our services and frac sand products to our affiliates and agreements pursuant to which our affiliates provide or will provide us with certain services, including administrative and advisory services and office space. Each of these entities is either controlled by or affiliated with Wexford or Gulfport, as the case may be, and the resolution of any conflicts that may arise in connection with such related party transactions, including pricing, duration or other terms of service, may not always be in our or our stockholders’ best interests because Wexford and/or Gulfport may have the ability to influence the outcome of these conflicts. For a discussion of potential conflicts, see “—Risks Inherent to Our Common Stock—Our two
largest stockholders control a significant percentage of our common stock, and their interests may conflict with those of our other stockholders.”
Prior to the IPO, there was no public market for our common stock and if the price of our common stock fluctuates significantly, your investment could lose value.
Prior to the completion of the IPO in October 2016, there was no public market for our common stock. Although our common stock is listed on The NASDAQ Global Select Market, an active public market for our common stock may not be maintained or our common stock may trade in the public market below the IPO price. If an active public market for our common stock is not maintained, the trading price and liquidity of our common stock will be materially and adversely affected. If there is a thin trading market or “float” for our common stock, the market price for our common stock may fluctuate significantly more than the stock market as a whole. Without a large float, our common stock is less liquid than the securities of companies with broader public ownership and, as a result, the trading prices of our common stock may be more volatile. In addition, in the absence of an active public trading market, investors may be unable to liquidate their investment in us. In addition, the stock market is subject to significant price and volume fluctuations, and the price of our common stock could fluctuate widely in response to several factors, including:
| |
• | our quarterly or annual operating results; |
| |
• | changes in our earnings estimates; |
| |
• | investment recommendations by securities analysts following our business or our industry; |
| |
• | additions or departures of key personnel; |
| |
• | changes in the business, earnings estimates or market perceptions of our competitors; |
| |
• | our failure to achieve operating results consistent with securities analysts’ projections; |
| |
• | changes in industry, general market or economic conditions; and |
| |
• | announcements of legislative or regulatory change. |
The stock market has experienced extreme price and volume fluctuations in recent years that have significantly affected the quoted prices of the securities of many companies, including companies in our industry. The changes often appear to occur without regard to specific operating performance. The price of our common stock could fluctuate based upon factors that have little or nothing to do with our company and these fluctuations could materially reduce the price for our common stock.
Wexford and Gulfport beneficially own a substantial number of our common stock and may sell such common stock in the public or private markets. Future sales of these shares of common stock or substantial amounts of our common stock, or the perception that such sales may occur, could adversely affect the prevailing market price of our common stock.
Wexford and Gulfport beneficially own 20,443,903 and 9,073,750 shares of our common stock, respectively. Future sales of these shares of common stock or substantial amounts of our common stock, or the perception that such sales may occur, could adversely affect the prevailing market price of our common stock. In addition, the sale of these shares could impair our ability to raise capital through the sale of additional common or preferred stock. As of December 31, 2016, we had 37,500,000 shares of common stock outstanding, excluding any equity awards granted under our equity incentive plan. The 7,750,000 shares of common stock sold in the IPO, except for any our common stock purchased by our affiliates, are freely tradable.
Mammoth Holdings, Gulfport and Rhino, and our directors and executive officers are subject to agreements that limit their ability to sell our common stock held by them. These holders cannot sell or otherwise dispose of any shares of our common stock for a period of at least 180 days after the date of the IPO, which period may be extended under limited circumstances, without the prior written approval of the representative of the underwriters. However, these lock-up agreements are subject to certain specific exceptions. In the event that one or more of our stockholders sells a substantial amount of our common stock in the public market, or the market perceives that such sales may occur, the price of our stock could decline.
If securities or industry analysts do not publish research or reports about our business, if they adversely change their recommendations regarding our stock or if our operating results do not meet their expectations, the price of our stock could decline.
The trading market for our common stock will be influenced by the research and reports that industry or securities analysts publish about us or our business. If one or more of these analysts cease coverage of our company or fail to publish reports on us regularly, we could lose visibility in the financial markets, which in turn could cause our stock price or trading
volume to decline. Moreover, if one or more of the analysts who cover our company downgrades our stock or if our operating results do not meet their expectations, our stock price could decline.
We may issue preferred stock whose terms could adversely affect the voting power or value of our common stock.
Our certificate of incorporation authorizes us to issue, without the approval of our stockholders, one or more classes or series of preferred stock having such designations, preferences, limitations and relative rights, including preferences over our common stock respecting dividends and distributions, as our board of directors may determine. The terms of one or more classes or series of preferred stock could adversely impact the voting power or value of our common stock. For example, we might grant holders of preferred stock the right to elect some number of our directors in all events or on the happening of specified events or the right to veto specified transactions. Similarly, the repurchase or redemption rights or liquidation preferences we might assign to holders of preferred stock could affect the residual value of the common stock.
Provisions in our certificate of incorporation and bylaws and Delaware law make it more difficult to effect a change in control of the company, which could adversely affect the price of our common stock.
The existence of some provisions in our certificate of incorporation and bylaws and Delaware corporate law could delay or prevent a change in control of our company, even if that change would be beneficial to our stockholders. Our certificate of incorporation and bylaws contain provisions that may make acquiring control of our company difficult, including:
| |
• | provisions regulating the ability of our stockholders to nominate directors for election or to bring matters for action at annual meetings of our stockholders; |
| |
• | limitations on the ability of our stockholders to call a special meeting and act by written consent; |
| |
• | the ability of our board of directors to adopt, amend or repeal bylaws, and the requirement that the affirmative vote of holders representing at least 66 2/3% of the voting power of all outstanding shares of capital stock be obtained for stockholders to amend our bylaws; |
| |
• | the requirement that the affirmative vote of holders representing at least 66 2/3% of the voting power of all outstanding shares of capital stock be obtained to remove directors; |
| |
• | the requirement that the affirmative vote of holders representing at least 66 2/3% of the voting power of all outstanding shares of capital stock be obtained to amend our certificate of incorporation; and |
| |
• | the authorization given to our board of directors to issue and set the terms of preferred stock without the approval of our stockholders. |
These provisions also could discourage proxy contests and make it more difficult for you and other stockholders to elect directors and take other corporate actions. As a result, these provisions could make it more difficult for a third party to acquire us, even if doing so would benefit our stockholders, which may limit the price that investors are willing to pay in the future for shares of our common stock.
Our certificate of incorporation designates courts in the State of Delaware as the sole and exclusive forum for certain types of actions and proceedings that may be initiated by our stockholders, which could limit our stockholders’ ability to obtain a favorable judicial forum for disputes with us or our directors, officers or other employees.
Our certificate of incorporation provides that, subject to limited exceptions, the Court of Chancery of the State of Delaware will be the sole and exclusive forum for:
| |
• | Any derivative action or proceeding brought on our behalf; |
| |
• | Any action asserting a claim of breach of fiduciary duty owed by any of our directors, officers or other employees to us or our stockholders; |
| |
• | Any action asserting a claim against us arising pursuant to any provision of the Delaware General Corporation Law; or |
| |
• | Any other action asserting a claim against us that is governed by the internal affairs doctrine. |
In addition, our certificate of incorporation provides that if any action specified above (each is referred to herein as a covered proceeding), is filed in a court other than the specified Delaware courts without the approval of our board of directors (each is referred to herein as a foreign action), the claiming party will be deemed to have consented to (i) the personal jurisdiction of the specified Delaware courts in connection with any action brought in any such courts to enforce the exclusive forum provision described above and (ii) having service of process made upon such claiming party in any such enforcement action by service upon such claiming party’s counsel in the foreign action as agent for such claiming party. These provisions may limit a stockholder’s ability to bring a claim in a judicial forum that it finds favorable for disputes with us or our directors, officers or other employees, which may discourage such lawsuits against us and our directors, officers and employees.
Alternatively, if a court were to find these provisions of our certificate of incorporation inapplicable to, or unenforceable in respect of, one or more of the covered proceedings, we may incur additional costs associated with resolving such matters in other jurisdictions, which could adversely affect our business and financial condition.
We do not intend to pay cash dividends on our common stock in the foreseeable future, and therefore only appreciation of the price of our common stock will provide a return to our stockholders.
We currently anticipate that we will retain all future earnings, if any, to finance the growth and development of our business. We do not intend to pay cash dividends in the foreseeable future. Any future determination as to the declaration and payment of cash dividends will be at the discretion of our board of directors and will depend upon our financial condition, results of operations, contractual restrictions, capital requirements, business prospects and other factors deemed relevant by our board of directors. In addition, the terms of our revolving credit facility prohibit us from paying dividends and making other distributions. As a result, only appreciation of the price of our common stock, which may not occur, will provide a return to our stockholders.
Item 1B. Unresolved Staff Comments
None.
Item 2. Properties
Our corporate headquarters are located at 4727 Gaillardia Parkway, Suite 200, Oklahoma City, Oklahoma 73142. We currently own eight properties, three located in Ohio, two located in Wisconsin, one located in Texas and two located in Canada, which are used for field offices, yards, production plants or housing. In addition to our headquarters, we also lease fourteen properties that are used for field offices, yards or transloading facilities for frac sand. We lease eleven of these properties from third parties and three of these properties from related parties.
We believe that our facilities are adequate for our current operations.
Item 3. Legal Proceedings
The Company is routinely involved in state and local tax audits. During 2015, the State of Ohio assessed taxes on the purchase of equipment the Company believes is exempt under state law. The Company has appealed the assessment and a hearing was scheduled for November 30, 2016. In November 2016, the State of Ohio deferred the hearing until 2017. While we are not able to predict the outcome of the appeal, this matter is not expected to have a material adverse effect on the financial position or results of operations of the Company.
On December 16, 2015, a lawsuit alleging wrongful death was filed titled Cecilia R.G. Uballe and Sabrina Barber, beneficiaries of Eseciel D. Uballe, Deceased v. Bison Trucking LLC in the U.S. District Court of Midland Texas. On December 5, 2016, the Company settled this matter. This resolution did not cause a material impact on our financial position, results of operation or cash flows.
Due to the nature of our business, we are, from time to time, involved in other routine litigation or subject to disputes or claims related to our business activities, including workers’ compensation claims and employment related disputes. In the opinion of our management, none of the pending litigation, disputes or claims against us, if decided adversely, will have a material adverse effect on our financial condition, cash flows or results of operations.
Item 4. Mine Safety Disclosures
Not applicable.
PART II. OTHER INFORMATION
Item 5. Market for Registrant's Common Equity, Related Stockholder Matters and Issuer Purchases of Equity Securities.
Market Information
Our common stock is traded on the NASDAQ Global Select Market under the symbol "TUSK." The following table presents the high and low sales prices of our common stock for each quarter in 2016 based on the closing price of a given trading day:
|
| | | | | | |
2016 | High | Low |
First Quarter | — |
| — |
|
Second Quarter | — |
| — |
|
Third Quarter | — |
| — |
|
Fourth Quarter (a) | $ | 17.25 |
| $ | 12.48 |
|
(a) Our common stock commenced trading on the NASDAQ on October 14, 2016 in connection with our IPO.
Holders of Record
As of the close of business on February 21, 2017, there were four holders of record of our common stock. The number of holders of record of our common stock is not representative of the number of beneficial holders because many of the shares are held by depositories, brokers or nominees.
Use of Proceeds
On October 13, 2016, our registration statement on Form S-1 (File No. 333-213504) was declared effective and on October 19, 2016, we completed the IPO of 7,750,000 shares of common stock of which 7,500,000 were offered by the Company. The stock was priced at $15.00 per share and we received net proceeds of approximately $103.1 million from the sale of these shares of common stock, after deducting underwriting discounts and commissions and offering expenses. Of these proceeds, approximately $78.1 million was used to repay the outstanding borrowings under our revolving credit facility. The remaining net proceeds will be used for other general corporate purposes, which may include the acquisition of additional equipment and complementary businesses that enhance our existing service offerings, broaden our service offerings or expand our customer relationships.
Unregistered Sales of Equity Securities
On October 12, 2016, prior to the effective date of our registration statement relating to the IPO, we issued 20,615,700 shares of our common stock to Mammoth Energy Holdings LLC, 9,150,000 shares of our common stock to Gulfport and 234,300 shares of our common stock to Rhino Exploration LLC in connection with their contribution of their respective membership interests in Mammoth Energy Partners LLC described in more detail in Item 7. “Management’s Discussion and Analysis of Financial Condition and Results of Operations.” These shares of our common stock were issued in reliance upon the exemption from the registration requirements of the Securities Act provided by Section 4(a)(2) of the Securities Act as sales by an issuer not involving any public offering.
Issuer Purchases of Equity Securities
Not applicable.
Dividends
Mammoth Inc. has never declared or paid any cash dividends on its capital stock. We currently intend to retain all available funds and any future earnings for use in the operation and expansion of our business and do not anticipate declaring or paying any cash dividends in the foreseeable future. Any future determination as to the declaration and payment of dividends will be at the discretion of our board of directors and will depend on then-existing conditions, including our financial condition, results of operations, contractual restrictions, capital requirements, business prospects and other factors that our board of directors considers relevant. In addition, the terms of our existing outstanding borrowings restrict the payment of dividends to the holders of our common stock and any other equity holders.
Performance Graph
The following graph and table compares the cumulative total return of a $100 investment in our common stock from October 14, 2016, the date on which our stock began trading on the NASDAQ Global Select Market, through December 31, 2016, with the total cumulative return of a $100 investment in the Standard & Poors Stock Index and the Philadelphia Stock Exchange Oil Service Sector Index during that period.
|
| | | | | | |
| October 14, 2016 | December 31, 2016 |
Mammoth Energy Service, Inc. | $ | 100.00 |
| $ | 114.63 |
|
S&P 500 Stock Index | 100.00 |
| 104.88 |
|
PHLX Oil Service Index | 100.00 |
| 111.51 |
|
This graph shall not be deemed to be "soliciting material" or to be "filed" with the SEC.
Item 6. Selected Financial Data
This section presents our selected historical combined consolidated financial data. The selected historical combined consolidated financial data presented below is not intended to replace our historical combined consolidated financial statements. You should read the following data along with Item 7. "Management’s Discussion and Analysis of Financial Condition and Results of Operations” and the consolidated financial statements and related notes, each of which is included elsewhere in this annual report.
The historical financial information for periods prior to October 12, 2016, contained in this annual report relates to Mammoth Energy Partners LP, a Delaware limited partnership, or the Partnership. On October 12, 2016, the Partnership was converted into a Delaware limited liability company named Mammoth Energy Partners LLC, or Mammoth LLC, and then each member of Mammoth LLC contributed all of its membership interests in Mammoth LLC to Mammoth Energy Services, Inc., a Delaware corporation, or Mammoth Inc. Prior to the conversion and the contribution, Mammoth Inc. was a wholly-owned subsidiary of the Partnership. Upon the conversion and the contribution, Mammoth LLC (as the converted successor to the Partnership) became a wholly-owned subsidiary of Mammoth Inc.
On October 13, 2016, Mammoth Inc. priced 7,750,000 shares of its common stock in the IPO at a price to the public of $15.00 per share and, on October 14, 2016, Mammoth Inc.’s common stock began trading on The Nasdaq Global Select Market under the symbol “TUSK.” On October 19, 2016, Mammoth Inc. closed its IPO. Unless the context otherwise requires, references in this report to “we,” “our,” “us” or like terms, when used in a historical context for periods prior to October 12, 2016 refer to the Partnership and its subsidiaries. References in this report to “we,” “our,” “us” or like terms, when used for periods beginning on or after October 12, 2016 refer to Mammoth Inc. and its subsidiaries.
Presented below is our historical financial data for the periods and as of the dates indicated. The historical financial data for the years ended December 31, 2016, 2015 and 2014 and the balance sheet data as of December 31, 2016, 2015 and 2014 are derived from our audited consolidated financial statements included elsewhere in this annual report. As an emerging growth company, in accordance with Item 301 of Regulation S-K, the historical financial data for the years ended December 31, 2013 and 2012 and the balance sheet data as of December 31, 2013 and 2012 are not included in this annual report.
|
| | | | | | | | | | | |
| Years Ended December 31, |
STATEMENT OF OPERATIONS DATA: | 2016 | | 2015 | | 2014 |
Total revenues | $ | 230,998,721 |
| | $ | 359,936,693 |
| | $ | 259,526,004 |
|
Total cost and expenses | $ | 262,062,627 |
| | $ | 381,407,100 |
| | $ | 243,723,929 |
|
Operating (loss) income | $ | (31,063,906 | ) | | $ | (21,470,407 | ) | | $ | 15,802,075 |
|
Total other expense | $ | (3,459,218 | ) | | $ | (7,350,093 | ) | | $ | (10,298,429 | ) |
(Loss) income before income taxes | $ | (34,523,124 | ) | | $ | (28,820,500 | ) | | $ | 5,503,646 |
|
Net loss | $ | (88,407,995 | ) | | $ | (27,231,414 | ) | | $ | (2,010,548 | ) |
Comprehensive loss | $ | (85,697,390 | ) | | $ | (32,046,233 | ) | | $ | (1,537,834 | ) |
| | | | | |
Net loss per share (basic and diluted) | $ | (2.81 | ) | | $ | (0.91 | ) | | $ | (0.10 | ) |
Weighted average number of shares outstanding | 31,500,000 |
| | 30,000,000 |
| | 21,056,073 |
|
| | | | | |
Pro forma information (unaudited): |
| | | | |
Net loss, as reported | $ | (88,407,995 | ) | | $ | (27,231,414 | ) | | $ | (2,010,548 | ) |
Taxes on income earned as a non-taxable entity | $ | 13,750,827 |
| | $ | 2,469,030 |
| | $ | (5,207,628 | ) |
Taxes due to change to C corporation | $ | 53,088,861 |
| | $ | — |
| | $ | — |
|
Pro forma net loss | $ | (21,568,307 | ) | | $ | (24,762,384 | ) | | $ | (7,218,176 | ) |
Pro forma loss per common share | | | | | |
Basic and diluted | $ | (0.58 | ) | | $ | (0.66 | ) | | $ | (0.34 | ) |
Weighted average pro forma shares outstanding—basic and diluted | 37,500,000 |
| | 37,500,000 |
| | 21,056,073 |
|
| | | | | |
CASH FLOW DATA: | | | | | |
Cash flows provided by operations | $ | 28,101,652 |
| | $ | 68,392,616 |
| | $ | 8,247,714 |
|
Cash flows used in investing activities | $ | (7,295,817 | ) | | $ | (24,834,909 | ) | | $ | (101,564,915 | ) |
Cash flows provided by provided by (used in) financing activities | $ | 4,659,841 |
| | $ | (55,931,472 | ) | | $ | 103,125,751 |
|
|
| | | | | | | | | | | |
| December 31, |
BALANCE SHEET DATA: | 2016 | | 2015 | | 2014 |
Cash and cash equivalents | $ | 28,693,985 |
| | $ | 3,074,072 |
| | $ | 15,674,492 |
|
Property, plant and equipment, net | $ | 221,247,228 |
| | $ | 273,026,665 |
| | $ | 334,150,453 |
|
Total assets | $ | 420,553,835 |
| | $ | 450,985,570 |
| | $ | 580,714,876 |
|
Total current liabilities | $ | 29,339,480 |
| | $ | 30,790,175 |
| | $ | 71,108,086 |
|
Long-term debt | $ | — |
| | $ | 95,000,000 |
| | $ | 146,041,013 |
|
Total liabilities | $ | 79,512,155 |
| | $ | 127,822,308 |
| | $ | 225,504,670 |
|
Total equity | $ | 341,041,680 |
| | $ | 323,163,262 |
| | $ | 355,210,206 |
|
Item 7. Management’s Discussion and Analysis of Financial Condition and Results of Operations
The following discussion and analysis should be read in conjunction with the consolidated financial statements and related notes included elsewhere in this Annual Report on Form 10-K. This discussion contains forward-looking statements reflecting our current expectations, estimates and assumptions concerning events and financial trends that may affect our future operating results or financial position. Actual results and the timing of events may differ materially from those contained in these forward-looking statements due to a number of factors, including those discussed in Item 1A. "Risk Factors” and the section entitled “Forward-Looking Statements” appearing elsewhere in this Annual Report on Form 10-K.
Overview
We are an integrated, growth-oriented oilfield service company serving companies engaged in the exploration and development of North American onshore unconventional oil and natural gas reserves. Our primary business objective is to grow our operations and create value for stockholders through organic opportunities and accretive acquisitions. Our suite of services includes pressure pumping services, well services, natural sand proppant services, contract land and directional drilling services and other energy services. Our pressure pumping services division provides hydraulic fracturing services. Our well services division provides pressure control services, flowback services and equipment rentals. Our natural sand proppant services division sells, distributes and is capable of producing proppant for hydraulic fracturing. Our contract land and directional drilling services division provides drilling rigs and crews for operators as well as rental equipment, such as mud motors and operational tools, for both vertical and horizontal drilling. Our other energy services division currently provides housing, kitchen and dining, and recreational service facilities for oilfield workers located in remote areas away from readily available lodging. We believe that the services we offer play a critical role in increasing the ultimate recovery and present value of production streams from unconventional resources. Our complementary suite of completion and production and drilling related services provides us with the opportunity to cross-sell our services and expand our customer base and geographic positioning.
On October 19, 2016, Mammoth Inc. closed its IPO of 7,750,000 shares of common stock, of which 7,500,000 shares were sold by Mammoth Inc. and the remaining 250,000 shares were sold by certain selling stockholders, at a price to the public of $15.00 per share. Mammoth Inc.’s common stock is traded on the Nasdaq Global Select Market under the symbol “TUSK.” Unless the context otherwise requires, references in this report to “we,” “our,” “us,” or like terms, when used in a historical context for periods prior to October 12, 2016 refer to the Partnership and its subsidiaries. References in this report to “we,” “our,” “us,” or like terms, when used in the present tense or for periods commencing on or after October 12, 2016 refer to Mammoth Inc. and its subsidiaries. Mammoth Inc. was formed in June 2016, and did not conduct any material business operations prior to the completion of the IPO and the contribution described below completed on October 12, 2016 immediately prior to the IPO. Prior to the IPO, Mammoth Inc. was a wholly-owned subsidiary of the Partnership.
On November 24, 2014, Mammoth Energy Holdings LLC, or Mammoth Holdings, Gulfport Energy Corporation, or Gulfport, and Rhino Exploration LLC, or Rhino, contributed to the Company their respective interests in the following entities: Bison Drilling and Field Services, LLC, or Bison Drilling; Bison Trucking LLC, or Bison Trucking; White Wing Tubular Services LLC, or White Wing; Barracuda Logistics LLC, or Barracuda; Panther Drilling Systems LLC, or Panther Drilling; Redback Energy Services LLC, or Redback Energy Services; Redback Coil Tubing LLC, or Redback Coil Tubing; Muskie Proppant LLC, or Muskie Proppant; Stingray Pressure Pumping LLC, or Pressure Pumping; Stingray Logistics LLC, or Logistics; and Great White Sand Tiger Lodging Ltd., or Lodging. Upon completion of these contributions, Mammoth Holdings, Gulfport and Rhino beneficially owned a 68.7%, 30.5% and 0.8% equity interest, respectively, in the Partnership. Subsequently, the Partnership formed Redback Pumpdown Services LLC, or Pumpdown, Mr. Inspections LLC, or Mr. Inspections, Silverback Energy Services LLC, or Silverback, and Mammoth Inc. as wholly-owned subsidiaries.
On October 12, 2016, prior to and in connection with the IPO, the Partnership converted to a Delaware limited liability company named Mammoth Energy Partners LLC, or Mammoth LLC, and Mammoth Holdings, Gulfport and Rhino contributed their respective membership interests in Mammoth LLC to us in exchange for shares of our common stock, and Mammoth LLC became our wholly-owned subsidiary.
Each year, we evaluate qualitative and quantitative aspects of our service lines. As a result of that review as of December 31, 2016, we have split our completion and production division into pressure pumping services and well services. In addition, we renamed our remote accommodation services as other energy services. As a result, we now manage our business through five operating divisions: pressure pumping services, well services, natural sand proppant services, contract and directional drilling services and other energy services.
Since the dates presented below, we have conducted our operations through the following entities:
Pressure Pumping Services Division
| |
• | Pressure Pumping—March 2012 |
| |
• | Mr. Inspections—January 2015 |
| |
• | Mammoth Equipment Leasing—November 2016 |
Well Services Division
| |
• | Redback Energy Services—October 2011 |
| |
• | Redback Coil Tubing—May 2012 |
| |
• | Mammoth Energy Services—June 2016 |
Natural Sand Proppant Services Division
| |
• | Muskie Proppant—September 2011 |
Contract Land and Directional Drilling Services Division
| |
• | Bison Drilling—November 2010 |
| |
• | Panther Drilling—December 2012 |
| |
• | Bison Trucking—August 2013 |
| |
• | White Wing—September 2014 |
Other Energy Services Division
Industry Overview
The oil and natural gas industry has traditionally been volatile and is influenced by a combination of long-term, short-term and cyclical trends, including the domestic and international supply and demand for oil and natural gas, current and expected future prices for oil and natural gas and the perceived stability and sustainability of those prices, production depletion rates and the resultant levels of cash flows generated and allocated by exploration and production companies to their drilling, completion and related services and products budget. The oil and natural gas industry is also impacted by general domestic and international economic conditions, political instability in oil producing countries, government regulations (both in the United States and elsewhere), levels of customer demand, the availability of pipeline capacity and other conditions and factors that are beyond our control.
Demand for most of our products and services depends substantially on the level of expenditures by companies in the oil and natural gas industry. The significant decline in oil and natural gas prices that began in the third quarter of 2014 continued into February 2016, when the closing price of oil reached a 12-year low of $26.19 per barrel on February 11, 2016. The low commodity price environment caused a reduction in the drilling, completion and other production activities of most of our customers and their spending on our products and services.
The reduction in demand during the first part of 2016, and the resulting oversupply of many of the services and products we provide, substantially reduced the prices we could charge our customers for our products and services, and had a negative impact on the utilization of our services. This overall trend with respect to our customers’ activities and spending continued in 2016. However, oil prices have increased since the 12-year low recorded on February 11, 2016, reaching a high of $54.06 per barrel on December 28, 2016. As commodity prices have begun to recover, we have experienced an increase in activity. If near term commodity prices stabilize at current levels and recover further, we expect to continue to experience an increase in demand for our services and products, particularly in our completion and production, natural sand proppant and contract land and directional drilling businesses. Our other energy services revenue, which are currently only attributable to our remote accommodations business, remained stable through the fourth quarter of 2016. However, we currently project that our other energy services revenues will decrease in the first quarter of 2017 if we are unable to replace one customer that represented approximately 85% of such services during the year ended December 31, 2016 when it completes the construction phase of its project, which is currently estimated to occur in early 2017.
Results of Operations
Year Ended December 31, 2016 Compared to Year Ended December 31, 2015
|
| | | | | | | |
| Years Ended |
| December 31, 2016 | | December 31, 2015 |
Revenue: | | | |
Pressure pumping services | $ | 124,308,226 |
| | $ | 169,980,686 |
|
Well services | 10,024,813 |
| | 28,851,341 |
|
Natural sand proppant services | 33,756,444 |
| | 52,790,203 |
|
Contract land and directional drilling services | 32,042,509 |
| | 73,032,089 |
|
Other energy services | 30,866,729 |
| | 35,282,374 |
|
Total revenue | 230,998,721 |
| | 359,936,693 |
|
| | | |
Cost of Revenue: | | | |
Pressure pumping services | 86,808,742 |
| | 131,717,344 |
|
Well services | 13,540,309 |
| | 28,144,431 |
|
Natural sand proppant services | 28,166,829 |
| | 43,890,437 |
|
Contract land and directional drilling services | 31,847,969 |
| | 57,489,608 |
|
Other energy services | 13,186,060 |
| | 15,105,497 |
|
Total cost of revenue | 173,549,909 |
| | 276,347,317 |
|
Selling, general and administrative expenses | 16,730,975 |
| | 20,541,548 |
|
Depreciation and amortization | 69,910,858 |
| | 72,393,882 |
|
Impairment of long-lived assets | 1,870,885 |
| | 12,124,353 |
|
Operating loss | (31,063,906 | ) | | (21,470,407 | ) |
Interest expense, net | (3,711,457 | ) | | (5,192,329 | ) |
Other (expense) income | 252,239 |
| | (2,157,764 | ) |
Loss before income taxes | (34,523,124 | ) | | (28,820,500 | ) |
Provision (benefit) for income taxes | 53,884,871 |
| | (1,589,086 | ) |
Net loss | $ | (88,407,995 | ) | | $ | (27,231,414 | ) |
Revenue. Revenue for 2016 decreased $128.9 million, or 36%, to $231.0 million from $359.9 million for 2015. Revenue by operating division was as follows:
Pressure Pumping Services. Pressure pumping services division revenue decreased $45.7 million, or 27%, to $124.3 million for 2016 from $170.0 million for 2015. The decrease in our pressure pumping services revenue was driven primarily by a decline in fleet utilization from 63%, on three active fleets, for 2015 to 50%, on two active fleets, for 2016. The division decreases also included decreases due to the suspension of our pump down services in the Woodford Shale during the fourth quarter of 2015.
Well Services. Well services division revenue decreased $18.9 million, or 65%, to $10.0 million for 2016 from $28.8 million for 2015. Our coil tubing division revenue declined as a result of a decrease in average day rates from approximately $25,000 for 2015 to approximately $19,000 for 2016. Our flowback services declined as a result of discontinuing our flowback operations in the Appalachian Basin in December 2015 combined with a decline in both pricing and utilization of such services in our other basins.
Natural Sand Proppant Services. Natural sand proppant services division revenue decreased $19.0 million, or 36%, to $33.8 million for 2016, from $52.8 million for 2015. The decrease was primarily attributable to a reduction in the average sales price per ton of sand from $103 in 2015 to $59 in 2016. The decrease was partially offset by an increase in tons of sand sold from approximately 512,700 for 2015 to approximately 575,400 in 2016.
Contract Land and Directional Drilling Services. Contract land and directional drilling services division revenue decreased $41.0 million, or 56%, from $73.0 million for 2015 to $32.0 million for 2016. The decrease was primarily attributable to our land drilling services, which accounted for $35.0 million, or 86%, of the operating division decrease. The decrease in our land drilling services was driven by a decline in average active rigs from ten for 2015 to four for 2016 as well as a decline in average day rates from approximately $17,900 to approximately $12,900 during those same years. Our directional drilling services accounted for $4.3 million, or 10%, of the operating division decrease as a result of utilization declining from 36% for 2015 to 22% for 2016. Our rig moving services accounted for $1.2 million, or 3%, of the operating division decrease primarily driven by the decline in drilling activity. Our drill pipe inspection services accounted for $0.5 million, or 1%, of the operating division decrease as a result of of this business line being discontinued in the second quarter of 2016.
Other Energy Services. Other energy services division revenue, consisting of revenue derived from our remote accommodations business, decreased $4.4 million, or 13%, to $30.9 million for 2016 from $35.3 million for 2015. The decrease was a result of a decrease in revenue per room night, in Canadian dollars, from $180 for 2015 to $177 for 2016. Additionally, total room nights rented decreased from 251,233 for 2015 to 230,530 for 2016.
Cost of Revenue. Cost of revenue decreased $102.8 million from $276.3 million, or 77% of total revenue, for 2015 to $173.5 million, or 75% of total revenue, for 2016. Cost of revenue by operating division was as follows:
Pressure Pumping Services. Pressure pumping services division cost of revenue decreased $44.9 million, or 34%, from $131.7 million for 2015 to $86.8 million for 2016. The decrease was primarily due to decreases in proppant costs, repairs and maintenance expense and labor-related costs. As a percentage of revenue, our pressure pumping services division cost of revenue was 70% and 77% for 2016 and 2015, respectively. The decrease in costs as a percentage of revenue was primarily due to lower repairs and maintenance expense and a decrease in stages completed to 2,442 from 2,963 for 2016 and 2015, respectively.
Well Services. Well services division cost of revenue decreased $14.6 million, or 52%, from $28.1 million for 2015 to $13.5 million for 2016. The decrease was primarily due to declines in labor-related costs and repairs and maintenance expense. As a percentage of revenue, our well services division cost of revenue was 135% and 98% for 2016 and 2015, respectively. The increase in costs as a percentage of revenue was primarily due increased pricing pressure.
Natural Sand Proppant Services. Natural sand proppant services division cost of revenue decreased $15.7 million, or 36%, from $43.9 million for 2015 to $28.2 million for 2016, primarily due to a decrease in product costs. As a percentage of revenue, cost of revenue was 83% for each of 2016 and 2015, respectively.
Contract Land and Directional Drilling Services. Contract land and directional drilling services division cost of revenue decreased $25.7 million, or 45%, from $57.5 million for 2015 to $31.8 million for 2016, primarily due to a decrease in labor-related costs and lower utilization. As a percentage of revenue, our contract land and directional drilling services division cost of revenue was 99% and 79% for 2016 and 2015. The increase was primarily due to increased repairs and maintenance and compensation as a percentage of revenue.
Other Energy Services. Other energy services division cost of revenues decreased $1.9 million, or 13%, from $15.1 million for 2015 to $13.2 million for 2016, primarily due to declines in contracted labor-related costs. As a percentage of revenues, cost of revenues was 43% for each of 2016 and 2015. Average revenue per room night, in Canadian dollars, decreased from $180 for 2015 to $177 for 2016. Additionally, total room nights rented decreased from 251,233 for 2015 to 230,530 for 2016.
Selling, General and Administrative Expenses. Selling, general and administrative expenses represent the costs associated with managing and supporting our operations. These expenses decreased $3.8 million, or 19%, to $16.7 million for 2016, from $20.5 million for 2015. The decrease in expenses was primarily attributable to a $2.5 million reduction in bad debt expense, a $0.3 million reduction in compensation and benefits and reductions in travel-related charges and office and computer support expense of $0.5 million and $0.5 million, respectively, for 2016 compared to 2015.
Depreciation and Amortization. Depreciation and amortization decreased $2.5 million, or 3%, to $69.9 million for 2016 from $72.4 million in 2015. The decrease was primarily attributable to $26.2 million of assets that fully depreciated during 2016 in addition to impairments of $10.2 million in fixed assets during 2015 and was partially offset by placing in-service of $6.6 million of capital additions.
Impairment of Long-lived Assets. We recorded an impairment of long-lived assets in 2016 of $1.9 million, which was attributable to various fixed assets. Impairments for 2015 were $12.1 million, of which $10.2 million was attributable to various fixed assets and $1.9 million was attributable to the termination of a long-term contract.
Interest Expense, net. Interest expense decreased $1.5 million, or 30%, to $3.7 million during 2016 compared to $5.2 million during 2015. The decrease in interest expense was attributable to a decrease in average borrowings during 2016 and the repayment of all outstanding borrowings in October 2016 with a portion of the net proceeds from the IPO.
Other (Expense) Income, net. Non-operating charges resulted in other income, net, of $0.2 million for 2016 compared to other expense, net of $2.2 million for 2015. The 2016 amount included $0.7 million of gain recognition on assets disposed during the period compared to a $1.4 million loss for 2015.
Income Taxes. In 2015, we were treated as a pass-through entity for federal income tax and most state income tax purposes. The income tax expense recognized was primarily attributable to our subsidiary, Lodging, which provides our accommodation services in our other energy services division. For 2016, we recognized income tax expense of $53.9 million compared to an income tax benefit of $1.6 million for 2015. In 2016, in connection with the IPO, we became subject to federal income taxes which triggered recognition of federal income tax liabilities associated with historical earnings (See Note 1 to our consolidated financial statements included elsewhere in this annual report for more information). The 2016 amount included recognition of other items related to the change in classification to a C corporation resulting in total one-time effect of $53.1 million. The 2015 amount included recognition of deferred taxes recorded on income from Lodging in the U.S. related to an entity election that required us to disregard previously recorded deferred tax liabilities. We made an election on entity status in September 2015 that allowed the reversal of the deferred taxes in 2015.
Year Ended December 31, 2015 Compared to Year Ended December 31, 2014
|
| | | | | | | |
| Years Ended |
| December 31, 2015 | | December 31, 2014 |
Revenue: | | | |
Pressure pumping services | $ | 169,980,686 |
| | $ | 24,779,686 |
|
Well services | 28,851,341 |
| | 45,253,092 |
|
Natural sand proppant services | 52,790,203 |
| | 46,350,274 |
|
Contract land and directional drilling services | 73,032,089 |
| | 122,164,943 |
|
Other energy services | 35,282,374 |
| | 20,978,009 |
|
Total Revenue | 359,936,693 |
| | 259,526,004 |
|
| | | |
Cost of Revenue: | | | |
Pressure pumping services | 131,717,344 |
| | 17,293,057 |
|
Well services | 28,144,431 |
| | 31,715,681 |
|
Natural sand proppant services | 43,890,437 |
| | 38,815,543 |
|
Contract land and directional drilling services | 57,489,608 |
| | 93,571,050 |
|
Other energy services | 15,105,497 |
| | 9,673,570 |
|
Total cost of revenue | 276,347,317 |
| | 191,068,901 |
|
Selling, general and administrative expenses | 20,541,548 |
| | 17,027,863 |
|
Depreciation and amortization | 72,393,882 |
| | 35,627,165 |
|
Impairment of long-lived assets | 12,124,353 |
| | — |
|
Operating (loss) income | (21,470,407 | ) | | 15,802,075 |
|
Interest expense, net | (5,192,329 | ) | | (4,573,933 | ) |
Other expense | (2,157,764 | ) | | (5,724,496 | ) |
(Loss) income before income taxes | (28,820,500 | ) | | 5,503,646 |
|
(Benefit) provision for income taxes | (1,589,086 | ) | | 7,514,194 |
|
Net loss | $ | (27,231,414 | ) | | $ | (2,010,548 | ) |
Revenue. Revenue for 2015 increased $100.4 million, or 39%, to $359.9 million from $259.5 million for 2014. The net increase in revenue by operating division was as follows:
Pressure Pumping Services. Pressure pumping services division revenue increased $145.2 million, or 585%, to $170.0 million for 2015 from $24.8 million for 2014. The increase was primarily attributable to our pressure pumping services, which were acquired in connection with our acquisition of Pressure Pumping in November 2014 and accounted for substantially all of the division increase in revenue. The increase was partially offset by a decrease in our pump down services primarily driven by a decline in utilization which saw a drop in utilization from 51% for 2014 to 21% for 2015.
Well Services. Well services division revenue decreased $16.4 million, or 36%, to $28.8 million for 2015 from $45.2 million for 2014. The decreases in revenue from both our coil tubing and flowback services, which decreased $9.7 million and $6.7 million, respectively. Our coil tubing division revenue declined as a result of a decline in demand for these services. Our flowback services revenue declined as a result of as a result of discontinuing our flowback operations in the Appalachian Basin in December 2015 combined with a decline in both pricing and utilization of such services in our other basins.
Natural Sand Proppant Services. Natural sand proppant services division revenue increased $6.5 million, or 14%, to $52.8 million for 2015, from $46.3 million for 2014. The increase was primarily attributable to an increase in our pressure pumping services.
Contract Land and Directional Drilling Services. Contract land and directional drilling services division revenue decreased $49.2 million, or 40%, to $73.0 million for 2015, from $122.2 million for 2014. The decrease was primarily attributable to a decrease in drilling services revenue of $41.4 million, or 84% of the net division decrease in revenue. The decrease in drilling services revenue was primarily attributable to a decline in average active rigs from 12 in 2014 to eight in 2015 as well as a decline in average day rates from $18,900 to $17,900 during those same years. For 2015, our directional drilling services division saw a reduction of $8.1 million, or 17%, of the net division decrease in revenue. Our rig moving and drill pipe inspection service lines saw a combined increase in revenue of $0.3 million, or 1%, of the net decrease in revenue primarily driven by a full year of revenue from our drill pipe inspection service line, which began operations in September 2014.
Other Energy Services. Other energy services division revenue increased $14.3 million, or 68%, to $35.3 million for 2015 from $21.0 million for 2014. The increase was a result of increased occupancy resulting from the expansion of camp capacity from 498 to 884 rooms in the fourth quarter of 2014 as well as an increase in room nights from 115,258 in 2014 to 251,233 in 2015. While the room nights increased, average revenue per room night declined from $206 in 2014 to $180 in 2015.
Cost of Revenue. Cost of revenue increased $85.2 million, or 31%, from $191.1 million, or 74% of total revenue, for 2014 to $276.3 million, or 77% of total revenue, for 2015. Cost of revenue by operating division was as follows:
Pressure Pumping Services. Pressure pumping services division cost of revenue increased $114.4 million, or 661%, from $17.3 million for 2014 to $131.7 million for 2015, primarily due to the acquisition of Pressure Pumping in November 2014. The increase in cost of revenue associated with our pressure pumping services accounted for $111.1 million, or 97%, of the increase. As a percentage of revenue, cost of revenue was 77% and 71% for 2015 and 2014, respectively. The year-over-year increase in cost of revenue as a percentage of revenue was primarily due to a decline in utilization in our pump down services from 51% for 2014 to 21% for 2015.
Well Services. Well services division cost of revenue decreased $3.6 million, or 11%, from $31.7 million for 2014 to $28.1 million for 2015, primarily due a decline in demand for both our coil tubing and flowback services. As a percentage of revenue, cost of revenue was 98% and 70% for 2015 and 2014, respectively. The year-over-year increase in cost of revenue as a percentage of revenue was primarily due to increased pricing pressures from our customers on the costs for these services.
Natural Sand Proppant Services. Natural sand proppant services cost of revenue increased $5.1 million, or 13%, from $38.8 million for 2014 to $43.9 million for 2015, primarily due to an increase in our pressure pumping services. As a percentage of revenue, cost of revenue was 83% and 84% for 2015 and 2014, respectively. The decrease was primarily due to a reduction of labor-related costs.
Contract Land and Directional / Drilling Services. Contract land and directional drilling services division cost of revenue decreased $36.1 million, or 39%, from $93.6 million for 2014 to $57.5 million for 2015, primarily due to a decrease in labor-related costs and a decline in average active rigs from 12 in 2014 to eight in 2015. As a percentage of revenue, drilling cost of revenue was 79% and 77% for 2015 and 2014, respectively. The increase was primarily due to increased competition for our services, which resulted in a decline in average day rates from $18,900 to $17,900 during the same periods.
Other Energy Services. Other energy services division cost of revenue increased $5.4 million, or 56%, from $9.7 million for 2014 to $15.1 million for 2015, primarily due to increases in contracted labor-related costs. As a percentage of revenue, cost of revenue was 43% and 46% for 2015 and 2014, respectively. As a percentage of revenue, the decrease in cost of revenue was primarily due to the increase in division revenue in 2015 associated with an increase in room nights from 115,258 in 2014 to 251,233 in 2015.
Selling, General and Administrative Expenses. Selling, general and administrative expenses represent the costs associated with managing and supporting our operations. These expenses increased $3.5 million, or 21%, to $20.5 million for 2015, from $17.0 million for 2014. The increase in expenses was primarily attributable to a $3.1 million increase in bad debt expense.
Depreciation and Amortization. Depreciation and amortization increased $36.8 million, or 103%, to $72.4 million for 2015 from $35.6 million for 2014. The increase was primarily attributable to the $101.5 million in property, plant and equipment and $40.7 million in amortizing intangible assets that were acquired in connection with our acquisition of Stingray Pressure Pumping LLC and Stingray Logistics LLC on November 24, 2014. The remainder of the year-over-year increase was
attributable to the $111.7 million in property, plant and equipment purchased in 2014 and $26.3 million in property, plant and equipment purchased in 2015.
Impairment of Long-lived Assets. We recorded an impairment of long-lived assets in 2015 of $12.1 million, of which $10.2 million was attributable to various fixed assets and $1.9 million was attributable to the termination of a long-term contract. No impairment of long-lived assets was recorded by us in 2014.
Interest Expense, net. Interest expense increased $0.6 million, or 13%, to $5.2 million for 2015, compared to $4.6 million for 2014. The increase in interest expense was attributable to increased average borrowings during 2015 due primarily to $49.8 million in debt that was assumed in our acquisition of Stingray Pressure Pumping LLC and Stingray Logistics LLC on November 24, 2014. The increase in borrowings was partially offset by the repayment of $70.4 million in debt during 2015.
Other (Expense) Income, net. Non-operating charges resulted in other expense, net of $2.2 million for 2015 compared to other expense, net of $5.7 million for 2014. The 2015 amount consisted primarily of the loss on disposal of long-lived assets, compared to 2014 which included charges associated with a then proposed initial public offering that was postponed due to market conditions existing at that time.
Income Taxes. During 2015 and 2014, we were treated as a pass-through entity for federal income tax and most state income tax purposes. The income tax expense recognized was primarily attributable to our subsidiary, Lodging, which provides our accommodation services. For 2015, we recognized income tax benefit of $1.6 million compared to an income tax expense of $7.5 million for 2014. The change was primarily attributable to deferred taxes recorded on income from Lodging in the U.S. for 2014 related to an entity election that required us to disregard previously recorded deferred tax liability. We made an election on entity status in September 2015 that allowed the reversal of the deferred taxes in 2015.
Non-GAAP Financial Measures
Adjusted EBITDA is a supplemental non-GAAP financial measure that is used by management and external users of our financial statements, such as industry analysts, investors, lenders and rating agencies. We define Adjusted EBITDA as net income (loss) before depreciation and amortization, impairment of long-lived assets, one-time compensation charges associated with the IPO, equity based compensation, interest income, interest expense, other (income) expense, net (which is comprised of the (gain) or loss on disposal of long-lived assets and charges associated with the Partnership's proposed initial public offering in 2014) and provision (benefit) for income taxes. We exclude the items listed above from net income (loss) in arriving at Adjusted EBITDA because these amounts can vary substantially from company to company within our industry depending upon accounting methods and book values of assets, capital structures and the method by which the assets were acquired. Adjusted EBITDA should not be considered as an alternative to, or more meaningful than, net income (loss) or cash flows from operating activities as determined in accordance with GAAP or as an indicator of our operating performance or liquidity. Certain items excluded from Adjusted EBITDA are significant components in understanding and assessing a company’s financial performance, such as a company’s cost of capital and tax structure, as well as the historic costs of depreciable assets, none of which are components of Adjusted EBITDA. Our computations of Adjusted EBITDA may not be comparable to other similarly titled measure of other companies. We believe that Adjusted EBITDA is a widely followed measure of operating performance and may also be used by investors to measure our ability to meet debt service requirements.
The following tables also provide a reconciliation of Adjusted EBITDA to the GAAP financial measure of net income or (loss) for each of our operating segments for the specified periods.
Consolidated
|
| | | | | | | | | | | |
| Years Ended December 31, |
Reconciliation of Adjusted EBITDA to net income (loss): | 2016 | | 2015 | | 2014 |
Net loss | $ | (88,407,995 | ) | | $ | (27,231,414 | ) | | $ | (2,010,548 | ) |
Depreciation and amortization | 69,910,858 |
| | 72,393,882 |
| | 35,627,165 |
|
Impairment of long-lived assets | 1,870,885 |
| | 12,124,353 |
| | — |
|
One-time IPO compensation charges | 1,200,770 |
| | — |
| | — |
|
Equity based compensation | 501,147 |
| | — |
| | 3,838,842 |
|
Interest income | — |
| | (98,492 | ) | | (214,141 | ) |
Interest expense | 3,711,457 |
| | 5,290,821 |
| | 4,788,074 |
|
Other (income) expense, net | (252,239 | ) | | 2,157,764 |
| | 5,724,496 |
|
Provision (benefit) for income taxes | 53,884,871 |
| | (1,589,086 | ) | | 7,514,194 |
|
Adjusted EBITDA | $ | 42,419,754 |
| | $ | 63,047,828 |
| | $ | 55,268,082 |
|
Pressure Pumping Services
|
| | | | | | | | | | | |
| Years Ended December 31, |
Reconciliation of Adjusted EBITDA to net income (loss): | 2016 | | 2015 | | 2014 |
Net loss | $ | (4,605,494 | ) | | $ | (5,579,236 | ) | | $ | (80,771 | ) |
Depreciation and amortization | 37,012,902 |
| | 35,728,715 |
| | 4,015,572 |
|
Impairment of long-lived assets | 138,587 |
| | 1,213,885 |
| | — |
|
One-time IPO compensation charges | 101,760 |
| | — |
| | — |
|
Equity based compensation | 176,326 |
| | — |
| | — |
|
Interest expense | 599,147 |
| | 1,859,195 |
| | 386,618 |
|
Other expense, net | 26,743 |
| | 66,889 |
| | 1,744,695 |
|
Provision for income taxes | — |
| | 72,435 |
| | 10,897 |
|
Adjusted EBITDA | $ | 33,449,971 |
| | $ | 33,361,883 |
| | $ | 6,077,011 |
|
Well Services
|
| | | | | | | | | | | |
| Years Ended December 31, |
Reconciliation of Adjusted EBITDA to net income (loss): | 2016 | | 2015 | | 2014 |
Net (loss) income | $ | (62,197,372 | ) | | $ | (8,483,700 | ) | | $ | 4,803,247 |
|
Depreciation and amortization | 5,127,879 |
| | 5,696,547 |
| | 4,768,024 |
|
Impairment of long-lived assets | 1,384,751 |
| | 88,247 |
| | — |
|
One-time IPO compensation charges | 35,640 |
| | — |
| | — |
|
Equity based compensation | 43,073 |
| | — |
| | 53,807 |
|
Interest expense | 134,007 |
| | 429,061 |
| | 831,508 |
|
Other (income) expense, net | (565,966 | ) | | 686,617 |
| | 777,382 |
|
Provision for income taxes | 50,265,203 |
| | 4,454 |
| | 18,226 |
|
Adjusted EBITDA | $ | (5,772,785 | ) | | $ | (1,578,774 | ) | | $ | 11,252,194 |
|
Natural Sand Proppant Services
|
| | | | | | | | | | | |
| Years Ended December 31, |
Reconciliation of Adjusted EBITDA to net income (loss): | 2016 | | 2015 | | 2014 |
Net (loss) income | $ | (564,425 | ) | | $ | 524,182 |
| | $ | 280,782 |
|
Depreciation and amortization | 4,078,844 |
| | 4,200,809 |
| | 3,867,024 |
|
Impairment of long-lived assets | — |
| | 1,904,981 |
| | — |
|
One-time IPO compensation charges | 33,150 |
| | — |
| | — |
|
Equity based compensation | 57,441 |
| | — |
| | (24,856 | ) |
Interest income | — |
| | (98,056 | ) | | (208,519 | ) |
Interest expense | 49,518 |
| | 51,476 |
| | 312,467 |
|
Other expense (income), net | 2,321 |
| | (88,976 | ) | | 1,099,284 |
|
Provision for income taxes | 3,716 |
| | — |
| | 4,826 |
|
Adjusted EBITDA | $ | 3,660,565 |
| | $ | 6,494,416 |
| | $ | 5,331,008 |
|
Contract Land and Directional Drilling Services
|
| | | | | | | | | | | |
| Years Ended December 31, |
Reconciliation of Adjusted EBITDA to net income (loss): | 2016 | | 2015 | | 2014 |
Net loss | $ | (30,366,202 | ) | | $ | (30,401,338 | ) | | $ | (7,300,562 | ) |
Depreciation and amortization | 21,512,117 |
| | 24,626,705 |
| | 21,319,617 |
|
Impairment of long-lived assets | 347,547 |
| | 8,917,240 |
| | — |
|
One-time IPO compensation charges | 963,660 |
| | — |
| | — |
|
Equity based compensation | 110,307 |
| | — |
| | 3,935,902 |
|
Interest expense | 2,828,753 |
| | 2,890,130 |
| | 3,194,061 |
|
Other expense, net | 247,620 |
| | 1,121,093 |
| | 1,539,279 |
|
Provision (benefit) for income taxes | — |
| | (184,523 | ) | | 77,576 |
|
Adjusted EBITDA | $ | (4,356,198 | ) | | $ | 6,969,307 |
| | $ | 22,765,873 |
|
Other Energy Services
|
| | | | | | | | | | | |
| Years Ended December 31, |
Reconciliation of Adjusted EBITDA to net income (loss): | 2016 | | 2015 | | 2014 |
Net income | $ | 9,325,498 |
| | $ | 16,708,678 |
| | $ | 286,756 |
|
Depreciation and amortization | 2,179,116 |
| | 2,141,106 |
| | 1,656,928 |
|
One-time IPO compensation charges | 66,560 |
| | — |
| | — |
|
Equity based compensation | 114,000 |
| | — |
| | (126,011 | ) |
Interest income | — |
| | (436 | ) | | (5,622 | ) |
Interest expense | 100,032 |
| | 60,959 |
| | 63,420 |
|
Other expense, net | 37,043 |
| | 372,141 |
| | 563,856 |
|
Provision (benefit) for income taxes | 3,615,952 |
| | (1,481,452 | ) | | 7,402,669 |
|
Adjusted EBITDA | $ | 15,438,201 |
| | $ | 17,800,996 |
| | $ | 9,841,996 |
|
Liquidity and Capital Resources
We require capital to fund ongoing operations, including maintenance expenditures on our existing fleet and equipment, organic growth initiatives, investments and acquisitions. Since November 2014, our primary sources of liquidity have been cash on hand, borrowings under our revolving credit facility and cash flows from operations in addition to our proceeds from our initial public offering. Our primary use of capital has been for investing in property and equipment used to provide our services.
As of December 31, 2016, our revolving credit facility was undrawn, leaving an aggregate of $146.2 million, of available borrowing capacity under this facility.
The following table summarizes our liquidity as of the dates indicated:
|
| | | | | | | |
| December 31, |
| 2016 | | 2015 |
Cash and cash equivalents | $ | 28,693,985 |
| | $ | 3,074,072 |
|
Revolving credit facilities availability | 146,181,002 |
| | 141,550,112 |
|
Less borrowings | — |
| | (95,000,000 | ) |
Less letter of credit facilities (rail car commitments) | (2,090,560 | ) | | (1,930,560 | ) |
Less letter of credit facilities (insurance programs) | (1,285,000 | ) | | (1,176,000 | ) |
Net working capital (less cash) | 28,323,882 |
| | 22,276,591 |
|
Total | $ | 199,823,309 |
| | $ | 68,794,215 |
|
Liquidity and Cash Flows
The following table sets forth our cash flows for the periods indicated:
|
| | | | | | | | | |
| Years Ended December 31, |
| 2016 | 2015 | 2014 |
Net cash provided by operating activities | $ | 28,101,652 |
| $ | 68,392,616 |
| $ | 8,247,714 |
|
Net cash used in investing activities | (7,295,817 | ) | (24,834,909 | ) | (101,564,915 | ) |
Net cash provided by (used in) financing activities | 4,659,841 |
| (55,931,472 | ) | 103,125,751 |
|
Effect of foreign exchange rate on cash | 154,237 |
| (226,655 | ) | (2,418,289 | ) |
Net change in cash | $ | 25,619,913 |
| $ | (12,600,420 | ) | $ | 7,390,261 |
|
Operating Activities
Net cash provided by operating activities was $28.1 million, $68.4 million and $8.2 million, respectively, for the years ended December 31, 2016, 2015 and 2014. The decrease in operating cash flows from 2015 to 2016 was primarily attributable to the decrease in net income. The increase from 2014 to 2015 was primarily attributable to positive operating income generated by our pressure pumping services as well as cash generated by working capital changes. The cash generated from working capital changes was primarily attributable to the collection of receivables.
Investing Activities
Net cash used in investing activities was $7.3 million, $24.8 million and $101.6 million, respectively, for the years ended December 31, 2016, 2015 and 2014. Substantially all cash used in investing activities was used to purchase property and equipment that is utilized to provide our services.
The following table summarizes our capital expenditures by operating division for the periods indicated:
|
| | | | | | | | | |
| Years Ended December 31, |
| 2016 | 2015 | 2014 |
Pressure pumping services | $ | 7,673,187 |
| $ | 4,169,678 |
| $ | 180,466 |
|
Well services | 404,612 |
| 6,768,143 |
| 11,441,285 |
|
Natural sand proppant production | 106,252 |
| 171,202 |
| 4,587,464 |
|
Contract and directional drilling services | 2,709,478 |
| 12,650,831 |
| 85,801,345 |
|
Other energy services | 424,380 |
| 2,491,821 |
| 9,679,496 |
|
Net change in cash | $ | 11,317,909 |
| $ | 26,251,675 |
| $ | 111,690,056 |
|
Financing Activities
Net cash provided by (used in) financing activities was $4.7 million, $(55.9) million and $103.1 million for the years ended December 31, 2016, 2015 and 2014, respectively. In 2016, net cash provided by financing activities was primarily attributable to net repayments of $98.4 million under our revolving credit facility and net proceeds of $103.1 million from the IPO. In 2015, net cash used in financing activities was primarily attributable to net borrowings under our revolving credit facility. In 2014, net cash provided by financing activities was primarily attributable to net borrowings of $53.7 million and capital contributions of $51.8 million partially offset by $2.4 million in debt issuance costs.
Effect of Foreign Exchange Rate on Cash
The effect of foreign exchange rate on cash was $0.1 million, $(0.3) million and $(2.3) million for the years ended December 31, 2016, 2015 and 2014, respectively. The year-over-year effect was driven primarily by a favorable (unfavorable) shift in the weakness (strength) of the Canadian dollar relative to the U.S. dollar for the cash held in Canadian accounts.
Working Capital
Our working capital totaled $57.0 million and $25.4 million at December 31, 2016 and 2015, respectively. Our cash balances totaled $28.7 million and $3.1 million at December 31, 2016 and 2015, respectively.
Our Revolving Credit Facility
On November 25, 2014, we entered into a $170.0 million revolving credit and security agreement with PNC Capital Markets LLC, as lead arranger, PNC Bank, National Association, as the administrative and collateral agent, and the lenders from time-to-time party thereto. Our revolving credit facility, as amended in connection with the IPO, matures on November 25, 2019. Borrowings under our revolving credit facility are secured by our and our subsidiaries’ assets. The maximum availability for future borrowings under our revolving credit facility is subject to a borrowing base calculation prepared monthly. Concurrent with our entry into our revolving credit facility, we repaid all of our then existing subordinate debt with the initial advance under our revolving credit facility.
Interest is payable monthly at a base rate set by the institution’s commercial lending group plus an applicable margin. Additionally, at our request, outstanding balances, are permitted to be converted to LIBOR rate plus applicable margin tranches at set increments of $500,000. The LIBOR rate option allows us to select interest periods from one, two, and three or six months. The applicable margin for either the base rate or the LIBOR rate option can vary from 1.5% to 3.0%, based upon a calculation of the excess availability of the line as a percentage of the maximum credit limit.
We used a portion of the net proceeds from the IPO to repay all borrowings outstanding under our revolving credit facility and at February 21, 2017 our credit facility remained undrawn with availability of $142.6 million, net of outstanding letters of credit.
Our revolving credit facility contains various customary affirmative and restrictive covenants. Among the covenants are two financial covenants, including a minimum interest coverage ratio (3.0 to 1.0), and a maximum leverage ratio (4.0 to 1.0), and minimum availability ($10.0 million). As of December 31, 2016 and 2015, we were in compliance with these covenants.
Capital Requirements and Sources of Liquidity
As a result of the decline in drilling and completion activity, we reduced our capital expenditures in 2015 and have further reduced our capital expenditures in 2016. During 2016, our capital expenditures included $7.7 million on our pressure pumping services division primarily for pressure pumping equipment, $2.7 million in our contract land and directional drilling services division primarily for upgrades to our rig fleet, $0.4 million in our other energy services division primarily for an intersection upgrade, $0.4 million in our well services division primarily for upgrades on a coil tubing unit and $0.1 million in our natural sand proppant services division for a conveyor.
With commodity prices beginning to increase in the second half of 2016 and then stabilizing at their current range, we have seen an increase in customer demand, particularly in our pressure pumping and natural sand proppant services divisions. We have increased our capital budget accordingly and, during 2017, we currently estimate that our aggregate capital expenditures will be approximately $120.0 million. These capital expenditures include $66.0 million in our pressure pumping services division for the acquisition of an additional 132,500 horsepower of new high pressure hydraulic pumps and related equipment, $29.0 million in our pressure pumping service division for tractors, pneumatic trailers and transload facilities to enhance our last mile solutions, $9.0 million in our contract land and directional drilling services division for an upgrade to two of our horizontal rigs and $16.0 million in our well services and other energy services divisions, primarily to maintain our coil tubing and flowback services lines and add new service offerings.
We believe that our cash on hand, operating cash flow and available borrowings under our revolving credit facility will be sufficient to fund our operations for at least the next twelve months. However, future cash flows are subject to a number of variables, and significant additional capital expenditures could be required to conduct our operations. There can be no assurance that operations and other capital resources will provide cash in sufficient amounts to maintain planned or future levels of capital expenditures. Further, as previously announced, we intend to actively pursue an acquisition strategy to enhance our portfolio of products and services, market positioning and/or geographic presence. We regularly evaluate acquisition opportunities, and the number of opportunities coming to our attention has increased substantially since the IPO. We do not have a specific acquisition budget for 2017 since the timing and size of acquisitions cannot be accurately forecasted, however, we continue to evaluate opportunities, including transactions involving entities controlled by Wexford and Gulfport. Our acquisitions may be undertaken with cash, our common stock or a combination of cash, common stock and/or other consideration. In the event we make one or more acquisitions and the amount of capital required is greater than the amount we have available for acquisitions at that time, we could be required to reduce the expected level of capital expenditures and/or seek additional capital. If we seek additional capital for that or other reasons, we may do so through borrowings under our revolving credit facility, joint venture partnerships, asset sales, offerings of debt or equity securities or other means. We cannot assure you that this additional capital will be available on acceptable terms or at all. If we are unable to obtain funds we need, we may not be able to complete acquisitions that may be favorable to us or finance the capital expenditures necessary to conduct our operations.
Contractual and Commercial Commitments
The following table summarizes our contractual obligations and commercial commitments as of December 31, 2016:
|
| | | | | | | | | | | | | | | | | | | |
| Total | | Less than 1 year | | 1-3 Years | | 3-5 Years | | More than 5 Years |
Contractual obligations: | | | | | | | | | |
Long-term debt (1) | $ | — |
| | $ | — |
| | $ | — |
| | $ | — |
| | $ | — |
|
Interest and commitment fees on long-term debt (2) | 1,587,466 |
| | 548,179 |
| | 1,039,287 |
| | — |
| | — |
|
Operating lease obligations (3) | 14,059,375 |
| | 3,028,467 |
| | 4,257,573 |
| | 2,785,606 |
| | 3,987,729 |
|
Purchase commitment to sand suppliers (4) | 2,200,000 |
| | 2,200,000 |
| | — |
| | — |
| | — |
|
Purchase commitments to equipment manufacturers (5) | 18,554,769 |
| | 18,554,769 |
| | — |
| | — |
| | — |
|
| $ | 36,401,610 |
| | $ | 24,331,415 |
| | $ | 5,296,860 |
| | $ | 2,785,606 |
| | $ | 3,987,729 |
|
| |
(1) | The long-term debt excludes interest payments on each obligation. |
| |
(2) | Assumption of no long-term debt balance; future charges relate to commitment fees on credit facility. |
| |
(3) | Operating lease obligations relate to real estate, rail cars and other equipment. |
| |
(4) | The purchase commitment to a sand supplier represents our annual obligation to purchase a minimum amount of sand. |
| |
(5) | Obligations arising from capital improvements/equipment purchases. |
Off-Balance Sheet Arrangements
Operating Leases
The Company leases real estate, rail cars and other equipment under long-term operating leases with varying terms and expiration dates through 2025. Aggregate future minimum lease payments under these non-cancelable operating leases in effect at December 31, 2016 are as follows:
|
| | | | |
Year ended December 31: | | Amount |
2017 | | $ | 3,028,467 |
|
2018 | | 2,339,084 |
|
2019 | | 1,918,489 |
|
2020 | | 1,392,803 |
|
2021 | | 1,392,803 |
|
Thereafter | | 3,987,729 |
|
| | $ | 14,059,375 |
|
Other Commitments
We entered into a purchase agreement in 2014 with a sand supplier to begin January 1, 2015 and end December 31, 2016. We are subject to an annual commitment of 200,000 tons of sand. During June 2016, we paid a deposit of $0.6 million to the sand supplier to be netted against future purchases of sand under this contract and deferred the commitment until 2017. We have one additional unilateral option to extend for one additional year with a further deposit of $0.6 million. As of December 31, 2016, the future commitment for 2017 under this agreement was $2.2 million.
In the fourth quarter of 2016, we entered into agreements to acquire new high pressure fracturing units and other capital equipment. The future commitments under these agreements was $18.6 million as of December 31, 2016. Subsequently, in February 2017, we ordered additional new high pressure fracturing units with nameplate capacity of 57,500 horsepower and related equipment. The aggregate cost of the February 2017 commitments was $35.2 million. Additionally, subsequent to December 31, 2016, we ordered $6.4 million in other equipment for our natural sand proppant and contract land and directional drilling service segments.
Subsequent to December 31, 2016, we entered into railcar lease agreements with aggregate commitments of $2.0 million.
Critical Accounting Policies and Estimates
The discussion and analysis of our financial condition and results of operations are based upon our combined financial statements, which have been prepared in accordance with accounting principles generally accepted in the United States. Below, we have provided expanded discussion of our more significant accounting policies, estimates and judgments. We believe these accounting policies reflect our more significant estimates and assumptions used in preparation of our financial statements. See Note 1 of our consolidated financial statements appearing elsewhere in this prospectus for a discussion of additional accounting policies and estimates made by management.
Use of Estimates. In preparing the financial statements, our management makes informed judgments and estimates that affect the reported amounts of assets and liabilities, the disclosure of contingent assets and liabilities at the date of the financial statements and reported amounts of revenues and expenses during the reporting period. Actual results could differ from those estimates. Significant estimates include but are not limited to the allowance for doubtful accounts, reserves for self-insurance, depreciation and amortization of property and equipment, amortization of intangible assets, and future cash flows and fair values used to assess recoverability and impairment of long-lived assets, including goodwill.
Revenue Recognition. We generate revenue from multiple sources within our five operating divisions. In all cases, revenue is recognized when services are performed, collection of the receivables is probable, persuasive evidence of an arrangement exists and the price is fixed and determinable. Services are sold without warranty or the right to return. Taxes assessed on revenue transactions are presented on a net basis and are not included in revenue. The specific revenue sources are outlined as follows:
Pressure Pumping Services Revenue. Pressure pumping services are typically provided based upon a purchase order, contract or on a spot market basis. Services are provided on a day rate, contracted or hourly basis, and revenue is recognized as the work progresses. Jobs for these services are typically short-term in nature and range from a few hours to multiple days. Revenue is recognized upon the completion of each day’s work based upon a completed field ticket, which includes the charges for the services performed, mobilization of the equipment to the location and the personnel involved in such services or mobilization. Additional revenue is generated through labor charges and the sale of consumable supplies that are incidental to the service being performed. The labor charges and the use of consumable supplies are reflected on completed field tickets.
Well Services Revenue. Well services are typically provided based upon a purchase order, contract, or on a spot market basis. Services are provided on a day rate, contracted, or hourly basis, and revenue is recognized as the work progresses. Jobs for these services are typically short-term in nature and range from a few hours to multiple days. Our equipment rental services are recognized upon completion of each day's work based on completed field ticket.
Natural Sand Proppant Services Revenue. Revenue from the sale of natural sand proppant is recognized according to the terms of title transfer on the sand. For proppant sold free on board plant, revenue is recognized when the sand is shipped. For proppant sold free on board destination, revenue is recognized when the sand reaches the customer specified transload facility or when the sand is loaded into a truck for last mile delivery depending on the specific terms of each sale.
Contract Land and Directional Drilling Services Revenue. Contract drilling services are provided under daywork or footage contracts, and revenue is recognized as the work progresses based on the days completed or the feet drilled, as applicable. Mobilization revenue and costs for daywork and footage contracts are recognized over the days of actual drilling. Directional drilling services are provided on a day rate or hourly basis, and revenue is recognized as work progresses. Proceeds from customers for the cost of oilfield downhole rental equipment that is involuntarily damaged or lost in-hole are reflected as revenues.
Other Energy Services Revenue. Revenue from our other energy services is recognized when rooms are occupied and services have been rendered. Advance deposits on rooms and special events are deferred until services are provided to the customer.
Revenues arising from claims for amounts billed in excess of the contract price or for amounts not included in the original contract are recognized when billed less any allowance for uncollectibility. Revenue from such claims is only recognized if it is probable that the claim will result in additional revenue, the costs for the additional services have been incurred, management believes there is a legal basis for the claim and the amount can be reliably estimated. Revenues from such claims are recorded only to the extent that contract costs relating to the claims have been incurred. Historically, we have not billed any customer for amounts not included in the original contract.
The timing of revenue recognition may differ from contract billing or payment schedules, resulting in revenues that have been earned but not billed (“unbilled revenue”) or amounts that have been billed, but not earned (“deferred revenue”).
Allowance for Doubtful Accounts. We regularly review receivables and provide for estimated losses through an allowance for doubtful accounts. In evaluating the level of established reserves, we make judgments regarding our customers’ ability to make required payments, economic events and other factors. As the financial condition of customers change, circumstances develop or additional information becomes available, adjustments to the allowance for doubtful accounts may be required. In the event we were to determine that a customer may not be able to make required payments, we would increase the allowance through a charge to income in the period in which that determination is made. Uncollectable accounts receivable are periodically charged against the allowance for doubtful accounts once final determination is made of their uncollectibility.
Depreciation and Amortization. In order to depreciate and amortize our property and equipment, we estimate useful lives, attrition factors and salvage values of these items. Our estimates may be affected by such factors as changing market conditions, technological advances in the industry or changes in regulations governing the industry.
Impairment of Long-Lived Assets. Long-lived assets are reviewed for impairment when events or changes in circumstances indicate that the carrying amount of such assets may not be recoverable. Recoverability of such assets is evaluated by measuring the carrying amount of the assets against the estimated undiscounted future cash flows associated with the assets. If such evaluations indicate that the future undiscounted cash flow from the assets is not sufficient to recover the carrying value of such assets, the assets are adjusted to their estimated fair values.
Goodwill. Goodwill is tested for impairment annually, or more frequently if events or changes in circumstances indicate that goodwill might be impaired. The impairment test is a two-step process. First, the fair value of each reporting unit is compared to its carrying value to determine whether an indication of impairment exists. If impairment is indicated, then the implied value of the reporting unit’s goodwill is determined by allocating the unit’s fair value to its assets and liabilities as if the reporting unit had been acquired in a business combination. The fair value of the reporting unit is determined using the discounted cash flow approach, excluding interest. The impairment for goodwill is measured as the excess of its carrying value over its implied value.
Share-based Compensation. The share-based compensation program consists of restricted stock units granted to employees and restricted stock units granted to non-employee directors under the Mammoth Energy Services, Inc. 2016 Incentive Plan (the "2016 Plan"). The Company recognizes in its financial statements the cost of employee services received in exchange for restricted stock based on the fair value of the equity instruments as of the grant date. In general, this value is amortized over the vesting period; for grants with a non-substantive service condition, this value is recognized immediately. Amounts are recognized in selling, general, and administrative expenses.
Income Taxes. Prior to our IPO, the Partnership and each of its subsidiaries, except Great White Sand Tiger Lodging Ltd., which we refer to as Lodging, was treated as a pass-through entity for federal income tax and most state income tax purposes. Accordingly, income taxes on net earnings were payable by the stockholders, members or partners and are not reflected in the historical financial statements. In connection with our IPO, we became a C corporation subject to federal income taxes, which triggered the recognition of federal income tax liabilities associated with historical earnings. See Notes 1 and 2 to our consolidated financial statements included elsewhere in this annual report for more information. Lodging is subject to corporate income taxes and they are provided in the financial statements based upon Financial Accounting Standards Board, Accounting Standard Codification 740 Income Taxes. As such, deferred tax assets and liabilities are recognized for the future tax consequences attributable to differences between the financial statement carrying amounts of existing assets and liabilities and their respective tax bases. Deferred tax assets and liabilities are measured using statutory tax rates expected to apply to taxable income in the years in which those temporary differences are expected to be recovered or settled. The effect of deferred tax assets and liabilities as a result of a change in tax rate is recognized in the period that includes the statutory enactment date. A valuation allowance for deferred tax assets is recognized when it is more likely than not that the benefit of deferred tax assets will not be realized.
New Accounting Pronouncements
In November 2015, the Financial Accounting Standards Board, or ("FASB"), issued Accounting Standards Update, or ("ASU"), No. 2015-17, "Income Taxes," which simplifies the presentation of deferred income taxes by requiring deferred tax liabilities and assets be classified as noncurrent in the balance sheet. ASU 2015-17 is effective for annual and interim reporting periods beginning after December 15, 2016, with early adoption permitted. The effect of the adoption is discussed in Note 2 to our consolidated financial statements included elsewhere in this annual report.
In July 2015, the FASB issued ASU No. 2015-11, “Inventory (Topic 330): Simplifying the Measurement of Inventory,” which changes inventory measured using any method other than last-in, first-out ("LIFO") or the retail inventory method (for example, inventory measured using first-in, first-out (FIFO) or average cost) at the lower of cost and net realizable value. ASU 2015-11 is effective for annual and interim reporting periods beginning after December 15, 2016, with early adoption permitted. We do not expect the adoption of this guidance to have a material effect on our consolidated financial statements.
In May 2014, the FASB issued ASU 2014-09, “Revenue from Contracts with Customers.” ASU 2014-09 supersedes existing revenue recognition requirements in Generally Accepted Accounting Principles ("GAAP") and requires an entity to recognize revenue when it transfers promised goods or services to customers in an amount that reflects the consideration to which the entity expects to be entitled to in exchange for those goods or services. Additionally, it requires expanded disclosures regarding the nature, amount, timing, and certainty of revenue and cash flows from contracts with customers. The ASU was effective for annual and interim reporting periods beginning after December 15, 2016, using either a full or a modified retrospective application approach; however, in July 2015 the FASB decided to defer the effective date by one year (until 2018) by issuing ASU No. 2015-14, "Revenue From Contracts with Customers: Deferral of the Effective Date." The Company expects to adopt this new revenue guidance utilizing the retrospective method of adoption in the first quarter of 2018, and because the Company is still evaluating the portion of its revenues that may be subject to the new leasing guidance discussed below, it is unable to quantify the impact that the new revenue standard will have on the Company’s consolidated financial statements upon adoption.
In February 2016, the FASB issued ASU No, 2016-2 “Leases” amending the current accounting for leases. Under the new provisions, all lessees will report a right-of-use asset and a liability for the obligation to make payments for all leases with the exception of those leases with a term of 12 months or less. All other leases will fall into one of two categories: (i) a financing lease or (ii) an operating lease. Lessor accounting remains substantially unchanged with the exception that no leases entered into after the effective date will be classified as leveraged leases. For sale leaseback transactions, a sale will only be recognized if the criteria in the new revenue recognition standard are met. ASU 2016-2 is effective for fiscal years beginning after December 15, 2018, and interim periods within that fiscal year. Early adoption is permitted. Since a portion of the Company’s revenue may be subject to this new leasing guidance, it expects to adopt this updated leasing guidance at the same time its adopts the new revenue standard discussed above, utilizing the retrospective method of adoption. This new leasing guidance will also impact the Company in situations where it is the lessee, and in certain circumstances it will have a right-of-use asset and lease liability on its consolidated financial statements. We are currently evaluating the effect the new guidance will have on our consolidated financial statements and results of operations.
Item 7A. Quantitative and Qualitative Disclosures About Market Risk
The demand, pricing and terms for oil and gas services provided by us are largely dependent upon the level of activity for the U.S. oil and natural gas industry. Industry conditions are influenced by numerous factors over which we have no control, including, but not limited to: the supply of and demand for oil and natural gas; the level of prices, and expectations about future prices of oil and natural gas; the cost of exploring for, developing, producing and delivering oil and natural gas; the expected rates of declining current production; the discovery rates of new oil and natural gas reserves; available pipeline and other transportation capacity; weather conditions; domestic and worldwide economic conditions; political instability in oil-producing countries; environmental regulations; technical advances affecting energy consumption; the price and availability of alternative fuels; the ability of oil and natural gas producers to raise equity capital and debt financing; and merger and divestiture activity among oil and natural gas producers.
The level of activity in the U.S. oil and natural gas exploration and production industry is volatile. Expected trends in oil and natural gas production activities may not continue and demand for our services may not reflect the level of activity in the industry. Any prolonged substantial reduction in oil and natural gas prices would likely affect oil and natural gas production levels and therefore affect demand for our services. A material decline in oil and natural gas prices or U.S. activity levels could have a material adverse effect on our business, financial condition, results of operations and cash flows. Recently, demand for our services has been strong and we are continuing our past practice of committing our equipment on a short-term or day-to-day basis.
Interest Rate Risk
We had a cash and cash equivalents balance of $28.7 million at December 31, 2016. We do not enter into investments for trading or speculative purposes. We do not believe that we have any material exposure to changes in the fair value of these investments as a result of changes in interest rates. Declines in interest rates, however, will reduce future income.
At December 31, 2016, our revolving credit facility was undrawn and no borrowings were outstanding. On October 19, 2016, immediately prior to the closing of the IPO, we had $78.1 million outstanding under this facility with weighted average interest rate of 3.51%. A 1% increase or decrease in the interest rate at that time would have increased or decreased our interest expense by approximately $0.8 million per year. We do not currently hedge our interest rate exposure.
Foreign Currency Risk
Our energy services business generates revenue and incurs expenses that are denominated in the Canadian dollar. These transactions could be materially affected by currency fluctuations. Changes in currency exchange rates could adversely affect our consolidated results of operations or financial position. We also maintain cash balances denominated in the Canadian dollar. At December 31, 2016, we had $5.6 million of cash in Canadian accounts. A 10% increase in the strength of the Canadian dollar versus the U.S. dollar would have resulted in an increase in pre-tax income of approximately $0.9 million as of December 31, 2016. Conversely, a corresponding decrease in the strength of the Canadian dollar would have resulted in a comparable decrease in pre-tax income. We have not hedged our exposure to changes in foreign currency exchange rates and, as a result, could incur unanticipated translation gains and losses.
Seasonality
We provide completion and production services as well as contract land and drilling services primarily in the Utica, Permian Basin, Eagle Ford, Marcellus, Granite Wash, Cana Woodford and Cleveland sand resource plays located in the continental U.S. We also provide other energy services in the oil sands in Alberta, Canada. We serve these markets through our facilities and service centers that are strategically located to serve resource plays in Ohio, Oklahoma, Wisconsin, Minnesota, and Alberta, Canada. For the years ended December 31, 2016 and 2015, we generated approximately 84% and 72%, respectively, of our revenue from our operations in Ohio, Wisconsin, Minnesota, Pennsylvania, West Virginia and Canada where weather conditions may be severe. As a result, our operations may be limited or disrupted, particularly during winter and spring months, in these geographic regions, which would have a material adverse effect on our financial condition and results of operations. Our operations in Oklahoma and Texas are generally not affected by seasonal weather conditions.
Inflation
Inflation in the United States has been relatively low in recent years and did not have a material impact on our results of operations for the years ended 2016 and 2015. Although the impact of inflation has been insignificant in recent years, it is still a factor in the United States economy and we tend to experience inflationary pressure on the cost of oilfield services and equipment as increasing oil and gas prices increase drilling activity in our areas of operations.
Item 8. Financial Statements and Supplementary Data
The information required by this item appears beginning on page F-1 following the signature pages of this report.
Item 9. Changes in and Disagreements with Accountants on Accounting and Financial Disclosure
Not applicable.
Item 9A. Controls and Procedures
Evaluation of Disclosure Control and Procedures
Under the direction of our Chief Executive Officer and Chief Financial Officer, we have established disclosure controls and procedures, as defined in Rule 13a-15(e) and 15d-15(e) under the Exchange Act, that are designed to ensure that information required to be disclosed by us in the reports that we file or submit under the Exchange Act is recorded, processed, summarized and reported within the time periods specified in the SEC’s rules and forms. The disclosure controls and procedures are also intended to ensure that such information is accumulated and communicated to management, including our Chief Executive Officer and Chief Financial Officer, as appropriate to allow timely decisions regarding required disclosures. In designing and evaluating the disclosure controls and procedures, management recognizes that any controls and procedures, no matter how well designed and operated, can provide only reasonable assurance of achieving the desired control objectives. In addition, the design of disclosure controls and procedures must reflect the fact that there are resource constraints and that management is required to apply judgment in evaluating the benefits of possible controls and procedures relative to their costs.
As of December 31, 2016, an evaluation was performed under the supervision and with the participation of management, including our Chief Executive Officer and Chief Financial Officer, of the effectiveness of the design and operation of our disclosure controls and procedures pursuant to Rule 13a-15(b) under the Exchange Act. Based upon our evaluation, our Chief Executive Officer and Chief Financial Officer have concluded that as of December 31, 2016, our disclosure controls and procedures are effective.
Management’s Annual Report on Internal Control Over Financial Reporting and Attestation Report of the Registered Public Accounting Firm
This Annual Report on Form 10-K does not include a report of management’s assessment regarding internal control over financial reporting due to a transition period established by rules of the Securities and Exchange Commission for newly public companies.
Further, our independent registered public accounting firm is not yet required to formally attest to the effectiveness of our internal controls over financial reporting, and will not be required to do so for as long as we are an “emerging growth company” pursuant to the provisions of the Jumpstart Our Business Startups Act of 2012 or as long as we are a non-accelerated filer.
Changes in Internal Controls Over Financial Reporting
There was no change in our internal control over financial reporting (as defined in Rules 13a-15(d) and 15d-15(d) under the Exchange Act) that occurred during the quarter ended December 31, 2016 that has materially affected, or is reasonably likely to materially affect, our internal control over financial reporting.
Item 9B. Other Information
Not applicable.
PART III.
Item 10. Directors, Executive Officers and Corporate Governance
Information required by Item 10 of Part III is incorporated herein by reference to the definitive Proxy Statement to be filed by us pursuant to Regulation 14A of the General Rules and Regulations under the Securities Exchange Act of 1934 within 120 days after the close of the year ended December 31, 2016.
We have adopted a Code of Business Conduct and Ethics that applies to our Chief Executive Officer, Chief Financial Officer, principal accounting officer and controller and persons performing similar functions. The Code of Business Conduct and Ethics is posted on our website at http://ir.mammothenergy.com/corporate-governance.cfm. We intend to satisfy the disclosure requirements under Item 5.05 of Form 8-K regarding an amendment to, or waiver from, a provision of the Code of Business Conduct and Ethics by posting such information on our website at the address specified above.
Item 11. Executive Compensation
The information required by Item 11 of Part III is incorporated by reference to our definitive Proxy Statement within 120 days after the close of the year ended December 31, 2016.
Item 12. Security Ownership of Certain Beneficial Owners and Management and Related Stockholder Matters
The information required by Item 12 of Part III is incorporated by reference to our definitive Proxy Statement within 120 days after the close of the year ended December 31, 2016.
Item 13. Certain Relationships and Related Transactions and Director Independence
The information required by Item 13 of Part III is incorporated by reference to our definitive Proxy Statement within 120 days after the close of the year ended December 31, 2016.
Item 14. Principal Accountant Fees and Services
The information required by Item 14 of Part III is incorporated by reference to our definitive Proxy Statement within 120 days after the close of the year ended December 31, 2016.
PART IV.
Item 15. Exhibits, Financial Statement Schedules
The following documents are filed as part of this report or incorporated by reference herein:
(1) Financial Statements
Reference is made to the Index to Financial Statements appearing on Page F-1. Reference is also made to the Financial Statements of Mammoth Energy Services, Inc. (“Mammoth”) that have been included on pages F-1 to F-30 in Mammoth's Annual Report on Form 10-K (File No. 001-37917) filed with the SEC on February 23, 2017, as such Annual Report on Form 10-K may be amended from time to time, which Financial Statements are incorporated herein by reference.
(2) Financial Statement Schedules
All financial statement schedules have been omitted because they are not applicable or the required disclosure is presented in the financial statements or notes thereto.
(3) Exhibits
The Exhibit Index beginning on page E-1 of this report is incorporated herein by reference.
Signatures
Pursuant to the requirements of the Securities Exchange Act of 1934, the registrant has duly caused this report to be signed on its behalf by the undersigned thereunto duly authorized.
|
| | | | | |
| | | | | MAMMOTH ENERGY SERVICES, INC. |
Date: | February 23, 2017 | | By: | | /s/ Mark Layton |
| | | | | Mark Layton |
| | | | | Chief Financial Officer |
| | | | | |
| | | | | |
Pursuant to the requirements of the Securities and Exchange Act of 1934, this report has been signed below by the following persons on behalf of the Registrant and in the capacities and on the dates indicated.
|
| | |
Signature | Title | Date |
/s/ Arty Straehla | Chief Executive Officer (principal executive officer) | February 23, 2017 |
Arty Straehla | |
| | |
/s/ Mark Layton | Chief Financial Officer (principal financial and accounting officer) | February 23, 2017 |
Mark Layton | |
| | |
/s/ Marc McCarthy | Director (Chairman of the Board) | February 23, 2017 |
Marc McCarthy | | |
| | |
/s/ Paul K. Heerwagen IV | Director | February 23, 2017 |
Paul K. Heerwagen IV | | |
| | |
/s/ Matthew Ross | Director | February 23, 2017 |
Matthew Ross | | |
| | |
/s/ Arthur Smith | Director | February 23, 2017 |
Arthur Smith | | |
| | |
/s/ André Weiss | Director | February 23, 2017 |
André Weiss | | |
Report of Independent Registered Public Accounting Firm
Board of Directors and Shareholders
Mammoth Energy Services, Inc.
We have audited the accompanying consolidated balance sheets of Mammoth Energy Services, Inc. (a Delaware corporation) and subsidiaries (the Company) as of December 31, 2016 and 2015, and the related consolidated statements of comprehensive loss, changes in equity, and cash flows for each of the three years in the period ended December 31, 2016. These financial statements are the responsibility of the Company’s management. Our responsibility is to express an opinion on these financial statements based on our audits.
We conducted our audits in accordance with the standards of the Public Company Accounting Oversight Board (United States). Those standards require that we plan and perform the audit to obtain reasonable assurance about whether the financial statements are free of material misstatement. We were not engaged to perform an audit of the Company’s internal control over financial reporting. Our audits included consideration of internal control over financial reporting as a basis for designing audit procedures that are appropriate in the circumstances, but not for the purpose of expressing an opinion on the effectiveness of the Company’s internal control over financial reporting. Accordingly, we express no such opinion. An audit also includes examining, on a test basis, evidence supporting the amounts and disclosures in the financial statements, assessing the accounting principles used and significant estimates made by management, as well as evaluating the overall financial statement presentation. We believe that our audits provide a reasonable basis for our opinion.
As discussed in Note 2 to the consolidated financial statements, the Company adopted new accounting guidance in 2016 and 2015 related to the presentation of deferred income taxes.
In our opinion, the consolidated financial statements referred to above present fairly, in all material respects, the financial position of Mammoth Energy Services, Inc. and subsidiaries as of December 31, 2016 and 2015, and the results of their operations and their cash flows for each of the three years in the period ended December 31, 2016 in conformity with accounting principles generally accepted in the United States of America.
/s/GRANT THORNTON LLP
Oklahoma City, Oklahoma
February 23, 2017
MAMMOTH ENERGY SERVICES, INC.
CONSOLIDATED BALANCE SHEETS
|
| | | | | | | | |
ASSETS | | December 31, |
| | 2016 | | 2015 |
CURRENT ASSETS | | | | |
Cash and cash equivalents | | $ | 28,693,985 |
| | $ | 3,074,072 |
|
Accounts receivable, net | | 20,602,962 |
| | 17,797,852 |
|
Receivables from related parties | | 28,059,565 |
| | 25,643,781 |
|
Inventories | | 4,355,088 |
| | 4,755,661 |
|
Prepaid Expenses | | 4,254,148 |
| | 4,447,253 |
|
Other current assets | | 391,599 |
| | 422,219 |
|
Total current assets | | 86,357,347 |
| | 56,140,838 |
|
| | | | |
Property, plant and equipment, net | | 221,247,228 |
| | 273,026,665 |
|
Intangible assets, net - customer relationships | | 15,949,772 |
| | 24,309,772 |
|
Intangible assets, net - trade names | | 5,617,057 |
| | 6,328,057 |
|
Goodwill | | 86,043,148 |
| | 86,043,148 |
|
Other non-current assets | | 5,339,283 |
| | 5,137,090 |
|
Total assets | | $ | 420,553,835 |
| | $ | 450,985,570 |
|
| | | | |
LIABILITIES AND EQUITY | | | | |
CURRENT LIABILITIES | | | | |
Accounts payable | | $ | 18,480,325 |
| | $ | 16,046,378 |
|
Payables to related parties | | 2,434,031 |
| | 6,997,929 |
|
Accrued expenses and other current liabilities | | 8,396,968 |
| | 7,718,956 |
|
Income taxes payable | | 28,156 |
| | 26,912 |
|
Total current liabilities | | 29,339,480 |
| | 30,790,175 |
|
| | | | |
Long-term debt | | — |
| | 95,000,000 |
|
Deferred income taxes | | 47,670,789 |
| | 1,460,959 |
|
Other liabilities | | 2,501,886 |
| | 571,174 |
|
Total liabilities | | 79,512,155 |
| | 127,822,308 |
|
| | | | |
COMMITMENTS AND CONTINGENCIES (Note 16) | |
| |
|
| | | | |
EQUITY | | | | |
Equity: | | | | |
Common stock, $0.01 par value, 200,000,000 shares authorized, | | 375,000 |
| | — |
|
37,500,000 issued and outstanding at December 31, 2016; zero issued | | | | |
and outstanding at December 31, 2015 | | | | |
Additional paid in capital | | 400,205,921 |
| | — |
|
Accumulated Deficit | | (56,322,878 | ) | | — |
|
Common units, 30,000,000 units issued and outstanding | | | | |
at December 31, 2015; zero issued and outstanding at December 31, 2016 | | — |
| | 329,090,230 |
|
Accumulated other comprehensive loss | | (3,216,363 | ) | | (5,926,968 | ) |
Total equity | | 341,041,680 |
| | 323,163,262 |
|
Total liabilities and equity | | $ | 420,553,835 |
| | $ | 450,985,570 |
|
The accompanying notes are an integral part of these consolidated financial statements.
MAMMOTH ENERGY SERVICES, INC.
CONSOLIDATED STATEMENTS OF COMPREHENSIVE LOSS
|
| | | | | | | | | | | |
| Years Ended December 31, |
| 2016 | | 2015 | | 2014 |
REVENUE | | | | | |
Services revenue | $ | 89,642,899 |
| | $ | 172,012,405 |
| | $ | 182,341,309 |
|
Services revenue - related parties | 107,599,378 |
| | 132,674,989 |
| | 30,834,421 |
|
Product revenue | 5,433,141 |
| | 16,732,077 |
| | 36,859,731 |
|
Product revenue - related parties | 28,323,303 |
| | 38,517,222 |
| | 9,490,543 |
|
Total Revenue | 230,998,721 |
| | 359,936,693 |
| | 259,526,004 |
|
| | | | | |
COST AND EXPENSES | | | | | |
Services cost of revenue (1) | 139,807,987 |
| | 225,820,450 |
| | 150,482,793 |
|
Services cost of revenue - related parties | 5,575,092 |
| | 4,177,335 |
| | 1,770,565 |
|
Product cost of revenue (2) | 7,577,660 |
| | 25,838,555 |
| | 35,525,596 |
|
Product cost of revenue - related parties | 20,589,170 |
| | 20,510,977 |
| | 3,289,947 |
|
Selling, general and administrative | 15,836,165 |
| | 19,303,557 |
| | 14,272,986 |
|
Selling, general and administrative - related parties | 894,810 |
| | 1,237,991 |
| | 2,754,877 |
|
Depreciation and amortization | 69,910,858 |
| | 72,393,882 |
| | 35,627,165 |
|
Impairment of long-lived assets | 1,870,885 |
| | 12,124,353 |
| | — |
|
Total cost and expenses | 262,062,627 |
| | 381,407,100 |
| | 243,723,929 |
|
Operating (loss) income | (31,063,906 | ) | | (21,470,407 | ) | | 15,802,075 |
|
| | | | | |
OTHER (EXPENSE) INCOME | | | | | |
Interest income | — |
| | 98,492 |
| | 214,141 |
|
Interest expense | (3,711,457 | ) | | (5,290,821 | ) | | (4,603,595 | ) |
Interest expense - related parties | — |
| | — |
| | (184,479 | ) |
Other, net | 252,239 |
| | (2,157,764 | ) | | (5,724,496 | ) |
Total other expense | (3,459,218 | ) | | (7,350,093 | ) | | (10,298,429 | ) |
(Loss) income before income taxes | (34,523,124 | ) | | (28,820,500 | ) | | 5,503,646 |
|
Provision (benefit) for income taxes | 53,884,871 |
| | (1,589,086 | ) | | 7,514,194 |
|
Net loss | $ | (88,407,995 | ) | | $ | (27,231,414 | ) | | $ | (2,010,548 | ) |
| | | | | |
OTHER COMPREHENSIVE (LOSS) INCOME | | | | | |
Foreign currency translation adjustment (3) | 2,710,605 |
| | (4,814,819 | ) | | 472,714 |
|
Comprehensive loss | $ | (85,697,390 | ) | | $ | (32,046,233 | ) | | $ | (1,537,834 | ) |
| | | | | |
Net loss per share (basic and diluted) (Note 10) | $ | (2.81 | ) |
| $ | (0.91 | ) |
| $ | (0.10 | ) |
Weighted average number of shares outstanding (Note 10) | 31,500,000 |
|
| 30,000,000 |
|
| 21,056,073 |
|
|
|
| |
| | |
Pro Forma C Corporation Data (unaudited): | | |
| |
|
Net loss, as reported | $ | (88,407,995 | ) | | $ | (27,231,414 | ) | | $ | (2,010,548 | ) |
Taxes on income earned as a non-taxable entity (Note 9) | 13,750,827 |
| | 2,469,030 |
| | (5,207,628 | ) |
Taxes due to change to C corporation (Note 9) | 53,088,861 |
| | — |
| | — |
|
Pro forma net loss | $ | (21,568,307 | ) | | $ | (24,762,384 | ) | | $ | (7,218,176 | ) |
Basic and Diluted (Note 10) | $ | (0.58 | ) | | $ | (0.66 | ) | | $ | (0.34 | ) |
Weighted average pro forma shares outstanding—basic and diluted (Note 10) | 37,500,000 |
| | 37,500,000 |
| | 21,056,073 |
|
| | | | | |
(1) Exclusive of depreciation and amortization | 65,705,373 |
| | 68,053,581 |
| | 31,687,048 |
|
(2) Exclusive of depreciation and amortization | 4,072,674 |
| | 4,193,106 |
| | 3,859,150 |
|
(3) Net of tax | 1,731,887 |
| | — |
| | 298,170 |
|
The accompanying notes are an integral part of these consolidated financial statements.
MAMMOTH ENERGY SERVICES, INC.
CONSOLIDATED STATEMENTS OF CHANGES IN EQUITY
|
| | | | | | | | | | | | | | | | | | | | | | |
| | | | | | | | |
| | | | | | | | |
| Common Stock | Members' | | Common | Paid-In | | |
| Shares | Amount | Equity (2) | R-E (1) | Partners | Capital | AOCI (3) | Total |
Balance at January 1, 2014 | 100 |
| 1 |
| $ | 116,370,107 |
| $ | 5,928,873 |
| $ | — |
| $ | — |
| $ | (1,584,863 | ) | $ | 120,714,118 |
|
Capital contributions | — |
| — |
| 51,768,502 |
| — |
| — |
| — |
| — |
| 51,768,502 |
|
Equity based compensation through November 24, 2014 | — |
| — |
| 212,537 |
| — |
| — |
| — |
| — |
| 212,537 |
|
Dividends paid | — |
| — |
| — |
| (12,301 | ) | — |
| — |
| — |
| (12,301 | ) |
Net income through November 24, 2014 | — |
| — |
| 4,177,882 |
| 5,210,867 |
| — |
| — |
| — |
| 9,388,749 |
|
Contribution of predecessor interests for 20MM units (Note 1) | (100 | ) | (1 | ) | (172,529,028 | ) | (11,127,439 | ) | 180,465,348 |
| — |
| — |
| (3,191,120 | ) |
Acquisition of Stingray (Note 12) | — |
| — |
| — |
| — |
| 183,630,000 |
| — |
| — |
| 183,630,000 |
|
Equity based compensation from November 25, 2014 to December 31, 2014 | — |
| — |
| — |
| — |
| 3,626,304 |
| — |
| — |
| 3,626,304 |
|
Net loss from November 25, 2014 to December 31, 2014 | — |
| — |
| — |
| — |
| (11,399,297 | ) | — |
| — |
| (11,399,297 | ) |
Other comprehensive gain, net of tax | — |
| — |
| — |
| — |
| — |
| — |
| 472,714 |
| 472,714 |
|
Balance at December 31, 2014 | — |
| — |
| — |
| — |
| 356,322,355 |
| — |
| (1,112,149 | ) | 355,210,206 |
|
Net loss | — |
| — |
| — |
| — |
| (27,231,414 | ) | — |
| — |
| (27,231,414 | ) |
Capital distributions | — |
| — |
| — |
| — |
| (711 | ) | — |
| — |
| (711 | ) |
Other comprehensive income | — |
| — |
| — |
| — |
| — |
| — |
| (4,814,819 | ) | (4,814,819 | ) |
Balance at December 31, 2015 | — |
| — |
| — |
| — |
| 329,090,230 |
| — |
| (5,926,968 | ) | 323,163,262 |
|
Net loss prior to LLC conversion | — |
| — |
| — |
| — |
| (32,085,117 | ) | — |
| — |
| (32,085,117 | ) |
Equity based compensation | — |
| — |
| — |
| — |
| (18,683 | ) | — |
| — |
| (18,683 | ) |
LLC Conversion (Note 1) | — |
| — |
| — |
| — |
| (296,986,430 | ) | 296,986,430 |
| — |
| — |
|
Issuance of common stock at public offering, net of offering costs | 37,500,000 |
| 375,000 |
| — |
| — |
| — |
| 102,699,661 |
| — |
| 103,074,661 |
|
Stock-based compensation | — |
| — |
| — |
| — |
| — |
| 519,830 |
| — |
| 519,830 |
|
Net loss subsequent to LLC conversion | — |
| — |
| — |
| (56,322,878 | ) | | — |
| — |
| (56,322,878 | ) |
Other comprehensive income | — |
| — |
| — |
| — |
| — |
| — |
| 2,710,605 |
| 2,710,605 |
|
Balance at December 31, 2016 | 37,500,000 | 375,000 |
| — |
| (56,322,878 | ) | — |
| 400,205,921 |
| (3,216,363 | ) | 341,041,680 |
|
| | | | |
| | | |
(1) Retained Earnings (Accumulated Deficit) | | | | | |
(2) Members' Equity and Contributed Capital - Common Shareholders | | | | | |
(3) Accumulated Other Comprehensive Loss | | | | | |
The accompanying notes are an integral part of these consolidated financial statements.
MAMMOTH ENERGY SERVICES, INC.
CONSOLIDATED STATEMENTS OF CASH FLOWS
|
| | | | | | | | | | | |
| Years Ended December 31, |
| 2016 | | 2015 | | 2014 |
Cash flows from operating activities | | | | | |
Net loss | $ | (88,407,995 | ) | | $ | (27,231,414 | ) | | $ | (2,010,548 | ) |
Adjustments to reconcile net loss to cash provided by operating activities: | | | | | |
Equity based compensation | 501,147 |
| | — |
| | 3,838,842 |
|
Depreciation and amortization | 69,910,858 |
| | 72,393,882 |
| | 35,627,165 |
|
Amortization of coil tubing strings | 2,027,752 |
| | 2,075,787 |
| | 1,508,761 |
|
Amortization of debt origination costs | 398,806 |
| | 398,805 |
| | 1,094,367 |
|
Bad debt expense | 1,968,001 |
| | 3,682,218 |
| | 603,289 |
|
(Gain) loss on disposal of property and equipment | (747,896 | ) | | 1,429,087 |
| | (341,459 | ) |
Impairment of long-lived assets | 1,870,885 |
| | 12,124,353 |
| | — |
|
Deferred income taxes | 47,898,688 |
| | (5,717,451 | ) | | 5,814,982 |
|
Changes in assets and liabilities: | | | | | |
Accounts receivable, net | (4,636,428 | ) | | 27,522,839 |
| | (4,246,612 | ) |
Receivables from related parties | (2,415,741 | ) | | 9,499,181 |
| | (26,985,235 | ) |
Inventories | (1,627,179 | ) | | (2,611,047 | ) | | (1,055,660 | ) |
Prepaid expenses and other assets | (372,308 | ) | | 4,086,044 |
| | (2,233,175 | ) |
Accounts payable | 295,550 |
| | (27,633,817 | ) | | (417,121 | ) |
Payables to related parties | (4,578,623 | ) | | 2,420,581 |
| | (2,663,197 | ) |
Accrued expenses and other liabilities | 6,015,365 |
| | (4,054,709 | ) | | 1,834,108 |
|
Income taxes payable | 770 |
| | 8,277 |
| | (2,120,793 | ) |
Net cash provided by operating activities | 28,101,652 |
| | 68,392,616 |
| | 8,247,714 |
|
| | | | | |
Cash flows from investing activities: | | | | | |
Purchases of property and equipment | (11,317,909 | ) | | (26,251,675 | ) | | (111,592,602 | ) |
Purchases of property and equipment - related parties | — |
| | — |
| | (97,454 | ) |
Proceeds from disposal of property and equipment | 4,022,092 |
| | 1,416,766 |
| | 3,063,803 |
|
Other, net | — |
| | — |
| | 2,270 |
|
Business combination cash acquired (Note 12) | — |
| | — |
| | 7,059,068 |
|
Net cash used in investing activities | (7,295,817 | ) | | (24,834,909 | ) | | (101,564,915 | ) |
| | | | | |
Cash flows from financing activities: | | | | | |
Borrowings on long-term debt | 28,560,000 |
| | 14,500,000 |
| | 203,690,193 |
|
Repayments of long-term debt | (126,974,820 | ) | | (70,430,761 | ) | | (149,992,040 | ) |
Proceeds from initial public offering | 105,838,750 |
| | — |
| | — |
|
Initial public offering costs | (2,764,089 | ) | | — |
| | — |
|
Debt issuance costs | — |
| | — |
| | (2,328,603 | ) |
Capital (distributions) contributions | — |
| | (711 | ) | | 51,756,201 |
|
Net cash provided by (used in) financing activities | 4,659,841 |
| | (55,931,472 | ) | | 103,125,751 |
|
Effect of foreign exchange rate on cash | 154,237 |
| | (226,655 | ) | | (2,418,289 | ) |
Net increase (decrease) in cash and cash equivalents | 25,619,913 |
| | (12,600,420 | ) | | 7,390,261 |
|
Cash and cash equivalents at beginning of period | 3,074,072 |
| | 15,674,492 |
| | 8,284,231 |
|
Cash and cash equivalents at end of period | $ | 28,693,985 |
| | $ | 3,074,072 |
| | $ | 15,674,492 |
|
| | | | | |
Supplemental disclosure of cash flow information: | | | | | |
Cash paid for interest | $ | 3,518,623 |
| | $ | 5,120,482 |
| | $ | 3,492,763 |
|
Cash paid for income taxes | $ | 3,587,871 |
| | $ | 3,888,470 |
| | $ | 3,709,620 |
|
Supplemental disclosure of non-cash transactions: | | | | | |
Acquisition of Stingray Pressure Pumping and Stingray Logistics (Note 13) | $ | — |
| | $ | — |
| | $ | 176,570,932 |
|
Purchases of property and equipment included in trade accounts payable | $ | 2,788,602 |
| | $ | 740,555 |
| | $ | 7,047,706 |
|
The accompanying notes are an integral part of these consolidated financial statements.
MAMMOTH ENERGY SERVICES, INC.
NOTES TO CONSOLIDATED FINANCIAL STATEMENTS
| |
1. | Organization and Basis of Presentation |
The accompanying consolidated financial statements were prepared in accordance with the rules and regulations of the Securities and Exchange Commission, and reflect all adjustments, which in the opinion of management are necessary for the fair presentation of the results.
Mammoth Energy Services, Inc. ("Mammoth Inc." or the "Company"), together with its subsidiaries, is an integrated, growth-oriented oilfield services company serving companies engaged in the exploration and development of North American onshore unconventional oil and natural gas reserves. The Company was incorporated in Delaware in June 2016 as a wholly-owned subsidiary of Mammoth Energy Partners, LP, a Delaware limited liability company (the "Partnership" or the "Predecessor"). The Partnership was originally formed by Wexford Capital LP (“Wexford”) in February 2014 as a holding company under the name Redback Energy Services Inc. and was converted to a Delaware limited partnership in August 2014. On November 24, 2014, Mammoth Energy Holdings, LLC (“Mammoth Holdings,” an entity controlled by Wexford), Gulfport Energy Corporation (“Gulfport”) and Rhino Resource Partners LP (“Rhino”) (collectively known as “Predecessor Interest”) contributed their interest in certain of the entities presented below to the Partnership in exchange for 20 million limited partner units. Mammoth Energy Partners GP, LLC (the “General Partner”) held a non-economic general partner interest in the Partnership.
The following companies (“Operating Entities”) are included in these consolidated financial statements: Bison Drilling and Field Services, LLC (“Bison Drilling”), formed November 15, 2010; Bison Trucking LLC (“Bison Trucking”), formed August 9, 2013; White Wing Tubular Services LLC (“White Wing”), formed July 29, 2014; Barracuda Logistics LLC (“Barracuda”), formed October 24, 2014; Mr. Inspections LLC (“MRI”), formed January 25, 2015; Panther Drilling Systems LLC (“Panther”), formed December 11, 2012; Redback Energy Services, LLC (“Energy Services”), formed October 6, 2011; Redback Coil Tubing, LLC (“Coil Tubing”), formed May 15, 2012; Redback Pump Down Services LLC (“Pump Down”), formed January 16, 2015; Muskie Proppant LLC (“Muskie”), formed September 14, 2011; Stingray Pressure Pumping LLC (“Pressure Pumping”), formed March 20, 2012; Stingray Logistics LLC (“Logistics”), formed November 19, 2012; Great White Sand Tiger Lodging Ltd. (“Lodging”), formed October 1, 2007; Silverback Energy Services LLC ("Silverback"), formed June 8, 2016; and Mammoth Equipment Leasing LLC, formed on November 14, 2016. Prior to the contribution, the Partnership did not conduct any material business operations other than certain activities related to the preparation of the registration statement for a proposed initial public offering.
The contribution on November 24, 2014 of all Operating Entities, except Pressure Pumping, Logistics and entities created after contribution, was treated as a combination of entities under common control. On November 24, 2014, the Partnership also acquired Pressure Pumping and Logistics (collectively, the “Stingray Entities”) in exchange for 10 million limited partner units.
On October 12, 2016, the Partnership was converted into a Delaware limited liability company named Mammoth Energy Partners LLC (“Mammoth LLC”), and then Mammoth Holdings, Gulfport and Rhino, as all the members of Mammoth LLC, contributed their member interests in Mammoth LLC to Mammoth Inc. Prior to the conversion and the contribution, Mammoth Inc. was a wholly-owned subsidiary of the Partnership. Following the conversion and the contribution, Mammoth LLC (as the converted successor to the Partnership) was a wholly-owned subsidiary of Mammoth Inc. Mammoth Inc. did not conduct any material business operations until Mammoth LLC was contributed to it. On October 19, 2016, Mammoth Inc. closed its initial public offering of 7,750,000 shares of common stock (the "IPO"), which included an aggregate of 250,000 shares that were offered by Mammoth Holdings, Gulfport and Rhino, at a price to the public of $15.00 per share.
Net proceeds to Mammoth Inc. from its sale of 7,500,000 shares of common stock were approximately $103.1 million. On the closing date of the IPO, Mammoth Inc. repaid all outstanding borrowings under its revolving credit facility and intends to use the remaining net proceeds for general corporate purposes, which may include the acquisition of additional equipment and complementary businesses that enhance its existing service offerings, broaden its service offerings or expand its customer relationships.
At December 31, 2015, Mammoth Holdings, Gulfport and Rhino owned 68.7%, 30.5% and 0.8%, respectively, of the limited partner interest in the Predecessor. At December 31, 2016, Mammoth Holdings, Gulfport and Rhino owned the following share of outstanding common stock of Mammoth Inc:
MAMMOTH ENERGY SERVICES, INC.
NOTES TO CONSOLIDATED FINANCIAL STATEMENTS
|
| | | | | | |
| | At December 31, 2016 |
| | Share Count | | % Ownership |
Mammoth Holdings | | 20,443,903 |
| | 54.5 | % |
Gulfport | | 9,073,750 |
| | 24.2 | % |
Rhino | | 232,347 |
| | 0.6 | % |
Outstanding shares owned by related parties | | 29,750,000 |
| | 79.3 | % |
Total outstanding | | 37,500,000 |
| | 100.0 | % |
Operations
The Company's pressure pumping services include equipment and personnel used in connection with the completion and early production of oil and natural gas wells, well services include coil tubing units used to enhance the flow of oil or natural gas, natural sand proppant services include the distribution and production of natural sand proppant that is used primarily for hydraulic fracturing in the oil and gas industry. The Company's contract land and directional drilling services provides drilling rigs and directional tools for both vertical and horizontal drilling of oil and natural gas wells. The Company also provides other energy services, currently consisting of remote accommodations, for people working in the oil sands located in Northern Alberta, Canada.
The acquisition of the Stingray Entities added to the Company's completion and production portfolio. Specifically, by adding hydraulic fracturing and proppant hauling logistics services, the Company has developed a diverse offering of operations that can participate in nearly all phases of the oilfield services industry.
All of the Company’s operations are in North America. The Company operates in the Permian Basin, the Utica Shale, the Eagle Ford Shale, the Marcellus Shale, the Granite Wash, the Cana-Woodford Shale, the Cleveland Sand and the oil sands located in Northern Alberta, Canada. The Company's business depends in large part on the conditions in the oil and natural gas industry and, specifically, on the amount of capital spending by its customers. Any prolonged increase or decrease in oil and natural gas prices affects the levels of exploration, development and production activity, as well as the entire health of the oil and natural gas industry. Changes in the commodity prices for oil and natural gas could have a material effect on the Company’s results of operations and financial condition.
| |
2. | Summary of Significant Accounting Policies |
(a) Principles of Consolidation
The consolidated financial statements are prepared in accordance with Generally Accepted Accounting Principles ("GAAP"). All material intercompany accounts and transactions between the entities within the Company have been eliminated.
(b) Use of Estimates
The preparation of financial statements in conformity with GAAP requires management to make estimates and assumptions that affect the reported amounts of assets and liabilities, the disclosure of contingent assets and liabilities at the date of the financial statements, and the reported amounts of revenues and expenses during the reporting period. Actual results could differ from those estimates. Significant estimates include but are not limited to the allowance for doubtful accounts, reserves for self-insurance, depreciation and amortization of property and equipment, amortization of intangible assets, and future cash flows and fair values used to assess recoverability and impairment of long-lived assets, including goodwill.
(c) Cash and Cash Equivalents
All highly liquid investments with an original maturity of three months or less are considered cash equivalents. The Company maintains its cash accounts in financial institutions that are insured by the Federal Deposit Insurance Corporation, with the exception of cash held by Lodging in a Canadian financial institution. At December 31, 2016, we had $5.6 million, in Canadian dollars, of cash in Canadian accounts. Cash balances from time to time may exceed the insured amounts; however, the Company has not experienced any losses in such accounts and does not believe it is exposed to any significant credit risks on such accounts.
MAMMOTH ENERGY SERVICES, INC.
NOTES TO CONSOLIDATED FINANCIAL STATEMENTS
(d) Accounts Receivable
Accounts receivable include amounts due from customers for services performed and are recorded as the work progresses. The Company grants credit to customers in the ordinary course of business and generally does not require collateral. Most areas in which the Company operates provide for a mechanic’s lien against the property on which the service is performed if the lien is filed within the statutorily specified time frame. Customer balances are generally considered delinquent if unpaid by the 30th day following the invoice date and credit privileges may be revoked if balances remain unpaid.
The Company regularly reviews receivables and provides for estimated losses through an allowance for doubtful accounts. In evaluating the level of established reserves, the Company makes judgments regarding its customers’ ability to make required payments, economic events, and other factors. As the financial conditions of customers change, circumstances develop, or additional information becomes available, adjustments to the allowance for doubtful accounts may be required. In the event the Company was to determine that a customer may not be able to make required payments, the Company would increase the allowance through a charge to income in the period in which that determination is made. Uncollectible accounts receivable are periodically charged against the allowance for doubtful accounts once final determination is made of their uncollectability.
Following is a roll forward of the allowance for doubtful accounts for the years ended December 31, 2016, 2015 and 2014:
|
| | | | |
Balance, January 1, 2014 | | $ | 1,621,147 |
|
Additions charged to expense | | 603,289 |
|
Deductions for uncollectible receivables written off | | (1,634,934 | ) |
Balance, December 31, 2014 | | 589,502 |
|
Additions charged to expense | | 3,682,218 |
|
Deductions for uncollectible receivables written off | | (324,288 | ) |
Balance, December 31, 2015 | | 3,947,432 |
|
Additions charged to expense | | 1,968,001 |
|
Deductions for uncollectible receivables written off | | (602,967 | ) |
Balance, December 31, 2016 | | $ | 5,312,466 |
|
As discussed in Note 1, prolonged declines in pricing can impact the overall health of the oil and natural gas industry. The year ended December 31, 2016 contained such pricing conditions which may lead to enhanced risk of uncollectiblity on certain receivables. As such, the Company has made specific reserves consistent with Company policy which resulted in additions to allowance for doubtful accounts. The Company will continue to pursue collection until such time as final determination is made consistent with Company policy.
(e) Inventory
Inventory consists of raw sand and processed sand available for sale, chemicals and other products sold as a bi-product of completion and production operations, and supplies used in performing services. Inventory is stated at the lower of cost or market (net realizable value) on a average cost basis. The Company assesses the valuation of its inventories based upon specific usage and future utility.
Inventory also consists of coil tubing strings of various widths, diameters and lengths that are used in providing specialized services to customers who are primarily operators of oil or gas wells. The strings are used at various rates based on factors such as well conditions (i.e. pressure and friction), vertical and horizontal length of the well, running speed of the string in the well, and total running feet accumulated to the string. The Company obtains usage information from data acquisition software and other established assessment methods and attempts to amortize the strings over their estimated useful life. In no event will a string be amortized over a period longer than 12 months. Amortization of coil strings is included in services cost of revenue in the Consolidated Statements of Comprehensive Loss and totaled $2,027,752, $2,075,787 and $1,508,761 for the years ended December 31, 2016, 2015, and 2014, respectively.
(f) Prepaid Expenses
Prepaid expenses primarily consist of insurance costs. Insurance costs are expensed over the periods that these costs benefit.
MAMMOTH ENERGY SERVICES, INC.
NOTES TO CONSOLIDATED FINANCIAL STATEMENTS
(g) Property and Equipment
Property and equipment, including renewals and betterments, are capitalized and stated at cost, while maintenance and repairs that do not increase the capacity, improve the efficiency or safety, or improve or extend the useful life are charged to operations as incurred. Disposals are removed at cost, less accumulated depreciation, and any resulting gain or loss is recorded in operations. Depreciation is calculated using the straight-line method over the shorter of the estimated useful life, or the remaining lease term, as applicable. Depreciation does not begin until property and equipment is placed in service. Once placed in service, depreciation on property and equipment continues while being repaired, refurbished, or between periods of deployment.
(h) Long-Lived Assets
The Company reviews long-lived assets for recoverability in accordance with the provisions of Financial Accounting Standards Board ("FASB") Accounting Standard Codification (“ASC”) Topic 360, Impairment or Disposal of Long-Lived Assets, which requires that long-lived assets be reviewed for impairment whenever events or changes in circumstances indicate that the carrying amount of the assets may not be recoverable. Recoverability of assets is measured by comparing the carrying amount of an asset to future undiscounted net cash flows expected to be generated by the asset. These evaluations for impairment are significantly impacted by estimates of revenues, costs and expenses, and other factors. If long-lived assets are considered to be impaired, the impairment to be recognized is measured by the amount in which the carrying amount of the assets exceeds the fair value of the assets. For the years ended December 31, 2016, and 2015, the Company recognized an impairment loss of $1,870,885 and $9,874,458, respectively, on various fixed assets included in property, plant and equipment, net in the Consolidated Balance Sheets. Additionally, during the year ended December 31, 2015, the Company recognized an impairment loss of $1,904,982 on a terminated long term contractual agreement. No impairments occurred during the year ended December 31, 2014.
(i) Goodwill
Goodwill is tested for impairment annually, or more frequently if events or changes in circumstances indicate that goodwill might be impaired. The impairment test is a two-step process. First, the fair value of each reporting unit is compared to its carrying value to determine whether an indication of impairment exists. If impairment is indicated, then the implied value of the reporting unit’s goodwill is determined by allocating the unit’s fair value to its assets and liabilities as if the reporting unit had been acquired in a business combination. The fair value of the reporting unit is determined using the discounted cash flow approach, excluding interest. The impairment for goodwill is measured as the excess of its carrying value over its implied value. Goodwill was tested for impairment as of December 31, 2016. For the years ended December 31, 2016 and 2014, no impairment losses were recognized. During year ended December 31, 2015, the Company recognized impairments of $88,247.
(j) Other Non-Current Assets
Other non-current assets primarily consist of deferred financing costs on the credit facility (See Note 8) and sales tax receivables.
(k) Amortizable Intangible Assets
Intangible assets subject to amortization include customer relationships and trade names. Customer relationships are amortized based on an estimated attrition factor and trade names are amortized over their estimated useful lives. During the year ended December 31, 2015, the Company terminated one customer relationship and impaired the remaining unamortized value of the intangible and recognized an impairment loss of $256,666. There were no impairment losses recognized for amortizable assets for either the years ended December 31, 2016 or 2014.
(l) Fair Value of Financial Instruments
The Company's financial instruments consist of cash and cash equivalents, trade receivables, trade payables, amounts receivable or payable to related parties, and long-term debt. The carrying amount of cash and cash equivalents, trade receivables, receivables from related parties and trade payables approximates fair value because of the short-term nature of the instruments. The fair value of long-term debt approximates its carrying value because the cost of borrowing fluctuates based upon market conditions.
(m) Revenue Recognition
The Company generates revenue from multiple sources within its operating segments. In all cases, revenue is recognized when services are performed, collection of the receivable is probable, persuasive evidence of an arrangement exists, and the price is fixed and determinable. Services are sold without warranty or right of return. Taxes assessed on revenue transactions are presented on a net basis and are not included in revenue.
MAMMOTH ENERGY SERVICES, INC.
NOTES TO CONSOLIDATED FINANCIAL STATEMENTS
Pressure pumping services are typically provided based upon a purchase order, contract, or on a spot market basis. Services are provided on a day rate, contracted, or hourly basis, and revenue is recognized as the work progresses. Jobs for these services are typically short-term in nature and range from a few hours to multiple days. Revenue is recognized upon the completion of each day’s work based upon a completed field ticket, which includes the charges for the services performed, mobilization of the equipment to the location, and personnel. Additional revenue is generated through labor charges and the sale of consumable supplies that are incidental to the service being performed. The labor charges and the use of consumable supplies are reflected on the completed field tickets.
Natural sand proppant revenues are recognized when legal title passes to the customer, which may occur at the production facility, rail origin or at the destination terminal. At that point, delivery has occurred, evidence of a contractual arrangement exists, the price is fixed and determinable, and collectability is reasonably assured. Amounts received from customers in advance of sand deliveries are recorded as deferred revenue. Customers have the ability to make up contractual short falls by achieving higher-than-contracted volumes over the shortfall window. Contractual shortfall revenue is deemed not probable until the end of the measurement period.
Well services are typically provided based upon a purchase order, contract, or on a spot market basis. Services are provided on a day rate, contracted, or hourly basis, and revenue is recognized as the work progresses. Jobs for these services are typically short-term in nature and range from a few hours to multiple days. Our equipment rental services are recognized upon completion of each day's work based on a completed field ticket.
Contract drilling services are provided under daywork or footage contracts, and revenue is recognized as the work progresses based on the days completed or the feet drilled, as applicable. Mobilization revenue and costs for daywork and footage contracts are recognized over the days of actual drilling.
Directional drilling services are provided on a day rate or hourly basis, and revenue is recognized as work progresses. Proceeds from customers for the cost of equipment that is damaged or lost down-hole are reflected as service revenues as this is deemed to be perfunctory or inconsequential to the underlying service being performed.
Revenue from remote accommodation services is recognized when rooms are occupied and services have been rendered. Advance deposits on rooms and special events are deferred until services are provided to the customer. During the year ended December 31, 2016, the Company recognized and collected $524,997 in business interruption insurance proceeds which is included in Service revenue in the accompanying Consolidated Statements of Comprehensive Loss. The proceeds resulted from loss of revenue relating to wildfires that forced evacuation of personnel.
The timing of revenue recognition may differ from contract billing or payment schedules, resulting in revenues that have been earned but not billed (“unbilled revenue”). The Company had $2,732,993 and $3,414,853 of unbilled revenue included in accounts receivable, net in the Consolidated Balance Sheets at December 31, 2016 and 2015, respectively. The Company had $10,506,958 and $7,459,988 of unbilled revenue included in receivables from related parties in the Condensed Consolidated Balance Sheets at December 31, 2016 and 2015, respectively.
(n) Unaudited Pro Forma Earnings (loss) per Share
The Company’s pro forma basic earnings (loss) per share amounts have been computed based on the weighted-average number of shares of common stock outstanding for the period, as if the common shares issued at the IPO were outstanding for the full year of 2016 and 2015. Diluted earnings per share reflects the potential dilution, using the treasury stock method. During periods in which the Company realizes a net loss, restricted stock awards would be anti-dilutive to net loss per share and conversion into common stock is assumed not to occur.
(o) Equity-based Compensation
The Company records equity-based payments at fair value on the date of grant, and expenses the value of these equity-based payments in compensation expense over the applicable vesting periods. See Note 11.
(p) Stock-based Compensation
The Company's stock-based compensation program consists of restricted stock units granted to employees and restricted stock units granted to non-employee directors under the Mammoth Energy Services, Inc. 2016 Incentive Plan (the "2016 Plan"). The Company recognizes in its financial statements the cost of employee services received in exchange for restricted stock based on the fair value of the equity instruments as of the grant date. In general, this value is amortized over the vesting period; for grants with a non-substantive service condition, this value is recognized immediately.
MAMMOTH ENERGY SERVICES, INC.
NOTES TO CONSOLIDATED FINANCIAL STATEMENTS
Amounts are recognized in selling, general, and administrative expenses. See Note 12.
In March 2016, the FASB issued ASU No. 2016-09, “Compensation - Stock Compensation,” which modifies several aspects of the accounting for share-based payment transactions, including the income tax consequences, classification of awards as either equity or liabilities, and classification on the statement of cash flows. ASU 2016-09 is effective for annual reporting periods beginning after December 15, 2016 with early adoption permitted. With the early adoption of this standard, we are accounting for forfeitures in the period in which they occur. The adoption has no impact on prior period as the year ended December 31, 2016 is the first year under which the Company is treated as as a taxable entity for federal income tax purposes and there have been no historical vestings of either equity or share-based compensation.
(q) Income Taxes
On October 12, 2016, immediately prior to the IPO of Mammoth Inc., the Partnership converted into a limited liability company named Mammoth Energy Partners LLC (“Mammoth LLC”). All equity interests in Mammoth LLC were contributed to Mammoth Inc. and Mammoth LLC became a wholly owned subsidiary of Mammoth Inc. Mammoth Inc. is a C corporation under the Internal Revenue Code and is subject to income tax. Historically, Mammoth LLC and each of the Operating Entities other than Lodging was treated as a partnership for federal income tax purposes. As a result, essentially all taxable earnings and losses were passed through to its members, and Mammoth LLC did not pay any federal income taxes at the entity level. Mammoth Inc. owns the member interests in several single member limited liability companies. These LLCs are subject to taxation in Texas where the Company does business; therefore, the Company may provide for income taxes attributable to that state on a current basis. The income tax provision for the period before the IPO has been prepared on a separate return basis for Mammoth LLC and all of its subsidiaries that were treated as a partnership for federal income tax purposes.
Subsequent to the IPO, the Company's operations are included in a consolidated federal income tax return and other state returns. Accordingly, the Company has recognized deferred tax assets and liabilities for the future tax consequences attributable to differences between the financial statement carrying amounts of existing assets and liabilities and their respective tax bases for all our subsidiaries as if each entity were a corporation, regardless of its actual characterization for U.S. federal income tax purposes. The Company's effective tax rate was 34.6%, excluding the conversion to a C Corporation (See Note 1), for the year ended December 31, 2016. The Company's effective tax rate can fluctuate as a result of the impact of state income taxes, permanent differences and changes in pre-tax income.
Under FASB ASC 740, deferred tax assets and liabilities are recognized for the future tax consequences attributable to differences between the financial statement carrying amounts of existing assets and liabilities and their respective tax bases. Deferred tax assets and liabilities are measured using statutory tax rates expected to apply to taxable income in the years in which those temporary differences are expected to be recovered or settled. The effect of deferred tax assets and liabilities as a result of a change in tax rate is recognized in the period that includes the statutory enactment date. A valuation allowance for deferred tax assets is recognized when it is more likely than not that the benefit of deferred tax assets will not be realized.
The Company has included a pro forma provision for income taxes assuming it had been taxed as a C corporation in all periods prior to the conversion and contribution as part of its earnings per share calculation in Note 10. The unaudited pro forma data are presented for informational purposes only, and do not purport to project our results of operations for any future period or its financial position as of any future date.
Lodging is subject to foreign income taxes, and such taxes are provided in the financial statements pursuant to FASB ASC 740, Income Taxes.
The Company evaluates tax positions taken or expected to be taken in preparation of its tax returns and disallows the recognition of tax positions that do not meet a “more likely than not” threshold of being sustained upon examination by the taxing authorities. During the years ended December 31, 2016 and 2015, no material uncertain tax positions existed. Penalties and interest, if any, are recognized in general and administrative expense. The Company's 2016, 2015, 2014 and 2013 income tax returns remain open to examination by the applicable taxing authorities.
In November 2015, the FASB issued Accounting Standards Update ("ASU") No. 2015-17, "Income Taxes," which simplifies the presentation of deferred income taxes by requiring deferred tax liabilities and assets be classified as noncurrent in the balance sheet. ASU 2015-17 is effective for fiscal years, and interim periods within those years, beginning after December 15, 2016, with early adoption permitted. Early adoption was elected for the year ended December 31, 2016 with a retrospective change to the December 31, 2015 consolidated balance sheet as previously
MAMMOTH ENERGY SERVICES, INC.
NOTES TO CONSOLIDATED FINANCIAL STATEMENTS
presented is required pursuant to ASU 2015-17. There was no impact on the December 31, 2015 consolidated balance sheet.
(r) Foreign Currency Translation
For foreign operations, assets and liabilities are translated at the period-end exchange rate, and income statement items are translated at the average exchange rate for the period. Resulting translation adjustments are recorded within accumulated other comprehensive loss. Assets and liabilities denominated in foreign currencies, if any, are re-measured at the balance sheet date. Transaction gains or losses are included as a component of current period earnings.
(s) Other Comprehensive (Loss) Income
Comprehensive loss consists of net loss and other comprehensive loss. Other comprehensive loss included certain changes in equity that are excluded from net loss. Specifically, cumulative foreign currency translation adjustments are included in accumulated other comprehensive loss.
(t) Concentrations of Credit Risk and Significant Customers
Financial instruments that potentially subject the Company to concentrations of credit risk consist of cash and cash equivalents in excess of federally insured limits and trade receivables. The Company's accounts receivable have a concentration in the oil and gas industry and the customer base consists primarily of independent oil and natural gas producers. At December 31, 2016 and 2015, no third-party customer accounted for more than 10% of the Company's trade accounts receivable and receivables from related parties balance combined. At December 31, 2016 and 2015, related party customers accounted for 58% and 59%, respectively, of the Company's trade accounts receivable and receivables from related parties balance combined. At December 31, 2016 and 2015, one related party customer from the pressure pumping segment accounted for 39% and 37%, respectively, of the Company's trade accounts receivable and receivables from related parties balance combined. At December 31, 2016 and 2015, one related party customer from the natural sand proppant segment accounted for 11% and 16%, respectively, of the Company's trade accounts receivable and receivables from related parties balance combined. At December 31, 2016 and 2015, one related party customer accounted for 53% and 56%, respectively, of the Company's trade accounts receivable and receivables from related parties balance combined. During the years ended December 31, 2016, and 2015, one related party customer accounted for 57% and 47%, respectively, of the Company's total revenue. During the years ended December 31, 2016, and 2015 one related party customer from the pressure pumping segment accounted for 44% and 35%, respectively, of the Company's total revenue. During the years ended December 31, 2016, and 2015 one related party customer from the natural sand proppant segment accounted for 11% and 11%, respectively, of the Company's total revenue. One third-party customer accounted for greater than 10% of the Company's total revenue for years ended December 31, 2016, and 2015, at 11% and 11%, respectively. No customers accounted for greater than 10% of the Company's total revenue for the year ended December 31, 2014.
(u) New Accounting Pronouncements
In July 2015, the FASB issued ASU No. 2015-11, “Inventory (Topic 330): Simplifying the Measurement of Inventory,” which changes inventory measured using any method other than last-in, first-out (LIFO) or the retail inventory method (for example, inventory measured using first-in, first-out (FIFO) or average cost) at the lower of cost and net realizable value. ASU 2015-11 is effective for annual and interim reporting periods beginning after December 15, 2016, with early adoption permitted. We do not expect the adoption of this guidance to have a material effect on the Company's consolidated financial statements.
In May 2014, the FASB issued ASU 2014-09, “Revenue from Contracts with Customers.” ASU 2014-09 supersedes existing revenue recognition requirements in GAAP and requires an entity to recognize revenue when it transfers promised goods or services to customers in an amount that reflects the consideration to which the entity expects to be entitled to in exchange for those goods or services. Additionally, it requires expanded disclosures regarding the nature, amount, timing and certainty of revenue and cash flows from contracts with customers. The ASU was effective for annual and interim reporting periods beginning after December 15, 2016, using either a full or a modified retrospective application approach; however, in July 2015 the FASB decided to defer the effective date by one year (until 2018) by issuing ASU No. 2015-14, "Revenue From Contracts with Customers: Deferral of the Effective Date." The Company expects to adopt this new revenue guidance utilizing the retrospective method of adoption in the first quarter of 2018, and because the Company is still evaluating the portion of its revenues that may be subject to the new leasing guidance discussed below, it is unable to quantify the impact that the new revenue standard will have on the Company’s consolidated financial statements upon adoption.
In February 2016, the FASB issued ASU No, 2016-2 “Leases” amending the current accounting for leases. Under the new provisions, all lessees will report a right-of-use asset and a liability for the obligation to make payments for all leases with
MAMMOTH ENERGY SERVICES, INC.
NOTES TO CONSOLIDATED FINANCIAL STATEMENTS
the exception of those leases with a term of 12 months or less. All other leases will fall into one of two categories: (i) a financing lease or (ii) an operating lease. Lessor accounting remains substantially unchanged with the exception that no leases entered into after the effective date will be classified as leveraged leases. For sale leaseback transactions, a sale will only be recognized if the criteria in the new revenue recognition standard are met. ASU 2016-2 is effective for fiscal years beginning after December 15, 2018, and interim periods within that fiscal year. Early adoption is permitted. Since a portion of the Company’s revenue may be subject to this new leasing guidance, it expects to adopt this updated leasing guidance at the same time its adopts the new revenue standard discussed above, utilizing the retrospective method of adoption. This new leasing guidance will also impact the Company in situations where it is the lessee, and in certain circumstances it will have a right-of-use asset and lease liability on its consolidated financial statements. The Company is currently evaluating the effect the new guidance will have on our consolidated financial statements and results of operations.
A summary of the Company's inventory is shown below:
|
| | | | | | | | |
| | December 31, |
| | 2016 | | 2015 |
Supplies | | $ | 4,020,670 |
| | $ | 4,421,244 |
|
Raw materials | | 75,971 |
| | 47,701 |
|
Work in process | | 205,450 |
| | 233,719 |
|
Finished goods | | 52,997 |
| | 52,997 |
|
Total inventory | | $ | 4,355,088 |
| | $ | 4,755,661 |
|
| |
4. | Property, Plant and Equipment |
Property, plant and equipment include the following:
|
| | | | | | | | | |
| | | December 31, |
| Useful Life | | 2016 | | 2015 |
Land | | | $ | 2,010,555 |
| | $ | 2,010,555 |
|
Land improvements | 15 years or life of lease | | 3,640,976 |
| | 3,734,178 |
|
Buildings | 15-20 years | | 42,191,745 |
| | 41,218,431 |
|
Drilling rigs and related equipment | 3-15 years | | 138,526,519 |
| | 139,619,078 |
|
Pressure pumping equipment | 3-5 years | | 96,500,592 |
| | 93,956,896 |
|
Coil tubing equipment | 4-10 years | | 28,019,217 |
| | 30,190,216 |
|
Other machinery and equipment | 7-20 years | | 35,548,357 |
| | 37,829,135 |
|
Vehicles, trucks and trailers | 5-10 years | | 29,964,148 |
| | 29,542,164 |
|
Other property and equipment | 3-12 years | | 11,416,334 |
| | 11,169,306 |
|
| | | 387,818,443 |
| | 389,269,959 |
|
Deposits on equipment and equipment in process of assembly | | | 8,701,725 |
| | 2,072,278 |
|
| | | 396,520,168 |
| | 391,342,237 |
|
Less: accumulated depreciation | | | 175,272,940 |
| | 118,315,572 |
|
Property, plant and equipment, net | | | $ | 221,247,228 |
| | $ | 273,026,665 |
|
Depreciation expense was $60,839,858, $63,292,507 and $34,668,765, respectively, for the years ended December 31, 2016, 2015 and 2014.
Proceeds from customers for horizontal and directional drilling services equipment, damaged or lost down-hole are reflected in revenue with the carrying value of the related equipment charged to cost of service revenues and are reported as cash inflows from investing activities in the statement of cash flows. For the years ended December 31, 2016, 2015 and
MAMMOTH ENERGY SERVICES, INC.
NOTES TO CONSOLIDATED FINANCIAL STATEMENTS
2014, proceeds from the sale of equipment damaged or lost down-hole were $699,528, $404,383 and $698,860, respectively, and gain on sales of equipment damaged or lost down-hole were $447,477, $76,319 and $47,803, respectively.
Deposits on equipment and equipment in process of assembly represents deposits placed with vendors for equipment that is in the process of assembly and purchased equipment that is being outfitted for its intended use. The equipment is not yet placed in service.
A summary of our impairments is as follows:
|
| | | | | | | | |
| | December 31, |
| | 2016 | | 2015 |
Flowback equipment (a) | | $ | 1,384,751 |
| | $ | — |
|
Drilling rigs (a) | | 347,547 |
| | 8,917,240 |
|
Fluid storage equipment (a) | | — |
| | 957,218 |
|
Other property, plant and equipment (a) | | 138,587 |
| | — |
|
Impairment of long term contractual agreement (b) | | — |
| | 1,904,982 |
|
Impairment of goodwill (c) | | — |
| | 88,247 |
|
Impairment of intangible (d) | | — |
| | 256,666 |
|
| | $ | 1,870,885 |
| | $ | 12,124,353 |
|
| |
a. | For the years ended December 31, 2016 and 2015, the Company recognized impairments of $1,870,885 and $9,874,458, respectively, to reduce the carrying value of certain assets which were classified as held for use, to their estimated fair values, based on expected sales prices. No impairments occurred during the year ended December 31, 2014. The Company impaired based on future expected cash flows using significant unobservable inputs (Level 3) based on an income approach. |
| |
b. | The Company impaired $1,904,982 of assets in 2015 related to prepaid assets pursuant to a purchase contract from a vendor. The impairment impacted the prepaid expenses and other non-current assets lines of the Consolidated Balance Sheet for $1,080,000 and $824,982, respectively. |
| |
c. | The Company determined that there was an indication of impairment present based on the results of the first step of the goodwill impairment test for the goodwill held at Energy Services and fully impaired the $88,247 balance. |
| |
d. | The Company terminated one customer relationship related to its amortizable intangible assets and impaired the remaining unamortized value of the intangible of that relationship. |
The assumptions used in the impairment evaluation for long-lived assets are inherently uncertain and require management’s judgment. A continued period of low oil and natural gas prices or continued reductions in capital expenditures by our customers would likely have an adverse impact on our utilization and the prices that we receive for our services. This could result in the recognition of future material impairment charges on the same, or additional, property and equipment if future cash flow estimates, based upon information then available to management, indicate that their carrying values are not recoverable.
| |
6. | Goodwill and Intangible Assets |
The Company had the following definite lived intangible assets recorded as of the dates presented below:
|
| | | | | | | | |
| | December 31, |
| | 2016 | | 2015 |
Customer relationships | | $ | 33,605,000 |
| | $ | 33,605,000 |
|
Trade names | | 7,110,000 |
| | 7,110,000 |
|
Less: accumulated amortization - customer relationships | | 17,655,228 |
| | 9,295,228 |
|
Less: accumulated amortization - trade names | | 1,492,943 |
| | 781,943 |
|
Intangible assets, net | | $ | 21,566,829 |
| | $ | 30,637,829 |
|
Amortization expense for intangible assets was $9,071,000, $9,101,375 and $938,400 for the years ended December 31, 2016, 2015, and 2014, respectively. The original life of customer relationships range from 4 to 10 years with a remaining
MAMMOTH ENERGY SERVICES, INC.
NOTES TO CONSOLIDATED FINANCIAL STATEMENTS
average useful life of 3.35 years. Trade names are amortized over a 10 year useful life and as of December 31, 2016 the remaining useful life was 7.90 years.
Aggregated expected amortization expense for the future periods is expected to be as follows:
|
| | | | |
Year ended December 31: | | Amount |
2017 | | $ | 9,071,004 |
|
2018 | | 8,224,005 |
|
2019 | | 738,504 |
|
2020 | | 738,504 |
|
2021 | | 732,752 |
|
Thereafter | | 2,062,060 |
|
| | $ | 21,566,829 |
|
Goodwill was $86,043,148 at December 31, 2016 and 2015.
| |
7. | Accrued Expenses and Other Current Liabilities |
Accrued expense and other current liabilities included the following:
|
| | | | | | | | |
| | December 31, |
| | 2016 | | 2015 |
Accrued compensation, benefits and related taxes | | $ | 2,368,143 |
| | $ | 1,349,493 |
|
Financed insurance premiums | | 3,293,859 |
| | 3,194,564 |
|
State and local taxes payable | | 319,597 |
| | 504,658 |
|
Insurance reserves | | 971,351 |
| | 739,775 |
|
Other | | 1,444,018 |
| | 1,930,466 |
|
Total | | $ | 8,396,968 |
| | $ | 7,718,956 |
|
Financed insurance premiums are due in monthly installments, bear interest at rates ranging from 1.79% to 5.00%, are unsecured, and mature within the twelve month period following the close of the year.
Mammoth Credit Facility
On November 25, 2014, the Partnership entered into a revolving credit and security agreement with a bank that provides for maximum borrowings of $170.0 million. The facility, as amended in connection with the IPO, matures on November 25, 2019. Borrowings under this facility are secured by the assets of Mammoth Inc., inclusive of the subsidiary companies. The maximum availability of the facility is subject to a borrowing base calculation prepared monthly. Concurrent with the execution of the facility, the initial advance was used to repay all the debt of the operating subsidiaries then outstanding. Interest is payable monthly at a base rate set by the institution’s commercial lending group plus an applicable margin. Additionally, at the Company's request, outstanding balances are permitted to be converted to LIBOR rate plus applicable margin tranches at set increments of $500,000. The LIBOR rate option allows the Company to select interest periods from one, two, three or six months. The applicable margin for either the base rate or the LIBOR rate option can vary from 1.5% to 3.0%, based upon a calculation of the excess availability of the line as a percentage of the maximum credit limit. The deferred loan costs associated with this facility are classified in other non-current assets.
At December 31, 2016, the facility was undrawn and had availability of $146,181,002.
At December 31, 2015, $95.0 million of the outstanding balance of the facility was in a one month LIBOR rate option tranche with an interest rate of 3.04%, and there was availability of $44,619,551 under the facility.
MAMMOTH ENERGY SERVICES, INC.
NOTES TO CONSOLIDATED FINANCIAL STATEMENTS
The facility contains various customary affirmative and restrictive covenants. Among the various covenants are specifically identified financial covenants placing requirements of a minimum interest coverage ratio (3.0 to 1.0), maximum leverage ratio (4.0 to 1.0), and minimum availability ($10.0 million). As of December 31, 2016 and 2015, the Company was in compliance with its covenants under the facility.
As discussed in Note 1, the Partnership was converted into a limited liability company on October 12, 2016 and the membership interests in the limited liability company were contributed to the Company. As a result, the Company will file a consolidated return for the period October 12, 2016 through December 31, 2016. Prior to the conversion, the Partnership, other than Lodging, was not subject to corporate income taxes.
The components of income tax expense (benefit) attributable to the Company for the year ended December 31, 2016, 2015 and 2014, respectively, are as follows:
|
| | | | | | | | | | | | |
| | Year Ended December 31, |
| | 2016 | | 2015 | | 2014 |
U.S. current income tax benefit | | $ | 2,306,512 |
| | $ | 12,861 |
| | $ | 24,805 |
|
U.S. deferred income tax expense | | 47,957,169 |
| | (5,625,436 | ) | | 5,549,517 |
|
Foreign current income tax expense | | 3,594,014 |
| | 3,878,855 |
| | 1,674,407 |
|
Foreign deferred income tax expense | | 27,176 |
| | 144,634 |
| | 265,465 |
|
Total | | $ | 53,884,871 |
| | $ | (1,589,086 | ) | | $ | 7,514,194 |
|
Foreign tax credits may be applied for up to five years. Tax credits must be utilized five years subsequent to the distribution of the underlying earnings. As of December 31, 2016, the distributions have not yet occurred.
A reconciliation of the statutory federal income tax amount to the recorded expense is as follows: |
| | | | | | | | | | | | |
| | Year Ended December 31, |
| | 2016 | | 2015 | | 2014 |
Loss before income taxes | | $ | (34,523,124 | ) | | $ | (28,820,500 | ) | | $ | 5,503,646 |
|
Statutory income tax rate | | 35 | % | | 35 | % | | 35 | % |
Expected income tax expense | | (12,083,093 | ) | | (10,087,175 | ) | | 1,926,276 |
|
Income earned as non-taxable entity (See Note 2) | | 13,750,827 |
| | — |
| | — |
|
Effect due to change to C corporation (See Note 2) | | 53,088,861 |
| | — |
| | — |
|
Change in entity status | | — |
| | (4,792,243 | ) | | 6,379,117 |
|
Non taxable entity | | — |
| | 15,455,772 |
| | 713,106 |
|
Other permanent differences | | 209,546 |
| | — |
| | — |
|
State tax expenses | | 21,181 |
| | — |
| | — |
|
Change in tax rate | | (24,803 | ) | | — |
| | — |
|
Foreign income tax rate differential | | (1,077,648 | ) | | (1,369,575 | ) | | (2,355,816 | ) |
Other | | — |
| | (795,865 | ) | | 851,511 |
|
Total | | $ | 53,884,871 |
| | $ | (1,589,086 | ) | | $ | 7,514,194 |
|
MAMMOTH ENERGY SERVICES, INC.
NOTES TO CONSOLIDATED FINANCIAL STATEMENTS
Deferred tax liabilities attributable to the Company consisted of the following:
|
| | | | | | | | |
| | Year Ended December 31, |
| | 2016 | | 2015 |
Deferred tax assets: | | | | |
Allowance for doubtful accounts | | $ | 1,892,761 |
| | $ | — |
|
Deferred stock compensation | | 1,686,671 |
| | — |
|
Accrued liabilities | | 746,132 |
| | — |
|
Other | | 1,785,999 |
| | 86,580 |
|
Deferred tax assets | | 6,111,563 |
| | 86,580 |
|
| | | | |
Deferred tax liabilities: | | | | |
Property and equipment | | $ | (42,525,793 | ) | | $ | (1,484,350 | ) |
Intangible assets | | (7,662,590 | ) | | — |
|
Unrepatriated foreign earnings | | (3,451,110 | ) | | — |
|
Other | | (142,859 | ) | | (63,189 | ) |
Deferred tax liabilities | | (53,782,352 | ) | | (1,547,539 | ) |
Net deferred tax liability | | $ | (47,670,789 | ) | | $ | (1,460,959 | ) |
| | | | |
Reflected in accompanying balance sheet as: | | | | |
Deferred income taxes | | $ | (47,670,789 | ) | | $ | (1,460,959 | ) |
| |
10. | Stockholders' Equity and Pro Forma Earnings Per Share |
Earnings Per Unit
The Partnership's limited partner units were issued November 24, 2014. However, the net income per common unit on the Consolidated Statements of Comprehensive Loss is based on the net income of the Partnership for the full years presented, since the entities were under common control as described in Note 1.
The Partnership's net loss was allocated wholly to the limited partner units as the General Partner did not have an economic interest.
Basic net loss per common unit is calculated by dividing net loss by the weighted-average number of common units outstanding during the period. Although the units were not issued until November 24, 2014, units issued for common control entities have been calculated based on the weighted average units outstanding as if they were outstanding from the beginning of the periods presented, in conjunction with the treatment of common control entities.
|
| | | | | | | | |
| | Year Ended December 31, |
| | 2015 | | 2014 |
Net loss | | $ | (27,231,414 | ) | | $ | (2,010,548 | ) |
Net loss per limited partner unit | | (0.91 | ) | | (0.10 | ) |
Weighted-average common units outstanding | | 30,000,000 |
| | 21,056,073 |
|
Common Stock Offering
On October 14, 2016, Mammoth Inc.’s common stock began trading on The Nasdaq Global Select Market under the symbol “TUSK.” On October 19, 2016, the Company closed the IPO of 7,750,000 shares of common stock at $15.00 per share. Net proceeds to Mammoth Inc. from its sale of 7,500,000 shares of common stock were approximately $103.1 million.
MAMMOTH ENERGY SERVICES, INC.
NOTES TO CONSOLIDATED FINANCIAL STATEMENTS
The authorized capital stock of the Company consists of 200 million shares of common stock, par value $0.01 per share.
Earnings Per Share
The number of common shares outstanding on a fully-converted basis was the same before and after any conversion of our owner units. Each time one common share was issued upon conversion of investor units, the number of common shares went up by one, and the number of common units outstanding that were convertible went down by one. Accordingly, for the year ended December 31, 2015 and 2014, there was no difference between common stock basic and diluted earnings per share because the conversion of common units into common shares did not impact the number of common shares on a fully-converted basis.
|
| | | | | | | | | | | | |
Year Ended December 31, | | Weighted Average Shares Outstanding | | Share Issuance at IPO (a) | | Conversion | | Weighted Average Units Outstanding |
2016 | | 31,500,000 |
| | 1,500,000 |
| | (30,000,000 | ) | | 30,000,000 |
|
2015 | | 30,000,000 |
| | — |
| | (30,000,000 | ) | | 30,000,000 |
|
2014 | | 21,056,073 |
| | — |
| | (21,056,073 | ) | | 21,056,073 |
|
| |
(a) | Weighted average of 7,500,000 shares issued from the closing date of the IPO on October 19, 2016 to December 31, 2016. |
|
| | | | | | | | | | | | |
| | Year Ended December 31, |
| | 2016 | | 2015 | | 2014 |
Basic loss per share: | | | | | | |
Allocation of earnings: | | | | | | |
Net loss | | $ | (88,407,995 | ) | | $ | (27,231,414 | ) | | $ | (2,010,548 | ) |
Weighted average common shares outstanding | | 31,500,000 |
| | 30,000,000 |
| | 21,056,073 |
|
Basic loss per share | | $ | (2.81 | ) | | $ | (0.91 | ) | | $ | (0.10 | ) |
| | | | | | |
Diluted loss per share: | | | | | | |
Allocation of earnings: | | | | | | |
Net loss | | $ | (88,407,995 | ) | | $ | (27,231,414 | ) | | $ | (2,010,548 | ) |
Weighted average common shares, including dilutive effect (a) | | 31,500,000 |
| | 30,000,000 |
| | 21,056,073 |
|
Diluted loss per share | | $ | (2.81 | ) | | $ | (0.91 | ) | | $ | (0.10 | ) |
| |
(a) | No incremental shares of potentially dilutive restricted stock awards were included for periods presented as their effect was antidulitive under the treasury stock method. |
Unaudited Pro Forma Earnings Per Share
The Company’s pro forma basic earnings per share amounts have been computed based on the weighted-average number of shares of common stock outstanding for the period, as if the common shares issued upon the conversion to Mammoth Inc. were outstanding for the entire year. A reconciliation of the components of pro forma basic and diluted earnings per common share is presented in the table below:
MAMMOTH ENERGY SERVICES, INC.
NOTES TO CONSOLIDATED FINANCIAL STATEMENTS
|
| | | | | | | | | | | | |
| | Year Ended December 31, |
| | 2016 | | 2015 | | 2014 |
Pro Forma C Corporation Data (unaudited): | | | | | | |
Net loss, as reported | | $ | (88,407,995 | ) | | $ | (27,231,414 | ) | | $ | (2,010,548 | ) |
Taxes on income earned as a non-taxable entity (Note 9) | | 13,750,827 |
| | 2,469,030 |
| | (5,207,628 | ) |
Taxes due to change to C corporation (Note 9) | | 53,088,861 |
| | — |
| | — |
|
Pro forma net loss | | $ | (21,568,307 | ) | | $ | (24,762,384 | ) | | $ | (7,218,176 | ) |
| | | | | | |
Basic loss per share: | | | | | | |
Allocation of earnings: | | | | | | |
Net loss | | $ | (21,568,307 | ) | | $ | (24,762,384 | ) | | $ | (7,218,176 | ) |
Weighted average common shares outstanding | | 37,500,000 |
| | 37,500,000 |
| | 21,056,073 |
|
Basic loss per share | | $ | (0.58 | ) | | $ | (0.66 | ) | | $ | (0.34 | ) |
| | | | | | |
Diluted loss per share: | | | | | | |
Allocation of earnings: | | | | | | |
Net loss | | $ | (21,568,307 | ) | | $ | (24,762,384 | ) | | $ | (7,218,176 | ) |
Weighted average common shares, including dilutive effect (a) | | 37,500,000 |
| | 37,500,000 |
| | 21,056,073 |
|
Diluted loss per share | | $ | (0.58 | ) | | $ | (0.66 | ) | | $ | (0.34 | ) |
| |
(a) | No incremental shares of potentially dilutive restricted stock awards were included for periods presented as their effect was antidulitive under the treasury stock method. |
Pro forma basic and diluted income (loss) per share has been computed by dividing pro forma net income (loss) attributable to the Company by the number of shares of common stock determined as if the shares of common stock issued were outstanding for all periods presented. Management believes that these assumptions provide a reasonable basis for presenting the pro forma effects.
| |
11. | Equity Based Compensation |
Upon formation of certain Operating Entities (including the acquired Stingray Entities), specified members of management (“Specified Members”) were granted the right to receive distributions from their respective Operating Entity, after the contribution member’s unreturned capital balance was recovered (referred to as “Payout” provision). Additionally, non-employee members were included in the award class (“Non-Employee Members”).
On November 24, 2014, the awards were modified in conjunction with the contribution of the Operating Entities to the Partnership. Awards are not granted in limited or general partner units. Agreements are for interests in the distributable earnings of Mammoth Holdings, Mammoth’s then majority limited partner unit holder.
On the IPO closing date, Mammoth Holding's unreturned capital balance was not fully recovered from its sale of common stock in the IPO. As a result, Payout did not occur and no compensation cost was recorded. Future offerings or sales of common stock that will recover outstanding unreturned capital remain not probable.
Payout is expected to occur following the sale by Mammoth Holding's of its shares of the Company's common stock, which is considered not probable until the event occurs. Therefore, for the awards that contained the Payout provision, no compensation cost was recognized as the distribution rights do not vest until Payout is reached. For the Specified Member awards, the unrecognized amount, which represents the fair value of the award as of the modification dates or grant date, was $5,618,552. For the Non-Employees Member awards, the unrecognized cost, which represents the fair value of the awards as of December 31, 2016, was $29,054,528.
MAMMOTH ENERGY SERVICES, INC.
NOTES TO CONSOLIDATED FINANCIAL STATEMENTS
| |
12. | Stock-Based Compensation |
The 2016 Plan authorizes the Company's Board of Directors or the compensation committee of the Company's Board of Directors to grant incentive restricted stock, restricted stock unit, stock appreciation rights, stock options and performance awards. There are 4.5 million shares of common stock reserved for issuance under the 2016 Plan.
Restricted Stock Units
The fair value of restricted stock unit awards was determined based on the fair market value of the Company's common stock on the date of the grant. This value is amortized over the vesting period.
A summary of the status and changes of the unvested shares of restricted stock under the 2016 Plan is presented below.
|
| | | | | | | | |
| | Number of Unvested Restricted Shares | | Weighted Average Grant-Date Fair Value | |
Unvested shares as of October 19, 2016 | | — |
| | $ | — |
| |
Granted | | 298,335 |
| | 14.97 |
| |
Vested | | (11,110 | ) | | (14.69 | ) | |
Forfeited | | (4,445 | ) | | (15.00 | ) | |
Unvested shares as of December 31, 2016 | | 282,780 |
| | $ | 14.98 |
| |
As of December 31, 2016, there was $3,878,325 of total unrecognized compensation cost related to the unvested restricted stock. The cost is expected to be recognized over a weighted average period of approximately twenty-one months.
Included in cost of revenue and selling, general and administrative expenses is stock-based compensation expense of $519,830 for the year ended December 31, 2016.
| |
13. | Acquisition of Stingray Entities |
Description of the Transaction
On November 24, 2014, the Partnership acquired all ownership interests in Stingray Pressure Pumping LLC (“Pressure Pumping”) and Stingray Logistics LLC (“Logistics”). Pressure Pumping was formed March 20, 2012 and Logistics was formed November 19, 2012, as Delaware limited liability companies. Both were formed by Wexford and Gulfport. The Partnership acquired Pressure Pumping and Logistics in exchange for limited partner interests. The acquisition of the Stingray Entities added to the Company's pressure pumping segment.
At the date of acquisition, the total ownership interest in Pressure Pumping and Logistics were converted to 31.96% (9.6 million common units) and 1.21% (0.4 million common units), respectively, of the Partnership's limited partnership interest. The fair value of the Stingray entities provided as consideration was determined with the assistance of external valuation experts as of acquisition date.
At the acquisition date, the components of the consideration transferred were as follows:
|
| | | | |
| | |
Consideration attributable to Stringray Pressure Pumping LLC (1) | | $ | 176,910,000 |
|
Consideration attributable to Stringray Logistics LLC (1) | | 6,720,000 |
|
Total consideration transferred | | $ | 183,630,000 |
|
| |
(1) | See Summary of acquired assets and liabilities below |
MAMMOTH ENERGY SERVICES, INC.
NOTES TO CONSOLIDATED FINANCIAL STATEMENTS
|
| | | | | | | | | | | |
| | Pressure Pumping | Logistics | | Total |
Cash and cash equivalents | | $ | 6,930,597 |
| $ | 128,471 |
| | $ | 7,059,068 |
|
Accounts receivable | | 25,904,279 |
| 2,164,859 |
| | 28,069,138 |
|
Inventories | | 1,205,059 |
| — |
| | 1,205,059 |
|
Other current assets | | 2,800,125 |
| 83,892 |
| | 2,884,017 |
|
Property, plant and equipment(1) | | 98,746,182 |
| 2,783,700 |
| | 101,529,882 |
|
Identifiable intangible assets - customer relationships(2) | | 33,610,000 |
| — |
| | 33,610,000 |
|
Identifiable intangible assets - trade names(2) | | 6,880,000 |
| 230,000 |
| | 7,110,000 |
|
Goodwill(3) | | 82,867,545 |
| 3,175,603 |
| | 86,043,148 |
|
Other Assets | | 207,057 |
| 4,000 |
| | 211,057 |
|
Total assets acquired | | $ | 259,150,844 |
| $ | 8,570,525 |
| | $ | 267,721,369 |
|
| | | | | |
Accounts payable and accrued liabilities | | $ | 33,428,913 |
| $ | 729,181 |
| | $ | 34,158,094 |
|
Income taxes payable | | 115,000 |
| $ | 5,000 |
| | 120,000 |
|
Long-term debt | | 48,696,931 |
| $ | 1,116,344 |
| | 49,813,275 |
|
Total liabilities assumed | | $ | 82,240,844 |
| $ | 1,850,525 |
| | $ | 84,091,369 |
|
Net assets acquired | | $ | 176,910,000 |
| $ | 6,720,000 |
| | $ | 183,630,000 |
|
| |
(1) | Property, plant and equipment fair value measurements were prepared by utilizing a combined fair market value and cost approach. The market approach relies on comparability of assets using market data information. The cost approach places emphasis on the physical components and characteristics of the asset. It places reliance on estimated replacement cost, depreciation and economic obsolescence. |
| |
(2) | Identifiable intangible assets were measured using a combination of income approaches. Trade names were valued using a "Relief-from-Royalty" method. Contractual and non-contractual customer relationships were valued using a "Multi-period excess earnings" method. Identifiable intangible assets will be amortized over 4-10 years. |
| |
(3) | Goodwill was the excess of the consideration transferred over the net assets recognized and represents the future economic benefits arising from other assets acquired that could not be individually identified and separately recognized. Goodwill recorded in connection with the acquisition is attributable to assembled workforces and future profitability based on the synergies expected to arise from the acquired entities. |
Since the acquisition date, the businesses acquired have provided the following earnings activity:
|
| | | | | | | | | | | | | | | | | | | | | |
| | 2016 | | 2015 | | 2014 |
| | Pressure Pumping | Logistics | | Pressure Pumping | Logistics | | Pressure Pumping | Logistics |
Revenues | | $ | 123,736,030 |
| $ | 4,393,991 |
| | $ | 166,869,663 |
| $ | 5,922,131 |
| | $ | 17,731,317 |
| $ | 635,024 |
|
Eliminations (1) | | (4,350 | ) | (4,349,075 | ) | | — |
| (5,922,131 | ) | | — |
| (635,024 | ) |
Revenues in consolidation | | 123,731,680 |
| 44,916 |
| | 166,869,663 |
| — |
| | 17,731,317 |
| — |
|
| | | | | | | | | |
Net income (loss) | | (2,207,333 | ) | (367,927 | ) | | (4,870,645 | ) | 630,999 |
| | (1,612,370 | ) | 97,525 |
|
Eliminations (2) | | 4,802,981 |
| (4,341,053 | ) | | 9,013,897 |
| (5,922,131 | ) | | 1,051,191 |
| (635,024 | ) |
Net income (loss) in consolidation | | 2,595,648 |
| (4,708,980 | ) | | 4,143,252 |
| (5,291,132 | ) | | (561,179 | ) | (537,499 | ) |
| |
(1) | Eliminations related to work performed on behalf of Stingray Pressure Pumping and Stingray Logistics |
| |
(2) | Eliminations relate to work performed on behalf of Stingray Pressure Pumping in addition to services provided by other Mammoth affiliates. |
The following table presents unaudited 2014 pro forma information for the Company as if the acquisition had occurred as of January 1, 2014:
|
| | | | |
| | 2014 |
Revenues | | $ | 381,868,708 |
|
Net loss | | (9,438,437 | ) |
MAMMOTH ENERGY SERVICES, INC.
NOTES TO CONSOLIDATED FINANCIAL STATEMENTS
The historical financial information was adjusted to give effect to the pro forma events that were directly attributable to the acquisition. For the year ended December 31, 2014, there were no transaction related costs expensed. The unaudited pro forma consolidated results are not necessarily indicative of what the consolidated results of operations actually would have been had the merger been completed on January 1, 2014. In addition, the unaudited pro forma consolidated results do not purport to project the future results of operations of the Company.
| |
14. | Acquisition of Lantern Rigs |
On January 29, 2014, Bison acquired five drilling rigs (“Rigs”) directly from the financial institutions that leased the Rigs to the previous owner, Lantern Drilling Company (“Lantern”). The Company has treated the acquisition of these assets as a business combination because the assets included a workforce and contract arrangements. The acquisition of these Rigs enhanced the Company's contract land and directional drilling segment. At the date of acquisition, the five rigs were valued at $47,225,000. The assets are classified in property, plant and equipment, net in the Consolidated Balance Sheets. After tax the total cash consideration paid for the assets was $50,557,053. The outflow of cash is presented in purchases of property and equipment in the Consolidated Statements of Cash Flow.
Since the acquisition date, the businesses acquired have provided the following earnings activity:
|
| | | | | | | | | | | | |
| | 2016 | | 2015 | | 2014 |
Revenues | | $ | 16,069,976 |
| | $ | 24,262,672 |
| | $ | 34,698,597 |
|
Net income (loss) | | (7,409,865 | ) | | 609,069 |
| | 6,873,499 |
|
The following table presents unaudited 2014 pro forma information for the Company as if the acquisition had occurred as of January 1, 2014:
|
| | | | |
| | 2014 |
Revenues | | $ | 262,461,809 |
|
Net loss | | (966,952 | ) |
The historical financial information was adjusted to give effect to the pro forma events that were directly attributable to the acquisition. For the year ended December 31, 2014, there were no transaction related costs expensed. The unaudited pro forma consolidated results are not necessarily indicative of what the consolidated results of operations actually would have been had the merger been completed on January 1, 2014. In addition, the unaudited pro forma consolidated results do not purport to project the future results of operations of the Company.
MAMMOTH ENERGY SERVICES, INC.
NOTES TO CONSOLIDATED FINANCIAL STATEMENTS
| |
15. | Related Party Transactions |
Transactions between the subsidiaries of the Company and the following companies are included in Related Party Transactions: Gulfport; Grizzly Oil Sands ULC (“Grizzly”); Taylor Frac LLC (“Taylor”); El Toro ("El Toro"); Stingray Cementing, LLC ("Cementing"); Diamondback E&P, LLC ("Diamondback"); Stingray Energy Services, LLC ("SR Energy"); Everest Operations Management, LLC ("Everest"); Elk City Yard, LLC ("Elk City Yard"); Double Barrel Downhole Technologies, LLC ("DBDHT"); Orange Leaf Holdings LLC ("Orange Leaf"); Caliber Investment Group, LLC ("Caliber"); and Dunvegan North Oilfield Services ULC (“Dunvegan”).
|
| | | | | | | | | | | | | | | | | |
| | REVENUES | | ACCOUNTS RECEIVABLE |
| | Years Ended December 31, | | At December 31, |
| | 2016 | 2015 | 2014 | | 2016 | 2015 |
Pressure Pumping and Gulfport | (a) | $ | 102,389,505 |
| $ | 124,311,189 |
| $ | 12,635,148 |
| | $ | 19,094,509 |
| $ | 16,218,713 |
|
Muskie and Gulfport | (b) | 25,783,253 |
| 38,181,970 |
| 3,133,822 |
| | 5,373,007 |
| 6,801,548 |
|
Muskie and Taylor | (c) | 2,540,050 |
| 335,252 |
| 111,398 |
| | 70,470 |
| 128,834 |
|
Panther Drilling and Gulfport | (d) | 3,011,259 |
| 3,703,140 |
| 8,302,362 |
| | 1,434,036 |
| 973,873 |
|
Energy Services and Gulfport | (e) | — |
| 2,548,418 |
| 1,473,094 |
| | — |
| 547,570 |
|
Lodging and Grizzly | (f) | 5,412 |
| 941,552 |
| 3,809,538 |
| | 274 |
| 906 |
|
Bison Drilling and El Toro | (g) | 371,873 |
| 521,121 |
| — |
| | — |
| — |
|
Panther Drilling and El Toro | (g) | 171,619 |
| 192,485 |
| 989,484 |
| | — |
| — |
|
Bison Trucking and El Toro | (g) | 130,000 |
| 144,905 |
| — |
| | — |
| — |
|
White Wing and El Toro | (g) | 20,431 |
| 12,719 |
| — |
| | — |
| — |
|
Energy Services and El Toro | (h) | 530,477 |
| 168,356 |
| — |
| | 108,386 |
| — |
|
Barracuda and Taylor | (i) | 452,378 |
| 122,131 |
| — |
| | 199,413 |
| 11,818 |
|
MRI and Cementing | (j) | 820 |
| 8,973 |
| — |
| | 820 |
| 8,973 |
|
White Wing and Diamondback | (k) | 1,650 |
| — |
| — |
| | — |
| — |
|
Coil Tubing and El Toro | (l) | 318,694 |
| — |
| — |
| | — |
| — |
|
Coil Tubing and SR Energy | (m) | 18,600 |
| — |
| — |
| | — |
| — |
|
Pressure Pumping and Cementing | (n) | 7,364 |
| — |
| — |
| | 950,678 |
| 198,076 |
|
Silverback and SR Energy | (o) | 11,356 |
| — |
| — |
| | 12,181 |
| 193,064 |
|
Panther and DBDHT | (p) | 157,940 |
| — |
| — |
| | 100,450 |
| — |
|
Panther and Diamondback | (q) | — |
| — |
| 168,673 |
| | — |
| — |
|
Bison Drilling and Diamondback | (q) | — |
| — |
| 232,299 |
| | — |
| — |
|
Bison Trucking and Diamondback | (q) | — |
| — |
| 3,176,607 |
| | — |
| — |
|
Energy Services and Pressure Pumping | (r) | — |
| — |
| 47,216 |
| | — |
| — |
|
Muskie and Pressure Pumping | (s) | — |
| — |
| 6,245,323 |
| | — |
| — |
|
Other Relationships | | — |
| — |
| — |
| | 715,341 |
| 560,406 |
|
| | $ | 135,922,681 |
| $ | 171,192,211 |
| $ | 40,324,964 |
| | $ | 28,059,565 |
| $ | 25,643,781 |
|
| |
a. | Pressure Pumping provides pressure pumping, stimulation and related completion services to Gulfport. |
| |
b. | Muskie has agreed to sell and deliver, and Gulfport has agreed to purchase, specified annual and monthly amounts of natural sand proppant, subject to certain exceptions specified in the agreement, and pay certain costs and expenses. |
| |
c. | Taylor, an entity under common ownership with the Company and managed by the Company, has purchased natural sand proppant from Muskie. Natural sand proppant is sold to Taylor at a market-based per ton arrangement on an as-needed basis. |
| |
d. | Panther Drilling performs drilling services for Gulfport pursuant to a master service agreement. |
| |
e. | Energy Services performs completion and production services for Gulfport pursuant to a master service agreement. |
| |
f. | Lodging provides remote accommodation and food services to Grizzly, an entity owned approximately 75% by affiliates of Wexford and approximately 25% by Gulfport. |
| |
g. | The contract land and directional drilling segment provides services for El Toro, an entity controlled by Wexford, pursuant to a master service agreement. |
| |
h. | Energy Services performs completion and production services for El Toro pursuant to a master service agreement. |
| |
i. | Barracuda receives fees from Taylor for the usage of its rail transloading facility. |
| |
j. | MRI provides iron inspection services to Cementing. |
| |
k. | White Wing provides rental services to Diamondback. |
| |
l. | Coil Tubing provides El Toro services in connection with completion activities. |
| |
m. | Coil Tubing provides rental services to SR Energy. |
| |
n. | Pressure Pumping provides services and materials to Cementing. |
| |
o. | Silverback provides services and materials to SR Energy. |
| |
p. | Panther provides services and materials to DBDHT. |
| |
q. | The contract land and directional drilling segment performed drilling services and sold or leased goods, equipment or facilities to Diamondback to a master service agreement. |
| |
r. | Prior to the acquisition of the Stingray Entities, Energy Services rented equipment from Pressure Pumping. |
| |
s. | Prior to the acquisition of the Stingray Entities, Muskie sold natural sand proppant to Pressure Pumping. |
MAMMOTH ENERGY SERVICES, INC.
NOTES TO CONSOLIDATED FINANCIAL STATEMENTS
|
| | | | | | | | | | | | | | | | | |
| | COST OF REVENUE | | ACCOUNTS PAYABLE |
| | Years Ended December 31, | | At December 31, |
| | 2016 | 2015 | 2014 | | 2016 | 2015 |
Pressure Pumping and Taylor | (a) | $ | 4,256,832 |
| $ | 2,685,202 |
| $ | 1,029,974 |
| | $ | — |
| $ | 17,552 |
|
Muskie and Taylor | (a) | 20,586,715 |
| 20,510,977 |
| 867,428 |
| | 2,119,084 |
| 6,505,833 |
|
Barracuda and Taylor | (b) | 255,029 |
| 81,039 |
| — |
| | 111,738 |
| 26,720 |
|
Panther and DBDHT | (c) | 48,998 |
| 101,206 |
| 250,322 |
| | — |
| 48,998 |
|
Bison Trucking and Diamondback | (d) | 169,886 |
| 165,951 |
| 112,330 |
| | — |
| 12,077 |
|
Energy Services and Elk City Yard | (e) | 106,800 |
| 106,800 |
| — |
| | — |
| — |
|
Barracuda and SR Energy | (f) | 30,722 |
| — |
| — |
| | 6,279 |
| — |
|
Stingray Entities and Taylor | (g) | — |
| 32,261 |
| — |
| | — |
| 32,261 |
|
Stingray Entities and SR Energy | (h) | 679,550 |
| 932,896 |
| 42,545 |
| | 161,065 |
| 12,208 |
|
Lodging and Dunvegan | (i) | 8,574 |
| 71,980 |
| 116,805 |
| | 3,199 |
| 304,746 |
|
Bison Drilling and El Toro | (j) | 5,000 |
| — |
| — |
| | — |
| — |
|
Silverback and SR Energy | (k) | 13,701 |
| — |
| — |
| | 6,801 |
| — |
|
Muskie and Everest | (l) | — |
| — |
| 1,969,439 |
| | — |
| — |
|
Bison Drilling and Everest | (l) | — |
| — |
| 218,589 |
| | — |
| — |
|
Muskie and Hopedale | (m) | 2,455 |
| — |
| 453,080 |
| | — |
| — |
|
| | $ | 26,164,262 |
| $ | 24,688,312 |
| $ | 5,060,512 |
| | $ | 2,408,166 |
| $ | 6,960,395 |
|
| | | | | | | |
| | SELLING, GENERAL AND ADMINISTRATIVE COSTS | | | |
Consolidated and Everest | (l) | $ | 251,122 |
| $ | 495,320 |
| $ | 2,297,106 |
| | $ | 12,668 |
| $ | 28,528 |
|
Consolidated and Taylor | (n) | 160,622 |
| 287,403 |
| — |
| | — |
| — |
|
Consolidated and Wexford | (o) | 380,551 |
| 381,070 |
| 457,771 |
| | 13,197 |
| 9,006 |
|
Mammoth and Orange Leaf | (p) | 102,515 |
| 49,892 |
| — |
| | — |
| — |
|
Pressure Pumping and Caliber | (q) | — |
| 24,306 |
| — |
| | — |
| — |
|
| | $ | 894,810 |
| $ | 1,237,991 |
| $ | 2,754,877 |
| | $ | 25,865 |
| $ | 37,534 |
|
| | | | | | $ | 2,434,031 |
| $ | 6,997,929 |
|
| |
a. | Taylor, an entity under common ownership with the Company and managed by the Company, sells natural sand proppant to Muskie and Pressure Pumping. Natural sand proppant is sold to Muskie at a market-based per ton arrangement on an as-needed basis to supplement sand provided by its facility (when in operation) if any orders placed by its customers are not able to be readily fulfilled, either because of volume or specific grades of sand requested. |
| |
b. | From time to time, Barracuda pays for goods and services on behalf of Taylor. |
| |
c. | Panther rents rotary steerable equipment in connection with its directional drilling services from DBDHT. |
| |
d. | Bison Trucking leases office space from Diamondback in Midland, Texas. The office space is leased through early 2017. |
| |
e. | Energy Services leases property from Elk City Yard. |
| |
f. | From time to time, Barracuda rents equipment from SR Energy. |
| |
g. | The Stingray Entities utilizes Taylor's transload facility. |
| |
h. | Pressure Pumping rents equipment from SR Energy. |
| |
i. | Dunvegan provides technical and administrative services and pays for goods and services on behalf of Lodging. |
| |
j. | Bison Drilling leases space from El Toro for storage of a rig. |
| |
k. | Silverback rents equipment from SR Energy. |
| |
l. | Everest has historically provided office space and certain technical, administrative and payroll services to the Company and the Company has reimbursed Everest in amounts determined by Everest based on estimates of the amount of office space provided and the amount of employees’ time spent performing services for the Company. In 2014, Everest provided personnel to support operational functions in addition to significant technical and advisory support. |
| |
m. | Muskie utilizes Hopedale's transload facility. |
| |
n. | Taylor provides certain administrative and analytical services to the Company. |
| |
o. | Wexford provides certain administrative and analytical services to the Company and, from time to time, the Company pays for goods and services on behalf of Wexford. |
| |
p. | Orange Leaf leases office space to Mammoth Inc. |
| |
q. | Caliber leases office space to Pressure Pumping. |
MAMMOTH ENERGY SERVICES, INC.
NOTES TO CONSOLIDATED FINANCIAL STATEMENTS
| |
16. | Commitments and Contingencies |
The Company leases real estate, rail cars and other equipment under long-term operating leases with varying terms and expiration dates through 2025. Aggregate future minimum lease payments under these non-cancelable operating leases in effect at December 31, 2016 are as follows:
|
| | | | |
Year ended December 31: | | Amount |
2017 | | $ | 3,028,467 |
|
2018 | | 2,339,084 |
|
2019 | | 1,918,489 |
|
2020 | | 1,392,803 |
|
2021 | | 1,392,803 |
|
Thereafter | | 3,987,729 |
|
| | $ | 14,059,375 |
|
For the years ended December 31, 2016, 2015 and 2014, the Company recognized rent expense of $3,956,791, $4,457,183 and $3,180,205, respectively.
The Company entered into a purchase agreement in 2014 with a sand supplier to begin January 1, 2015 and end December 31, 2016. The Company is subject to an annual commitment of 200,000 tons of sand. During June 2016, the Company paid a deposit of $600,000 to the sand supplier to be netted against future purchases of sand under this contract and deferred the commitment until 2017. The Company has one additional unilateral option to extend for one additional year with a further deposit of $600,000. As of December 31, 2016, the future commitment for 2017 under this agreement is $2,200,000.
The Company entered into agreements in 2016 to acquire new high pressure fracturing units and other capital equipment. The future commitment under these agreements is $18,554,769 as of December 31, 2016.
The Company has various letters of credit totaling $2,090,560 to secure rail car lease payments. These letters of credit were issued under the Company's revolving credit agreement which is collateralized by substantially all of the assets of the Company.
The Company partially insures some workers’ compensation and auto claims, which includes medical expenses, lost time and temporary or permanent disability benefits. As of December 31, 2016 and 2015, the policy requires a deductible per occurrence of $250,000 and $100,000, respectively. The Company establishes liabilities for the unpaid deductible portion of claims incurred relating to workers’ compensation and auto liability based on estimates. As of December 31, 2016 and 2015, the policies contained an aggregate stop loss of $2,000,000 and $1,900,000, respectively. As of December 31, 2016 and 2015, accrued claims were $971,351 and $739,775, respectively. These estimates may change in the near term as actual claims continue to develop. In connection with the insurance programs, letters of credit of $1,285,000 and $1,176,000 as of December 31, 2016 and 2015, respectively, have been issued supporting the retained risk exposure. As of both December 31, 2016 and 2015, these letters of credit were issued under the Company's revolving credit agreement which is collateralized by substantially all of the assets of the Company.
The Company is routinely involved in state and local tax audits. During 2015, the State of Ohio assessed taxes on the purchase of equipment the Company believes is exempt under state law. The Company has appealed the assessment and a hearing was scheduled for November 30, 2016. In November 2016, the State of Ohio deferred the hearing until 2017. While the Company is not able to predict the outcome of the appeal, this matter is not expected to have a material adverse effect on the financial position or results of operations of the Company.
On June 3, 2015, a punitive class and collective action lawsuit alleging that Pressure Pumping failed to pay a class of workers overtime in compliance with the Fair Labor Standards Act and Ohio law was filed titled William Crigler, et al v. Stingray Pressure Pumping, LLC in the U.S. District Court Southern District of Ohio Eastern Division. The Company submitted a settlement offer to the plaintiff that was accepted and is expected to be payable in 2017. This settlement will not have a material impact on the Company’s financial position, results of operations or cash flows.
MAMMOTH ENERGY SERVICES, INC.
NOTES TO CONSOLIDATED FINANCIAL STATEMENTS
On October 12, 2015, a putative class and collective action lawsuit alleging that Energy Services failed to pay a class of workers overtime in compliance with the Fair Labor Standards Act and Oklahoma law was filed titled William Reynolds, individually and on behalf of all others similarly situated v. Redback Energy Services LLC in the U.S. District Court for the Western District of Oklahoma. The Company is evaluating the background facts and at this time is not able to predict the outcome of this lawsuit or whether it will have a material impact on the Company’s financial position, results of operations or cash flows.
On December 2, 2015, a putative class and collective action lawsuit alleging that Bison Drilling failed to pay a class of workers overtime in compliance with the Fair Labor Standards Act and Texas law was filed titled John Talamentez, individually and on behalf of all others similarly situated v. Bison Drilling and Field Services, LLC in the U.S. District Court Western District of Texas Midland/Odessa Division. The Company is evaluating the background facts and at this time is not able to predict the outcome of this lawsuit or whether it will have a material impact on the Company’s financial position, results of operations or cash flows.
On December 16, 2015, a lawsuit alleging wrongful death was filed titled Cecilia R.G. Uballe and Sabrina Barber, beneficiaries of Eseciel D. Uballe, Deceased v. Bison Trucking LLC in the U.S. District Court of Midland Texas. On December 5, 2016, the Company settled this matter. This resolution did not cause a material impact on the Company’s financial position, results of operations or cash flows.
On February 12, 2016, a putative lawsuit alleging that Energy Services failed to pay a class of workers in compliance with the Fair Labor Standards Act was filed titled Brian Croniser vs. Redback Energy Services LLC in the U.S. District Court Southern District of Ohio. The Company is evaluating the background facts at this time and are not able to predict the outcome of this lawsuit or whether it will have a material impact on the Company’s financial position, results of operations or cash flows.
On June 22, 2016, a putative, Title VII discrimination, and Oklahoma anti-discrimination lawsuit alleging that Redback Energy Services was in violation of the previously mentioned federal and state laws. The lawsuit was filed titled Earl Richardson and Keary Johnson v. Redback Energy Services LLC in the U.S. District Court for the Western District of Oklahoma. The Company is evaluating the background facts at this time and is not able to predict the outcome of this lawsuit or whether it will have a material impact on the Company’s financial position, results of operations or cash flows.
On August 1, 2016, a putative class and collective action lawsuit alleging that Energy Services failed to pay a class of workers overtime in compliance with the Fair Labor Standards Act and Texas law was filed titled Michael Caffey, individually and on behalf of all others similarly situated v. Redback Energy Services LLC in the U.S. District Court for the Western District of Texas. The Company is evaluating the background facts and at this time is not able to predict the outcome of this lawsuit or whether it will have a material impact on the Company’s financial position, results of operations or cash flows.
On September 27, 2016, a putative lawsuit alleging that Energy Services failed to pay a class of workers in compliance with the Fair Labor Standards Act was filed titled Michael Drake vs. Redback Coil Tubing LLC, et al in the U.S. District Court Western District of Texas. The Company is evaluating the background facts at this time and is not able to predict the outcome of this lawsuit or whether it will have a material impact on the Company’s financial position, results of operations or cash flows.
The Company is involved in various other legal proceedings in the ordinary course of business. Although we cannot predict the outcome of these proceedings, legal matters are subject to inherent uncertainties and there exists the possibility that the ultimate resolution of these matters could have a material adverse effect on our business, financial condition, results of operations or cash flows.
Defined contribution plan
The Company sponsors a 401(k) defined contribution plan for the benefit of substantially all employees at their date of hire. The plan allows eligible employees to contribute up to 92% of their annual compensation, not to exceed annual limits established by the federal government. The Company makes discretionary matching contributions of up to 4% of an employee’s compensation and may make additional discretionary contributions for eligible employees. For the years ended December 31, 2016, 2015 and 2014 the Company paid $102,230, $1,514,478 and $1,270,081, respectively, in contributions to the plan.
MAMMOTH ENERGY SERVICES, INC.
NOTES TO CONSOLIDATED FINANCIAL STATEMENTS
The Company is organized into five reportable segments based on the nature of services provided and the basis in which management makes business and operating decisions. The Company principally provides oilfield services in connection with on-shore drilling of oil and natural gas wells for small to large domestic independent oil and nature gas producers. The Company’s five segments consist of pressure pumping services ("Pressure Pumping"), well services ("Well Services"), natural sand proppant ("Sand"), contract land and directional drilling services ("Drilling") and other energy services ("Other Energy Services").
The Company's Chief Executive Officer and Chief Financial Officer comprise the Company's Chief Operating Decision Maker function ("CODM"). Segment information is prepared on the same basis that our CODM manages the segments, evaluates the segment financial statements, and makes key operating and resource utilization decisions. Segment evaluation is determined on a quantitative basis based on a function of revenue and earnings before interest, other expense (income), impairment, taxes and depreciation and amortization as well as a qualitative basis, such as nature of the product and service offerings, types of customers.
Based on the CODM's assessment, effective December 31, 2016, the Company reorganized the reportable segments to align with its new management reporting structure and business activities. Prior to this reorganization, the existing reportable segments were comprised of four segments for financial reporting purposes: land and directional drilling services, completion and production services, completion and production - natural sand proppant and remote accommodation services. As a result of this change, there are five reportable segments for financial reporting purposes as described above. Historical information in this Note to the financial statements has been revised to reflect the new reportable segment.
Additionally, given that the Company is a C Corporation that will file a consolidated income tax returns for periods following the contribution that occurred in October 2016 (See Note 1), the Company deems loss (income) before income taxes to be a more meaningful representation of operational performance. Historical information in this Note to the financial statements has been revised to reflect the presentation methodology.
The following table sets forth certain financial information with respect to the Company’s reportable segments:
|
| | | | | | | | | | | | | | | | | | |
| Completion and Production | | | | |
Year Ended December 31, 2016 | Pressure Pumping | Well Services | Sand | Drilling | Other Energy Services | Total |
Revenue from external customers | $ | 21,446,803 |
| $ | 9,157,042 |
| $ | 5,433,141 |
| $ | 28,177,737 |
| $ | 30,861,317 |
| $ | 95,076,040 |
|
Revenue from related parties | $ | 102,861,423 |
| $ | 867,771 |
| $ | 28,323,303 |
| $ | 3,864,772 |
| $ | 5,412 |
| $ | 135,922,681 |
|
Cost of revenue | $ | 86,808,742 |
| $ | 13,540,309 |
| $ | 28,166,829 |
| $ | 31,847,969 |
| $ | 13,186,060 |
| $ | 173,549,909 |
|
Selling, general and administrative expenses | $ | 4,327,599 |
| $ | 2,336,002 |
| $ | 2,019,641 |
| $ | 5,624,705 |
| $ | 2,423,028 |
| $ | 16,730,975 |
|
Earnings before interest, other expense (income), impairment, taxes and depreciation and amortization | $ | 33,171,885 |
| $ | (5,851,498 | ) | $ | 3,569,974 |
| $ | (5,430,165 | ) | $ | 15,257,641 |
| $ | 40,717,837 |
|
Other expense (income) | $ | 26,743 |
| $ | (565,966 | ) | $ | 2,321 |
| $ | 247,620 |
| $ | 37,043 |
| $ | (252,239 | ) |
Interest expense | $ | 599,147 |
| $ | 134,007 |
| $ | 49,518 |
| $ | 2,828,753 |
| $ | 100,032 |
| $ | 3,711,457 |
|
Depreciation and amortization | $ | 37,012,902 |
| $ | 5,127,879 |
| $ | 4,078,844 |
| $ | 21,512,117 |
| $ | 2,179,116 |
| $ | 69,910,858 |
|
Impairment of long-lived assets | $ | 138,587 |
| $ | 1,384,751 |
| $ | — |
| $ | 347,547 |
| $ | — |
| $ | 1,870,885 |
|
Loss (income) before income taxes | $ | (4,605,494 | ) | $ | (11,932,169 | ) | $ | (560,709 | ) | $ | (30,366,202 | ) | $ | 12,941,450 |
| $ | (34,523,124 | ) |
Provision (benefit) for income taxes | $ | — |
| $ | 50,265,203 |
| $ | 3,716 |
| $ | — |
| $ | 3,615,952 |
| $ | 53,884,871 |
|
Net income (loss) | $ | (4,605,494 | ) | $ | (62,197,372 | ) | $ | (564,425 | ) | $ | (30,366,202 | ) | $ | 9,325,498 |
| $ | (88,407,995 | ) |
Total expenditures for property, plant and equipment | $ | 7,673,187 |
| $ | 404,612 |
| $ | 106,252 |
| $ | 2,709,478 |
| $ | 424,380 |
| $ | 11,317,909 |
|
Goodwill | $ | 86,043,148 |
| $ | — |
| $ | — |
| $ | — |
| $ | — |
| $ | 86,043,148 |
|
Intangible assets, net | $ | 21,435,058 |
| $ | 131,771 |
| $ | — |
| $ | — |
| $ | — |
| $ | 21,566,829 |
|
Total assets | $ | 195,521,027 |
| $ | 66,043,726 |
| $ | 26,517,973 |
| $ | 99,867,691 |
| $ | 32,603,418 |
| $ | 420,553,835 |
|
MAMMOTH ENERGY SERVICES, INC.
NOTES TO CONSOLIDATED FINANCIAL STATEMENTS
|
| | | | | | | | | | | | | | | | | | |
| Completion and Production | | | | |
Year Ended December 31, 2015 | Pressure Pumping | Well Services | Sand | Drilling | Other Energy Services | Total |
Revenue from external customers | $ | 45,538,393 |
| $ | 26,134,568 |
| $ | 14,272,981 |
| $ | 68,457,719 |
| $ | 34,340,821 |
| $ | 188,744,482 |
|
Revenue from related parties | $ | 124,442,293 |
| $ | 2,716,773 |
| $ | 38,517,222 |
| $ | 4,574,370 |
| $ | 941,553 |
| $ | 171,192,211 |
|
Cost of revenue | $ | 131,717,344 |
| $ | 28,144,431 |
| $ | 43,890,437 |
| $ | 57,489,608 |
| $ | 15,105,497 |
| $ | 276,347,317 |
|
Selling, general and administrative expenses | $ | 4,901,459 |
| $ | 2,285,684 |
| $ | 2,405,350 |
| $ | 8,573,174 |
| $ | 2,375,881 |
| $ | 20,541,548 |
|
Earnings before interest, other expense, impairment, taxes and depreciation and amortization | $ | 33,361,883 |
| $ | (1,578,774 | ) | $ | 6,494,416 |
| $ | 6,969,307 |
| $ | 17,800,996 |
| $ | 63,047,828 |
|
Other expense (income) | $ | 66,889 |
| $ | 686,617 |
| $ | (88,976 | ) | $ | 1,121,093 |
| $ | 372,141 |
| $ | 2,157,764 |
|
Interest expense | $ | 1,859,195 |
| $ | 429,061 |
| $ | 51,476 |
| $ | 2,890,130 |
| $ | 60,959 |
| $ | 5,290,821 |
|
Interest income | $ | — |
| $ | — |
| $ | 98,056 |
| $ | — |
| $ | 436 |
| $ | 98,492 |
|
Depreciation and amortization | $ | 35,728,715 |
| $ | 5,696,547 |
| $ | 4,200,809 |
| $ | 24,626,705 |
| $ | 2,141,106 |
| $ | 72,393,882 |
|
Impairment of long-lived assets | $ | 1,213,885 |
| $ | 88,247 |
| $ | 1,904,981 |
| $ | 8,917,240 |
| $ | — |
| $ | 12,124,353 |
|
Loss (income) before income taxes | $ | (5,506,801 | ) | $ | (8,479,246 | ) | $ | 524,182 |
| $ | (30,585,861 | ) | $ | 15,227,226 |
| $ | (28,820,500 | ) |
Provision (benefit) for income taxes | $ | 72,435 |
| $ | 4,454 |
| $ | — |
| $ | (184,523 | ) | $ | (1,481,452 | ) | $ | (1,589,086 | ) |
Net income (loss) | $ | (5,579,236 | ) | $ | (8,483,700 | ) | $ | 524,182 |
| $ | (30,401,338 | ) | $ | 16,708,678 |
| $ | (27,231,414 | ) |
Total expenditures for property, plant and equipment | $ | 4,169,678 |
| $ | 6,768,143 |
| $ | 171,202 |
| $ | 12,650,831 |
| $ | 2,491,821 |
| $ | 26,251,675 |
|
Goodwill | $ | 86,043,148 |
| $ | — |
| $ | — |
| $ | — |
| $ | — |
| $ | 86,043,148 |
|
Intangible assets, net | $ | 30,478,558 |
| $ | 159,271 |
| $ | — |
| $ | — |
| $ | — |
| $ | 30,637,829 |
|
Total assets | $ | 226,690,841 |
| $ | 41,481,415 |
| $ | 32,726,899 |
| $ | 118,227,357 |
| $ | 31,859,058 |
| $ | 450,985,570 |
|
|
| | | | | | | | | | | | | | | | | | |
| Completion and Production | | | | |
Year Ended December 31, 2014 | Pressure Pumping | Well Services | Sand | Drilling | Other Energy Services | Total |
Revenue from external customers | $ | 12,144,538 |
| $ | 43,732,782 |
| $ | 36,859,731 |
| $ | 109,295,518 |
| $ | 17,168,471 |
| $ | 219,201,040 |
|
Revenue from related parties | $ | 12,635,148 |
| $ | 1,520,310 |
| $ | 9,490,543 |
| $ | 12,869,425 |
| $ | 3,809,538 |
| $ | 40,324,964 |
|
Cost of revenue | $ | 17,293,057 |
| $ | 31,715,681 |
| $ | 38,815,543 |
| $ | 93,571,050 |
| $ | 9,673,570 |
| $ | 191,068,901 |
|
Selling, general and administrative expenses | $ | 1,409,618 |
| $ | 2,339,024 |
| $ | 2,178,867 |
| $ | 9,763,922 |
| $ | 1,336,432 |
| $ | 17,027,863 |
|
Earnings before interest, other expense, impairment, taxes and depreciation and amortization | $ | 6,077,011 |
| $ | 11,198,387 |
| $ | 5,355,864 |
| $ | 18,829,971 |
| $ | 9,968,007 |
| $ | 51,429,240 |
|
Other expense | $ | 1,744,695 |
| $ | 777,382 |
| $ | 1,099,284 |
| $ | 1,539,279 |
| $ | 563,856 |
| $ | 5,724,496 |
|
Interest expense | $ | 386,618 |
| $ | 831,508 |
| $ | 127,988 |
| $ | 3,194,061 |
| $ | 63,420 |
| $ | 4,603,595 |
|
Interest expense from related parties | $ | — |
| $ | — |
| $ | 184,479 |
| $ | — |
| $ | — |
| $ | 184,479 |
|
Interest income | $ | — |
| $ | — |
| $ | 208,519 |
| $ | — |
| $ | 5,622 |
| $ | 214,141 |
|
Depreciation and amortization | $ | 4,015,572 |
| $ | 4,768,024 |
| $ | 3,867,024 |
| $ | 21,319,617 |
| $ | 1,656,928 |
| $ | 35,627,165 |
|
Loss (income) before income taxes | $ | (69,874 | ) | $ | 4,821,473 |
| $ | 285,608 |
| $ | (7,222,986 | ) | $ | 7,689,425 |
| $ | 5,503,646 |
|
Provision (benefit) for income taxes | $ | 10,897 |
| $ | 18,226 |
| $ | 4,826 |
| $ | 77,576 |
| $ | 7,402,669 |
| $ | 7,514,194 |
|
Net income (loss) | $ | (80,771 | ) | $ | 4,803,247 |
| $ | 280,782 |
| $ | (7,300,562 | ) | $ | 286,756 |
| $ | (2,010,548 | ) |
Total expenditures for property, plant and equipment | $ | 180,466 |
| $ | 11,441,285 |
| $ | 4,587,464 |
| $ | 85,801,345 |
| $ | 9,679,496 |
| $ | 111,690,056 |
|
Goodwill | $ | 86,131,395 |
| $ | — |
| $ | — |
| $ | — |
| $ | — |
| $ | 86,131,395 |
|
Intangible assets, net | $ | 39,809,101 |
| $ | 186,770 |
| $ | — |
| $ | — |
| $ | — |
| $ | 39,995,871 |
|
Total assets | $ | 275,859,470 |
| $ | 39,977,056 |
| $ | 40,734,019 |
| $ | 185,218,626 |
| $ | 38,925,705 |
| $ | 580,714,876 |
|
The pressure pumping services segment provides hydraulic fracturing. The well services segment provides coil tubing, flowback and equipment rental services. The sand segment sells, distributes and is capable of producing sand for use in hydraulic fracturing. The contract land and directional drilling services segment provides vertical, horizontal and directional drilling services. The other energy services segment provides housing, kitchen and dining, and recreational service facilities for oilfield workers that are located in remote areas away from readily available lodging. The pressure pumping and well service segments primarily services in the Utica Shale of Eastern Ohio, Marcellus Shale in Pennsylvania, Eagle Ford and Permian basin in Texas and mid-continent region. The natural sand proppant segment
MAMMOTH ENERGY SERVICES, INC.
NOTES TO CONSOLIDATED FINANCIAL STATEMENTS
primarily services the Utica Shale and Montney Shale in British Columbia and Alberta, Canada. The contract land and directional drilling services segment primarily services the Permian Basin in West Texas. The other energy services segment primarily services Canada.
18. Quarterly Financial Data (unaudited)
|
| | | | | | | | | | | | | | | |
| Three Months Ended | |
| March 31, | June 30, | September 30, | December 31, | Total |
| 2016 | 2016 | 2016 | 2016 | |
Revenue from external customers | $ | 28,971,935 |
| $ | 20,070,966 |
| $ | 20,009,086 |
| $ | 26,024,053 |
| $ | 95,076,040 |
|
Revenue from related parties | $ | 5,531,569 |
| $ | 48,871,322 |
| $ | 42,757,132 |
| $ | 38,762,658 |
| $ | 135,922,681 |
|
Cost of revenue | $ | 32,897,220 |
| $ | 51,375,378 |
| $ | 42,733,976 |
| $ | 46,543,335 |
| $ | 173,549,909 |
|
Selling, general and administrative expenses | $ | 3,255,064 |
| $ | 4,795,729 |
| $ | 3,001,809 |
| $ | 5,678,373 |
| $ | 16,730,975 |
|
Earnings before other expense (income), interest, depreciation and amortization, impairment and taxes | $ | (1,648,780 | ) | $ | 12,771,181 |
| $ | 17,030,433 |
| $ | 12,565,003 |
| $ | 40,717,837 |
|
Other expense (income) | $ | (18,192 | ) | $ | (676,496 | ) | $ | 242,893 |
| $ | 199,556 |
| $ | (252,239 | ) |
Interest expense | $ | 1,191,895 |
| $ | 917,310 |
| $ | 932,749 |
| $ | 669,503 |
| $ | 3,711,457 |
|
Depreciation and amortization | $ | 17,413,591 |
| $ | 18,253,792 |
| $ | 17,148,430 |
| $ | 17,095,045 |
| $ | 69,910,858 |
|
Impairment of long-lived assets | $ | — |
| $ | 1,870,885 |
| $ | — |
| $ | — |
| $ | 1,870,885 |
|
Loss before income taxes | $ | (20,236,074 | ) | $ | (7,594,310 | ) | $ | (1,293,639 | ) | $ | (5,399,101 | ) | $ | (34,523,124 | ) |
Provision (benefit) for income taxes | $ | 894,360 |
| $ | 789,376 |
| $ | 1,055,960 |
| $ | 51,145,175 |
| $ | 53,884,871 |
|
Net loss | $ | (21,130,434 | ) | $ | (8,383,686 | ) | $ | (2,349,599 | ) | $ | (56,544,276 | ) | $ | (88,407,995 | ) |
| | | | | |
Net loss per share (basic and diluted) (Note 10) | $ | (0.70 | ) | $ | (0.28 | ) | $ | (0.08 | ) | $ | (1.57 | ) | $ | (2.81 | ) |
Weighted average number of shares outstanding (Note 10) | 30,000,000 |
| 30,000,000 |
| 30,000,000 |
| 35,951,087 |
| 31,500,000 |
|
|
| | | | | | | | | | | | | | | |
| Three Months Ended | |
| March 31, | June 30, | September 30, | December 31, | Total |
| 2015 | 2015 | 2015 | 2015 | |
Revenue from external customers | $ | 68,265,763 |
| $ | 56,780,307 |
| $ | 44,151,122 |
| $ | 19,547,290 |
| $ | 188,744,482 |
|
Revenue from related parties | $ | 44,103,719 |
| $ | 50,786,000 |
| $ | 42,045,370 |
| $ | 34,257,122 |
| $ | 171,192,211 |
|
Cost of revenue | $ | 80,748,069 |
| $ | 85,115,293 |
| $ | 70,360,228 |
| $ | 40,123,727 |
| $ | 276,347,317 |
|
Selling, general and administrative expenses | $ | 4,912,574 |
| $ | 4,938,008 |
| $ | 4,191,917 |
| $ | 6,499,049 |
| $ | 20,541,548 |
|
Earnings before other expense (income), interest, depreciation and amortization, impairment and taxes | $ | 26,708,839 |
| $ | 17,513,006 |
| $ | 11,644,347 |
| $ | 7,181,636 |
| $ | 63,047,828 |
|
Other expense (income) | $ | 896,518 |
| $ | 1,195,967 |
| $ | 142,029 |
| $ | (76,750 | ) | $ | 2,157,764 |
|
Interest income | $ | 46,678 |
| $ | 51,564 |
| $ | 250 |
| $ | — |
| $ | 98,492 |
|
Interest expense | $ | 1,532,394 |
| $ | 1,273,936 |
| $ | 1,376,424 |
| $ | 1,108,067 |
| $ | 5,290,821 |
|
Depreciation and amortization | $ | 17,743,210 |
| $ | 17,993,622 |
| $ | 17,959,432 |
| $ | 18,697,618 |
| $ | 72,393,882 |
|
Impairment of long-lived assets | $ | — |
| $ | 4,470,781 |
| $ | 908,456 |
| $ | 6,745,116 |
| $ | 12,124,353 |
|
Loss (income) before income taxes | $ | 6,583,395 |
| $ | (7,369,736 | ) | $ | (8,741,744 | ) | $ | (19,292,415 | ) | $ | (28,820,500 | ) |
Provision (benefit) for income taxes | $ | 1,164,943 |
| $ | 408,193 |
| $ | (4,250,643 | ) | $ | 1,088,421 |
| $ | (1,589,086 | ) |
Net income (loss) | $ | 5,418,452 |
| $ | (7,777,929 | ) | $ | (4,491,101 | ) | $ | (20,380,836 | ) | $ | (27,231,414 | ) |
| | | | | |
Net loss per share (basic and diluted) (Note 10) | $ | 0.18 |
| $ | (0.26 | ) | $ | (0.15 | ) | $ | (0.68 | ) | $ | (0.91 | ) |
Weighted average number of shares outstanding (Note 10) | 30,000,000 |
| 30,000,000 |
| 30,000,000 |
| 30,000,000 |
| 30,000,000 |
|
Subsequent to December 31, 2016, the Company entered into railcar lease agreements with aggregate commitments of $2.0 million.
MAMMOTH ENERGY SERVICES, INC.
NOTES TO CONSOLIDATED FINANCIAL STATEMENTS
In February 2017, the Company ordered additional new high pressure fracturing units and related equipment with an aggregate cost of $35.2 million with delivery expected during 2017. Additionally, subsequent to December 31, 2016, the Company ordered $6.4 million in other equipment for our natural sand proppant and contract land and directional drilling service segments.
On February 21, 2017, the Company granted 375,000 restricted stock units ("RSUs"). The RSUs vest in three substantially equal annual installments beginning on the first anniversary of the grant.
|
| | |
| | |
Exhibit Number | | Exhibit Description |
3.1 | | Amended and Restated Certificate of Incorporation of the Company (incorporated by reference to Exhibit 3.1 to the Company’s Current Report on Form 8-K (File No. 001-37917), filed with the SEC on November 15, 2016). |
3.2 | | Amended and Restated Bylaws of the Company (incorporated by reference to Exhibit 3.2 to the Company’s Current Report on Form 8-K (File No. 001-37917), filed with the SEC on November 15, 2016). |
4.1 | | Specimen Certificate for shares of common stock, par value $0.01 per share, of the Company (incorporated by reference to Exhibit 4.1 to the Company’s Amendment No. 2 to the Registration Statement on Form S-1/A (File No. 333-213504), filed with the SEC on October 3, 2016). |
4.2 | | Registration Rights Agreement, dated October 12, 2016, by and between the Company and Mammoth Energy Holdings, LLC (incorporated by reference to Exhibit 4.1 to the Company’s Current Report on Form 8-K (File No. 001-37917), filed with the SEC on November 15, 2016). |
4.3 | | Investor Rights Agreement, dated October 12, 2016, by and between the Company and Gulfport Energy Corporation (incorporated by reference to Exhibit 4.2 to the Company’s Current Report on Form 8-K (File No. 001-37917), filed with the SEC on November 15, 2016). |
4.4 | | Registration Rights Agreement, dated October 12, 2016, by and between the Company and Rhino Exploration LLC (incorporated by reference to Exhibit 4.3 to the Company’s Current Report on Form 8-K (File No. 001-37917), filed with the SEC on November 15, 2016). |
10.1 | | Advisory Services Agreement, dated as of October 19, 2016, by and between the Company and Wexford Capital LP (incorporated by reference to Exhibit 10.2 to the Company’s Current Report on Form 8-K (File No. 001-37917), filed with the SEC on November 15, 2016). |
10.2 | | Master Service Contract, effective May 16, 2013, by and between Muskie Proppant LLC and Diamondback E&P LLC (incorporated by reference to Exhibit 10.2 to the Company’s Registration Statement on Form S-1 (File No. 333-213504), filed with the SEC on September 2, 2016). |
10.3 | | Master Service Agreement, dated February 22, 2013, by and between Gulfport Energy Corporation and Panther Drilling Systems LLC (incorporated by reference to Exhibit 10.3 to the Company’s Registration Statement on Form S-1 (File No. 333-213504), filed with the SEC on September 2, 2016). |
10.4 | | Amendment to Master Service Agreement, dated as of May 23, 2016, by and among Gulfport Energy Corporation, Gulfport Buckeye LLC and Panther Drilling Systems LLC (incorporated by reference to Exhibit 10.4 to the Company’s Registration Statement on Form S-1 (File No. 333-213504), filed with the SEC on September 2, 2016). |
10.5 | | Master Service Contract, effective September 9, 2013, by and between Panther Drilling Systems LLC and Diamondback E&P LLC (incorporated by reference to Exhibit 10.5 to the Company’s Registration Statement on Form S-1 (File No. 333-213504), filed with the SEC on September 2, 2016). |
10.6 | | First Amendment, dated February 21, 2013, to Master Field Services Agreement, effective January 1, 2013, by and between Diamondback E&P LLC and Bison Drilling and Field Services LLC (incorporated by reference to Exhibit 10.6 to the Company’s Registration Statement on Form S-1 (File No. 333-213504), filed with the SEC on September 2, 2016). |
10.7 | | Master Field Services Agreement, effective January 1, 2013, by and between Diamondback E&P LLC and Bison Drilling and Field Services LLC (incorporated by reference to Exhibit 10.7 to the Company’s Registration Statement on Form S-1 (File No. 333-213504), filed with the SEC on September 2, 2016). |
10.8 | | Master Drilling Agreement, effective January 1, 2013, by and between Diamondback E&P LLC and Bison Drilling and Field Services LLC (incorporated by reference to Exhibit 10.8 to the Company’s Registration Statement on Form S-1 (File No. 333-213504), filed with the SEC on September 2, 2016). |
10.9 | | Master Service Agreement, dated June 11, 2012, by and between Gulfport Energy Corporation and Redback Energy Services LLC (incorporated by reference to Exhibit 10.9 to the Company’s Registration Statement on Form S-1 (File No. 333-213504), filed with the SEC on September 2, 2016). |
10.1 | | Master Service Contract, effective October 17, 2013, by and between Bison Trucking LLC and Diamondback E&P LLC (incorporated by reference to Exhibit 10.10 to the Company’s Registration Statement on Form S-1 (File No. 333-213504), filed with the SEC on September 2, 2016). |
10.11 | | Mammoth Energy Securities, Inc. 2016 Equity Incentive Plan (incorporated by reference to Exhibit 10.2 to the Company’s Current Report on Form 8-K (File No. 001-37917), filed with the SEC on November 15, 2016). |
10.12 | | Form of Option Agreement (incorporated by reference to Exhibit 10.12 to the Company’s Amendment No. 1 to the Registration Statement on Form S-1/A (File No. 333-213504), filed with the SEC on September 23, 2016). |
10.13 | | Form of Restricted Stock Unit Agreement (incorporated by reference to Exhibit 10.13 to the Company’s Amendment No. 1 to the Registration Statement on Form S-1/A (File No. 333-213504), filed with the SEC on September 23, 2016). |
10.14† | | Form of Director and Officer Indemnification Agreement (incorporated by reference to Exhibit 10.14 to the Company’s Amendment No. 2 to the Registration Statement on Form S-1/A (File No. 333-213504), filed with the SEC on October 3, 2016). |
10.15# | | Amended & Restated Master Services Agreement for Pressure Pumping Services Agreement, effective as of October 1, 2014, by and between Gulfport Energy Corporation and Stingray Pressure Pumping LLC (incorporated by reference to Exhibit 10.15 to the Company’s Registration Statement on Form S-1 (File No. 333-213504), filed with the SEC on September 2, 2016). |
10.16# | | Amendment to Amended and Restated Master Services Agreement, dated as of February 18, 2016 to be effective as of January 1, 2016, by and between Gulfport Energy Corporation and Stingray Pressure Pumping LLC (incorporated by reference to Exhibit 10.16 to the Company’s Registration Statement on Form S-1 (File No. 333-213504), filed with the SEC on September 2, 2016). |
10.17 | | Amendment to Master Service Agreement, dated as of July 7, 2016, by and among Gulfport Energy Corporation, Gulfport Buckeye LLC and Stingray Pressure Pumping LLC (incorporated by reference to Exhibit 10.17 to the Company’s Registration Statement on Form S-1 (File No. 333-213504), filed with the SEC on September 2, 2016). |
10.18# | | Sand Supply Agreement, effective as of October 1, 2014, by and between Muskie Proppant LLC and Gulfport Energy Corporation (incorporated by reference to Exhibit 10.18 to the Company’s Registration Statement on Form S-1 (File No. 333-213504), filed with the SEC on September 2, 2016). |
10.19# | | Amendment to Sand Supply Agreement, dated as of November 3, 2015, by and between Muskie Proppant LLC and Gulfport Energy Corporation (incorporated by reference to Exhibit 10.19 to the Company’s Registration Statement on Form S-1 (File No. 333-213504), filed with the SEC on September 2, 2016). |
|
| | |
10.2 | | Revolving Credit and Security Agreement, dated as of November 25, 2014, among Mammoth Energy Partners LP, Redback Energy Services LLC, Redback Coil Tubing LLC, Muskie Proppant LLC, Panther Drilling Systems LLC, Bison Drilling and Field Services LLC, Bison Trucking LLC, White Wing Tubular Services LLC, Great White Sand Tiger Lodging Ltd., Stingray Pressure Pumping LLC, Stingray Logistics LLC, collectively as the Borrowers, Mammoth Energy Inc. and Barracuda Logistics LLC, as the applicants, certain lenders from time to time party thereto and PNC Bank, National Association, as agent for the lenders (incorporated by reference to Exhibit 10.20 to the Company’s Amendment No. 1 to the Registration Statement on Form S-1/A (File No. 333-213504), filed with the SEC on September 23, 2016). |
10.21 | | Joinder Agreement, dated as of March 31, 2015, by and among Mammoth Energy Partners LP, Redback Energy Services LLC, Redback Coil Tubing LLC, Muskie Proppant LLC, Panther Drilling Systems LLC, Bison Drilling and Field Services LLC, Bison Trucking LLC, White Wing Tubular Services LLC, Great White Sand Tiger Lodging Ltd., Stingray Pressure Pumping LLC, Stingray Logistics LLC, collectively as the Borrowers, Mammoth Energy Inc. and Barracuda Logistics LLC, as the applicants, certain lenders from time to time party thereto and PNC Bank, National Association, as agent for the lenders (incorporated by reference to Exhibit 10.21 to the Company’s Amendment No. 1 to the Registration Statement on Form S-1/A (File No. 333-213504), filed with the SEC on September 23, 2016). |
10.22 | | Joinder Agreement, dated as of September 2, 2016, by and among Mammoth Energy Partners LP, Redback Energy Services LLC, Redback Coil Tubing LLC, Muskie Proppant LLC, Panther Drilling Systems LLC, Bison Drilling and Field Services LLC, Bison Trucking LLC, White Wing Tubular Services LLC, Great White Sand Tiger Lodging Ltd., Stingray Pressure Pumping LLC, Stingray Logistics LLC, Mammoth Energy Inc., Barracuda Logistics LLC, collectively as the Borrowers, Silverback Energy Services LLC, as applicant, certain lenders from time to time party thereto and PNC Bank, National Association, as agent for the lenders (incorporated by reference to Exhibit 10.22 to the Company’s Amendment No. 1 to the Registration Statement on Form S-1/A (File No. 333-213504), filed with the SEC on September 23, 2016). |
10.23 | | First Amendment to Revolving Credit and Security Agreement, dated as of September 30, 2016 by and among Mammoth Energy Partners LP, Redback Energy Services LLC, Redback Coil Tubing LLC, Muskie Proppant LLC, Panther Drilling Systems LLC, Bison Drilling And Field Services LLC, Bison Trucking LLC, White Wing Tubular Services LLC, Great White Sand Tiger Lodging LTD., Stingray Pressure Pumping LLC, Stingray Logistics LLC, Mammoth Energy Inc., Barracuda Logistics LLC and Silverback Energy Services LLC, collectively as existing borrowers, Mammoth Energy Services Inc., Redback Pumpdown Services LLC, Mr. Inspections LLC and Sand Tiger Holdings Inc., as new borrowers, the lenders party to the Credit Agreement from time to time, and PNC Bank, National Association, as a lender and agent for the lenders (incorporated by reference to Exhibit 10.23 to the Company’s Amendment No. 2 to the Registration Statement on Form S-1/A (File No. 333-213504), filed with the SEC on October 3, 2016). |
21.1* | | List of Significant Subsidiaries of the Company. |
31.1* | | Certification of Chief Executive Officer of the Registrant pursuant to Rule 13a-14(a) promulgated under the Securities Exchange Act of 1934, as amended. |
31.2* | | Certification of Chief Financial Officer of the Registrant pursuant to Rule 13a-14(a) promulgated under the Securities Exchange Act of 1934, as amended. |
32.1** | | Certification of Chief Executive Officer of the Registrant pursuant to Rule 13a-14(b) promulgated under the Securities Exchange Act of 1934, as amended, and Section 1350 of Chapter 63 of Title 18 of the United States Code. |
32.2** | | Certification of Chief Financial Officer of the Registrant pursuant to Rule 13a-14(b) promulgated under the Securities Exchange Act of 1934, as amended, and Section 1350 of Chapter 63 of Title 18 of the United States Code. |
101.INS* | | XBRL Instance Document. |
101.SCH* | | XBRL Taxonomy Extension Schema Document. |
101.CAL* | | XBRL Taxonomy Extension Calculation Linkbase Document. |
101.DEF* | | XBRL Taxonomy Extension Definition Linkbase Document. |
101.LAB* | | XBRL Taxonomy Extension Labels Linkbase Document. |
101.PRE* | | XBRL Taxonomy Extension Presentation Linkbase Document. |
| |
** | Furnished herewith, not filed. |
| |
+ | Management contract, compensatory plan or arrangement. |
| |
# | Confidential treatment with respect to certain portions of this agreement was granted by the SEC which portions have been omitted and filed separately with the SEC. |